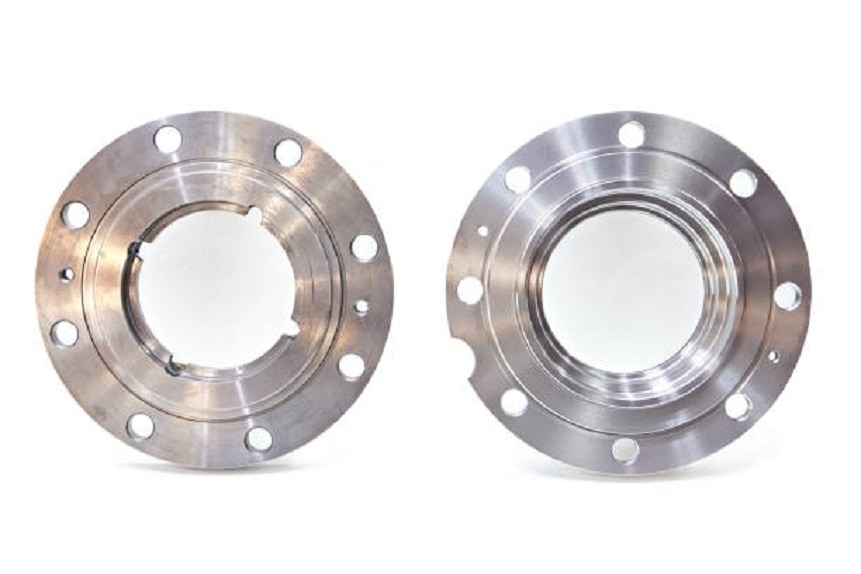
#Industry News
Common Types of Flanges
6 common flange types
Choosing the right flange type ensures a good match between the piping system and the equipment, thereby improving the efficiency and safety of the system. This article will introduce six common types of flanges, their characteristics, and their application scenarios.
1. Threaded Flange
Threaded Connection: Threaded flanges have internal or external threads, which can be used with threaded pipes or other threaded fittings, simplifying the installation process.
Easy Installation: Due to the simplicity of threaded connections, threaded flanges are relatively easy to install without welding equipment and are suitable for situations where welding is inconvenient.
2. Weld Neck Flange
Long Neck Design: Weld neck flanges have an extended neck design, typically longer than other flanges, providing better strength and rigidity.
Welding Performance: The neck of weld neck flanges can be directly welded to the pipeline, offering better connection strength and sealing performance.
Reduced Stress: Due to the neck design of weld neck flanges, the stress at the weld joint and pipeline connection is reduced, helping to alleviate stress on the pipeline system.
Suitable for High-Pressure Systems: Weld neck flanges are typically used in high-pressure or high-temperature pipeline systems due to their structural design and welding method.
3. Slip-On Flange
Simple Installation: The design of slip-on flanges makes them easy to install; simply slide the flange onto the end of the pipe and weld it without the need for complex operations.
Low Cost: Compared to other flanges, slip-on flanges have relatively low manufacturing costs, making them more economically priced.
Suitable for Low-Pressure Systems: Slip-on flanges are typically used in low-pressure, low-temperature, or non-critical applications in pipeline systems.
4. Socket Weld Flange
Socket Weld Connection: Socket weld flanges have an inwardly concave interface, which can be used for socket weld connections, making the connection between the flange and the pipe more robust and sealed.
Simple Structure: The structure of socket weld flanges is relatively simple and easy to process and manufacture, resulting in relatively low manufacturing costs.
Space Saving: The design of socket weld flanges allows the welding joint to be located inside the flange, saving space in the pipeline system.
5. Lap Joint Flange
Flat Connection: Lap joint flanges have a flat connecting surface and must be used with a flat end section of the pipe, creating a loose connection between the flange and the pipe.
Adjustability: The connection between lap joint flanges and the pipe is not tightly fixed but relatively adjustable through the combination of bolts and flanges, offering a certain degree of adjustability.
Simplified Maintenance: Due to the loose connection, lap joint flanges are relatively easy to disassemble and replace, which helps simplify the maintenance and repair of the pipeline system.
6. Blind Flange
Closing Pipeline End: Blind flanges are used to close the end of pipelines, preventing media leakage or external substances from entering the pipeline system.
Non-Perforated Design: Blind flanges are typically non-perforated, meaning they have no pipe or bolt holes, ensuring complete pipeline sealing.
Reliable Sealing: Due to their non-perforated design, blind flanges provide reliable sealing performance, ensuring the safe operation of the pipeline system.
Choosing the appropriate flange type is crucial for ensuring the effective operation of a piping system. Different types of flanges have various advantages and disadvantages in terms of connection methods, installation difficulty, cost, and suitable scenarios. Understanding these characteristics can help make more informed decisions in practical applications.
To learn more about flanges and more types of flanges, please click on the link below.