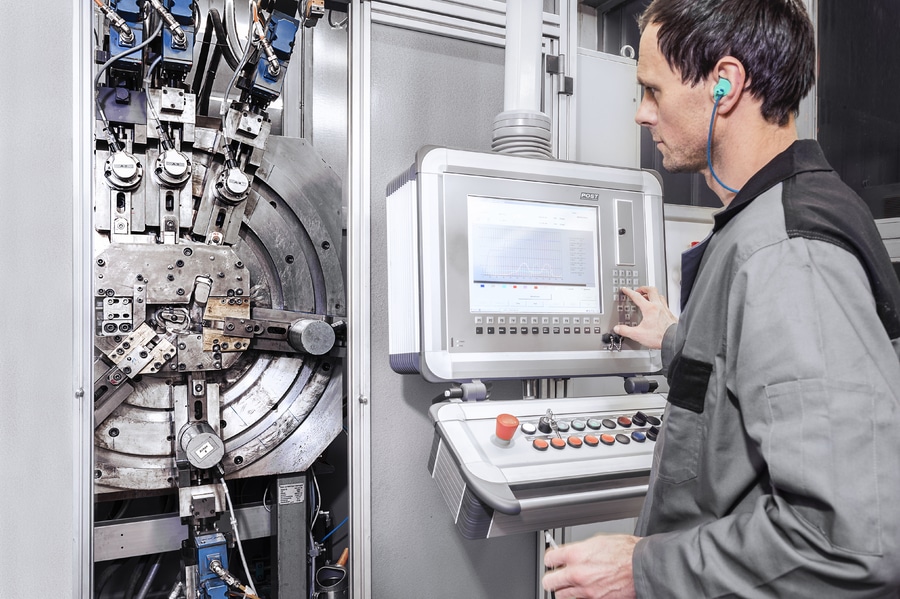
#Industry News
MES as a data hub
The Austrian metal processing company Schweiger Fulpmes has been using store floor and machine data acquisition for some time in order to be able to react quickly and flexibly to deviations in production. However, it was only with the implementation
Schweiger Fulpmes develops and produces rope clamps for ski lifts and cable cars, engine and gearbox parts for sports motorcycles and machine components for reaction technology. The product portfolio also includes steel and aluminum carabiners, belt buckles for mountain sports and safety technology as well as tools for wood shredders. The Austrian family business from Fulpmes in the Stubai Valley sees itself as a one-stop store for all processes, from product and process development to forging, CNC machining and surface treatment.
This vertical range of manufacture coupled with the variety of products requires modern machine and production data acquisition (MDE/PDA), explains Andreas Mussack, Head of Design & Development at the metal processing company: “We don't produce mass-produced goods. We therefore need to be able to react very flexibly and, above all, quickly to changes in production.”
First step towards Industry 4.0
The company uses the Enterprise Resource Planning (ERP) solution from the provider abas. “This has already opened up many opportunities for us in the direction of Industry 4.0,” says Andreas Mussack. As the software does not offer any machine data collection, it was necessary to
Page 2 of 4
the workers had to record the data on utilization rates, running times, quantities, etc. manually. This data was then transferred again manually so that it could be centralized for evaluation.
This process was lengthy and error-prone, Mussack recalls. It was also almost impossible to react quickly to malfunctions or downtimes. In addition, many machine manufacturers have their own MDC/PDC system for their machine control system, but these systems are incompatible with each other, so Schweiger Fulpmes was also unable to use one of these data acquisition systems. “We therefore looked for software that would allow us to connect all machine control systems,” says the design and development manager.
MDE/BDE digital and in real time
Schweiger Fulpmes was looking for a way to digitize the PDC/PDA with the help of an MES. The company wanted to identify the effects of specific interventions in the production processes more quickly by already integrating current operating and machine data when analyzing such interventions. This data should therefore also be available in real time.
After evaluating several solutions, the company finally opted for bisoftMES from gbo datacomp. “The software already covers the majority of our requirements with its standard functionalities,” says Mussack, explaining the decision. In addition, the flexibility and future viability of the MES was also important to the design and development manager. “Integrated interfaces such as OPC UA or MTConnect as well as the technical support from gbo datacomp ensured that we were able to connect our machines quickly,” says Mussack. Finally, the software costs were also a decisive factor. “bisoftMES is not bloated software where we pay for functions that we will never need,” says the design and development manager.
Step-by-step integration
After a few tests, during which the first optimization potentials were already visible, the project team went through the turning, milling and grinding areas in production together with the specialists from gbo in order to identify those where the use of the MES would offer the greatest advantages. The solution was then gradually integrated into production.
Operating and machine data is now digitized at Schweiger Fulpmes and automatically exchanged between the abas ERP software and the store floor. Here, bisoftMES acts as a data hub. The MES collects the data, consolidates it and visualizes it as key figures, for example for production planning or via dashboards in the production hall. At the heart of this is the interface to abas. “Once we had defined which data needed to be communicated to and from the ERP, gbo programmed the interface and everything has been running smoothly ever since,” summarizes Mussack. Instead of permanently transmitting all recorded data, only current machine and operating data is transmitted between abas and bisoftMES on the basis of reporting intervals. A REST interface was used for the interface, which ensures flexible adaptation of the data to be transferred.
More transparency, better analyses
As part of the digitalization project, Schweiger Fulpmes has succeeded in increasing transparency in production processes. “We now receive exactly the data we need directly from the machines,” explains Mussack. This has enabled the company to increase the overall effectiveness of the plant, as downtimes can be better evaluated and avoided. For example, a CNC processing machine repeatedly experienced downtimes for a few seconds, which were detected by the previous machine data acquisition system, but the causes remained unclear. It turned out that the processing axes were waiting until a component was placed on the plate instead of moving to the correct position beforehand. With a change to the programming, this step now takes place during the placement of the component.
The metal processing company has also succeeded in increasing the running times of the machines and systems in the third, unmanned shift. Here, for example, it happened time and again that deposit plates in processing machines signaled incorrect information about the components placed on them. “bisoftMES has solved the problem. Simply because we can now see the data clearly as key figures on the terminal, we can react more quickly,” adds Mussack. “After all, many of our workers are not directly at the machine, but operate it from a digital programming station.”
On the way to predictive maintenance
Schweiger Fulpmes now uses bisoftMES in its two production halls. According to Andreas Mussak, the solution provides very detailed key figures. The development manager wants to use these to determine the performance development of tools, for example, and thus further develop production planning in the direction of predictive maintenance. Mussack can also well imagine making the required production data available to all workers digitally in the future in order to be able to dispense with paper-based work instructions.