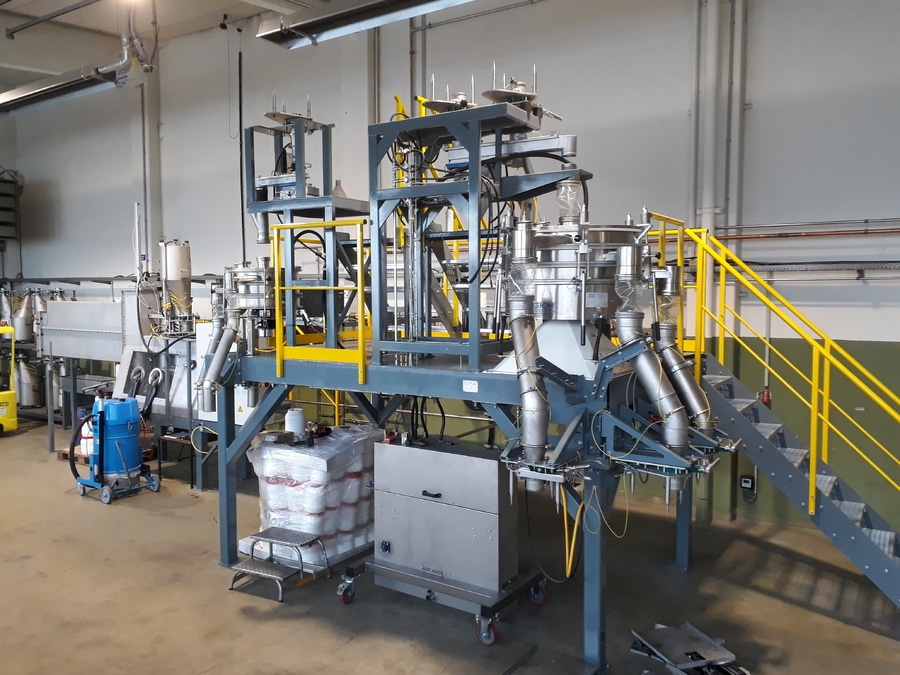
#Industry News
Tumbler Screening Machine for recycling of metal powder
Sieve technology in a processing plant for metal powder
Complex process steps are often required in order to produce materials with special properties. An example for a special plant would be the processing of metal powder. In this case high-quality alloys based on aluminum-titanium are processed, packaged and homogenized after previously being atomized in a vacuum melting process. A manufacturer of high performance metals and materials uses this special plant. The plant consists of several process steps: filling station, material container, screening plant, packaging plant and handling. The whole plant is a closed system and flooded with argon-gas as the metal powder gets damaged in contact with oxygen. In the first step - the filling station - the material is transferred from the containers of the vacuum melt into the material containers under argon atmosphere. The argon atmosphere is controlled during the complete process. Special materials containers were designed for process-reliable material handling and intermediate storage without interrupting the argon atmosphere. These material containers consist of an asymmetrical discharge cone so even heavily flowing material can be safely and completely discharged. The filled material containers can be rotated several times via a rotary mixer in order to homogenize the powder. The Tumbler Screening Machine of GKM Siebtechnik GmbH is the heart of the special plant. It was specially designed for the requirements of the metal powder screening without oxygen contamination. The material containers are installed above the Screening Plant and then fed through a closed vibrating conveyor into the screening machine. The material is screened into three fractions in order to scalp coarse particles and non-required fines. The argon supply operates fully automatically if needed. In order to remove even the ultrafine material up to 25 μm the screening machine is equipped with ultrasonic cleaning system. After the screening process and to deliver the product to the customers the material has to be filled into 6.4-liter plastic containers. These containers are connected to a filling station, which consists of a vibrating chute and a platform scale. The whole system is in a glove box with argon inertization. As a result the material is also protected during the filling or refilling process from oxidation. The operator closes the containers in the glove box after filling and pushes them into a discharge system with pneumatic lift and roller conveyor. The used weighing system is verifiable and has an automatic log memory so that every production batch can be traced.