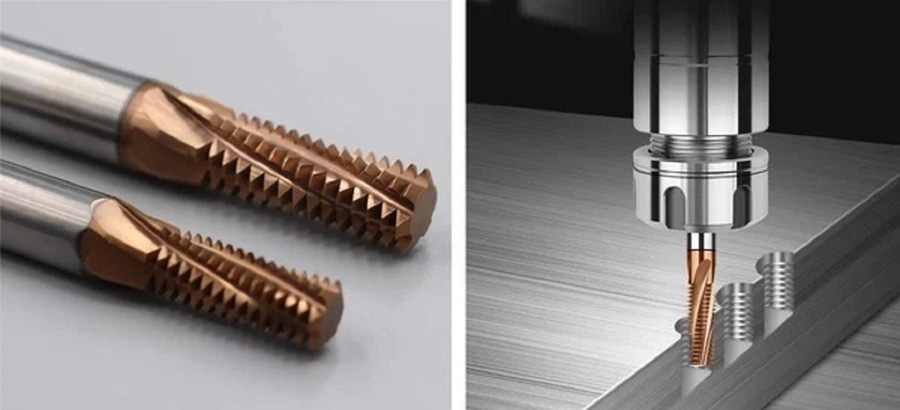
#Industry News
Types Of Machining Processes
10 Basic Types
Machining is a subtractive manufacturing process that shapes and finishes a workpiece by removing material from it. Mainly including ten types of milling, turning, drilling, grinding, planing, sawing, broaching, laser cutting, electrical discharge machining (EDM), and electrochemical machining (ECM).
1. Milling is a typical subtractive manufacturing process used to shape solid materials by removing excess material using rotating tools. It involves the use of a cutting tool called a milling cutter, which has multiple cutting edges.
2. Turning is a basic machining operation used to make cylindrical parts by removing material from the surface of the workpiece using cutting tools. This process is usually done on a lathe. During machining, the workpiece is clamped and rotated at a controlled speed while the cutting tool held in place moves parallel to the axis of rotation.
3. Drilling is the most common hole processing method, which forms a hole by rotating a drill bit on the workpiece and applying pressure. Drills are cutting tools used for drilling holes, and common types include twist drills, center drills, and deep hole drills. These tools are usually made of high-speed steel to provide adequate cutting speed and durability.
4. Grinding refers to the process of using abrasives to remove material from the surface of a workpiece. Achieving extremely high machining accuracy and capable of producing workpieces with surface roughness Ra≤0.1μm. The grinding wheel is the main abrasive tool in the grinding process. When the abrasive grains on the surface of the grinding wheel come into contact with the workpiece, they create micro-cuts in the material. Altering its shape, size or surface finish to meet specific requirements.
5. Planing is a cutting method that uses a planer to produce horizontal reciprocating motion on the workpiece. It is mainly used to shape the external features of parts, including bevels, stepped surfaces and grooves. Using planing processing, the processing accuracy can reach IT10~IT8, the surface roughness (Ra) can reach 6.3~1.6um, and the straightness can reach 0.04~0.12mm/m.
6. Sawing is a machining process that involves the use of a serrated or toothed cutting tool (usually a saw blade) to cut material and form a desired shape or individual workpiece. Traditionally, sawing has been associated with rapid material removal, often at the expense of precision. However, modern technology, especially CNC sawing, allows for high-precision cutting with minimal material waste.
7. Broaching is a processing technology that uses a broaching machine (broach) to form various internal and external surfaces. Broaches usually have a series of teeth or cutting edges arranged in a progressive fashion. The surface is formed and processed in one step to achieve high processing accuracy. Due to its complex structure, high manufacturing costs, and specialization, broaching is mainly used in high-volume production.
8. Laser cutting does not involve physical cutting tools. Instead, it utilizes a high-power-density laser beam to directly melt, burn, or vaporize materials. As the beam moves across the material, it creates a continuous narrow slit (usually about 0.1 mm wide), thereby completing the cutting or engraving of the material.
9. Electrical discharge machining (EDM) is a non-traditional machining process that uses electric discharge (sparks) to remove material from a workpiece. EDM is not limited by material hardness and is only suitable for conductive materials. It has extremely high precision and is widely used in the field of mold manufacturing.
10. Electrochemical machining (ECM) is a non-traditional processing method that uses electrochemical reactions to process metal materials. By harnessing the action of an electrolyte medium and an electric current, it dissolves metal surfaces by controlling the current density between the anode (workpiece) and cathode (tool).