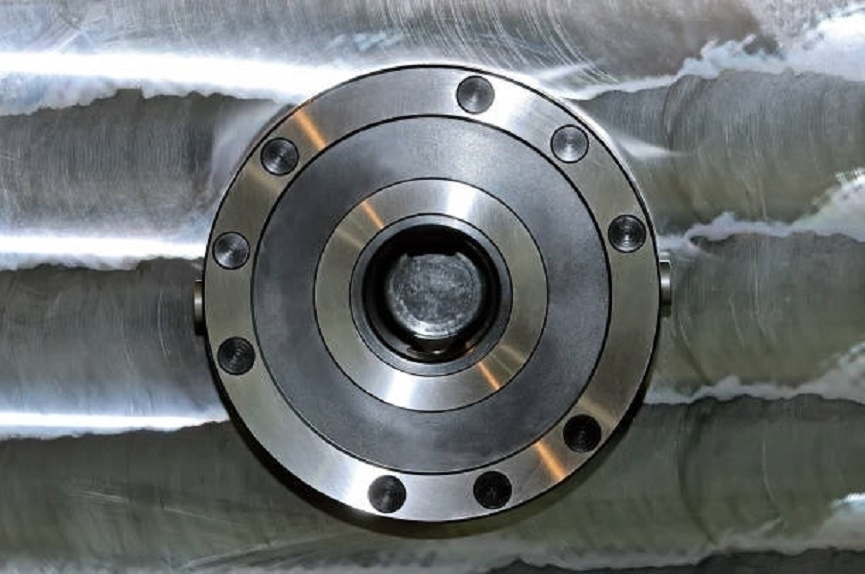
#Industry News
What Is Passivation?
How is Passivation carried out?
Passivation is a chemical process used to reduce the reactivity of materials, especially metals, to enhance their corrosion resistance. The principle of this treatment is to form a protective oxide layer on the metal surface, which acts as a barrier to prevent further oxidation and corrosion.
Stainless steel is one of the most commonly passivated materials. Without passivation, stainless steel is more susceptible to corrosion. Stainless steel contains chromium, which forms a thin protective oxide layer on its surface. However, this oxide layer can be damaged by contaminants such as dirt, grease or processing residues, leading to localized corrosion, rust and pitting. Without passivation, the protective oxide layer may not form adequately or may be damaged over time, reducing the corrosion resistance of the material and potentially shortening its service life in corrosive environments.
Steps to passivation
1. Surface cleaning
Proper cleaning and surface preparation are essential for successful passivation. Before starting the passivation process, the metal surface should be thoroughly cleaned of any contaminants, oil, grease or scale. Alkaline cleaners can be used to break down oil and grease, solvents can be used to dissolve and remove specific contaminants, or scale and rust can be physically removed by mechanical methods such as brushing, sandblasting or grinding. The goal is to achieve a cleanliness level of ISO 8501-1 Sa 2.5 or higher, ensuring that all organic and inorganic contaminants are removed.
2. Pickling
After cleaning, pickling is performed to remove surface oxides, scale and discoloration, especially those in welds. The stainless steel is immersed in a pickling solution of 10% to 25% nitric acid at a temperature of 120°F to 160°F (50°C to 70°C) for 15 to 30 minutes. This step ensures that embedded iron and other contaminants are removed, providing a clean, active surface for passivation.
3. Passivation
The appropriate passivation method is selected based on the specific requirements of the metal type, composition and application. Common passivation methods are chemical immersion, spraying or wiping with a passivating agent. Passivation is the process of forming a protective oxide layer on the surface of stainless steel, which is achieved by treating the cleaned and pickled surface with a decontamination solution. Choose a passivation solution reagent that is compatible with the metal being treated and meets relevant industry standards and regulations. The concentration and temperature of the passivation solution should also be carefully controlled for best results: the composition is 20% nitric acid, the temperature is room temperature (approximately 70°F to 90°F or 20°C to 30°C), and the duration is 20 to 30 minutes.
4. Rinse and dry
After passivation, all residual acid or contaminants must be removed. Rinse thoroughly with clean water to eliminate any residual chemicals, and then use a blower or drying oven to dry the components, ensuring that they are completely dry and free of any residual moisture that may cause corrosion.
Take appropriate safety precautions when handling passivation chemicals, as many passivation solutions contain potentially harmful acids. Ensure good ventilation, use personal protective equipment (PPE) such as gloves and goggles, and follow safety guidelines to prevent accidents or exposure to harmful fumes.
Through the above steps, the passivation process can significantly improve the corrosion resistance of metal materials, extend their service life, and ensure their reliability in a variety of application environments. If you want to learn more about passivation, please click the link below to view the original article.