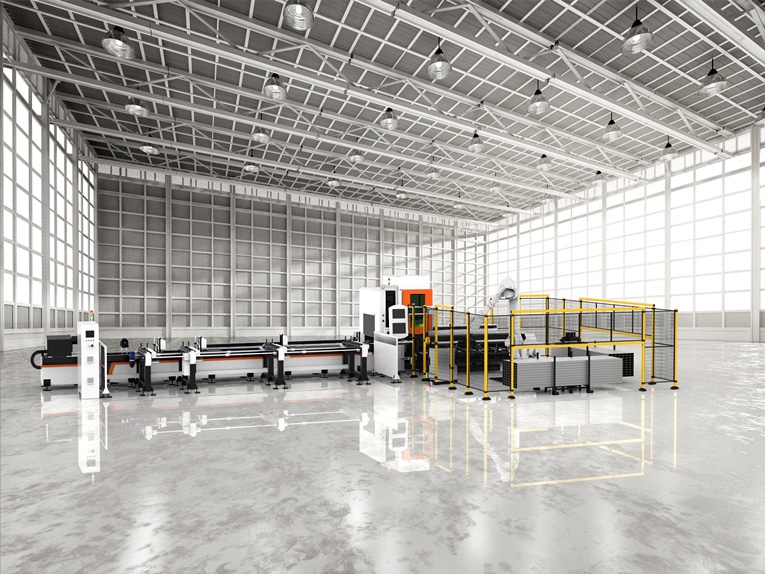
#Industry News
Customized Automated Laser Solutions: Flexible Laser Tube Processing Line for Scaffolding Manufacturing
Golden Laser works closely with you, supplying tailored design and engineering
Golden Laser’s customized automated laser solutions, particularly the Flexible Laser Tube Processing Line for scaffolding manufacturing, represent a significant advancement in the construction and manufacturing industries. Here’s an in-depth look at what this solution entails and its benefits:
Flexible Laser Tube Processing Line for Scaffolding Manufacturing
**1. Tailored for Scaffolding Needs
The processing line is specifically designed to meet the unique requirements of scaffolding manufacturing. This includes the ability to handle various tube sizes, shapes, and materials commonly used in scaffolding.
**2. High Precision and Efficiency
Golden Laser’s technology ensures high precision in cutting, drilling, and notching, which are critical for the structural integrity and safety of scaffolding. The automated system enhances efficiency by reducing manual labor and minimizing errors.
**3. Automated Loading and Unloading
The system includes automated loading and unloading features, which streamline the production process. This automation reduces the need for manual handling, thereby increasing throughput and reducing the risk of workplace injuries.
**4. Versatile Cutting Capabilities
The flexible laser tube processing line can perform a variety of cuts, including straight cuts, angled cuts, and complex geometries. This versatility is essential for creating the various components required in scaffolding systems.
**5. Integration with CAD/CAM Software
The system can be integrated with CAD/CAM software, allowing for seamless transition from design to production. This integration ensures that designs are accurately translated into physical components, reducing the likelihood of errors and rework.
**6. Real-Time Monitoring and Control
Advanced real-time monitoring and control systems are incorporated to ensure optimal performance. Operators can monitor the process, make adjustments as needed, and ensure that the production line is running smoothly.
**7. Material Optimization
The system is designed to optimize material usage, reducing waste and lowering costs. This is particularly important in scaffolding manufacturing, where material costs can be significant.
**8. Scalability and Flexibility
The processing line is scalable, allowing manufacturers to expand their operations as needed. Its flexibility means it can be adapted to produce different types of scaffolding components, catering to various project requirements.
Benefits for Scaffolding Manufacturers
Increased Productivity: Automation and high-speed processing significantly increase production rates, allowing manufacturers to meet tight deadlines and large orders.
Enhanced Quality: Precision cutting and consistent quality control ensure that each component meets stringent safety and quality standards.
Cost Savings: Reduced labor costs, material waste, and rework lead to significant cost savings over time.
Safety: Automated systems reduce the need for manual handling, thereby decreasing the risk of workplace injuries.
Customization: The ability to produce customized components allows manufacturers to cater to specific project needs and client requirements.
Conclusion
Golden Laser’s Flexible Laser Tube Processing Line for scaffolding manufacturing is a game-changer for the industry. By combining advanced laser technology with automation, Golden Laser provides a solution that enhances productivity, quality, and safety while reducing costs. This customized approach ensures that scaffolding manufacturers can meet the demands of modern construction projects efficiently and effectively.