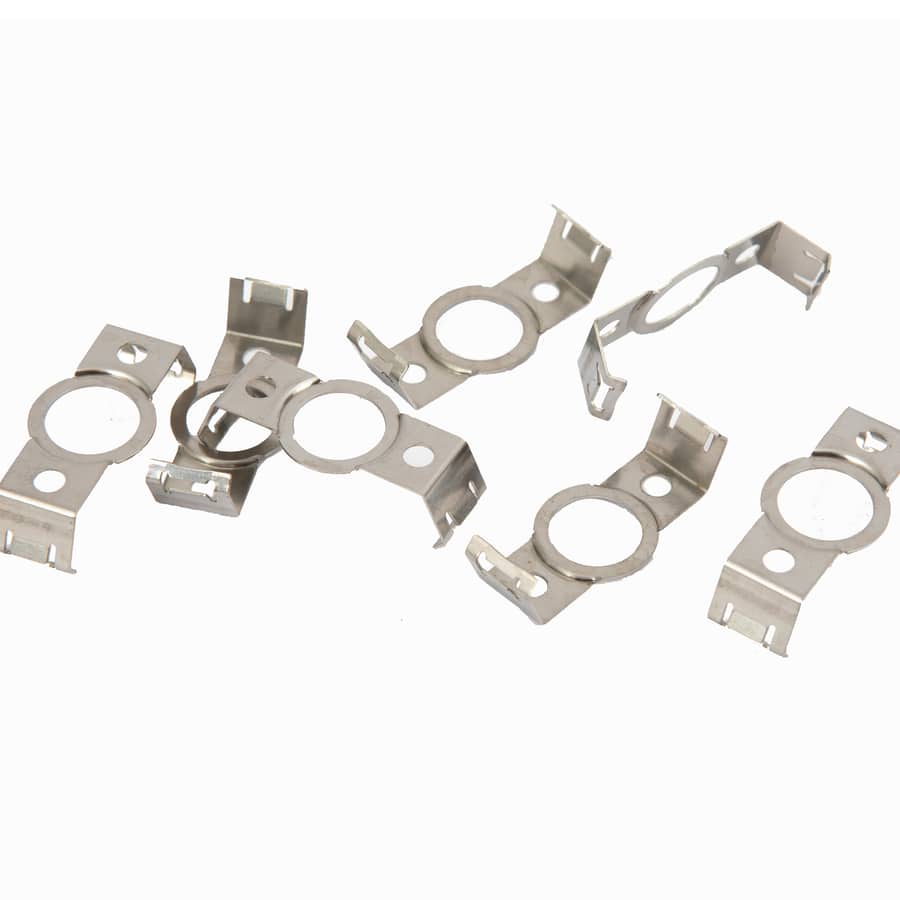
#Industry News
What is the difference between passivation and anodising of aluminium alloys?
Passivation of aluminum alloy is the direct reaction between aluminum alloy and liquid to form a passive film to improve the corrosion resistance and adhesion. Anodic treatment is to apply electric field to form an oxide film on the metal.
By chemical or electrochemical methods, the state of metal surface changes, the dissolution rate drops sharply, and the corrosion resistance is improved. This process is called passivation. Passivation is often accompanied by a sudden increase in anode potential, which makes the anodic reaction difficult to carry out and makes the metal corrosion slow down or stop. Because passivation can significantly improve the corrosion resistance of metals, it is widely used in machinery, electronics, instruments, daily necessities, military equipment and other fields.
Anodization, a metal surface treatment process, metal materials in the electrolyte solution, through the external application of anode current to form an oxide film on the surface of a material protection technology. Also known as surface anodization.
After surface anodization, the corrosion resistance, hardness, wear resistance, insulation and heat resistance of metal materials or products are greatly improved. Aluminum is the most important metal material for anodizing. Anodization of aluminum is usually carried out in acidic electrolyte, with aluminum as anode. In the process of electrolysis, the anion of oxygen reacts with aluminum to form oxide film. Although there is a certain resistance, the negative oxygen ions in the electrolyte can still reach the surface of aluminum and continue to form oxide film. With the increase of film thickness, the resistance also increases, so the electrolytic current decreases. At this time, the outer oxide film in contact with the electrolyte is chemically dissolved. When the rate of oxide formation on the surface of aluminum is gradually balanced with the rate of chemical dissolution, the maximum thickness of the oxide film can be reached under this electrolytic parameter. The outer layer of anodic oxide film of aluminum is porous and easy to absorb dyes and colored substances, so it can be dyed to improve its decoration. The corrosion resistance and wear resistance of the oxide film can be further improved after sealing by hot water, high temperature steam or nickel salt. In addition to aluminum, magnesium alloy, copper and copper alloy, zinc and zinc alloy, titanium alloy, steel, cadmium, tantalum, zirconium, etc. are used for surface anodization in industry.