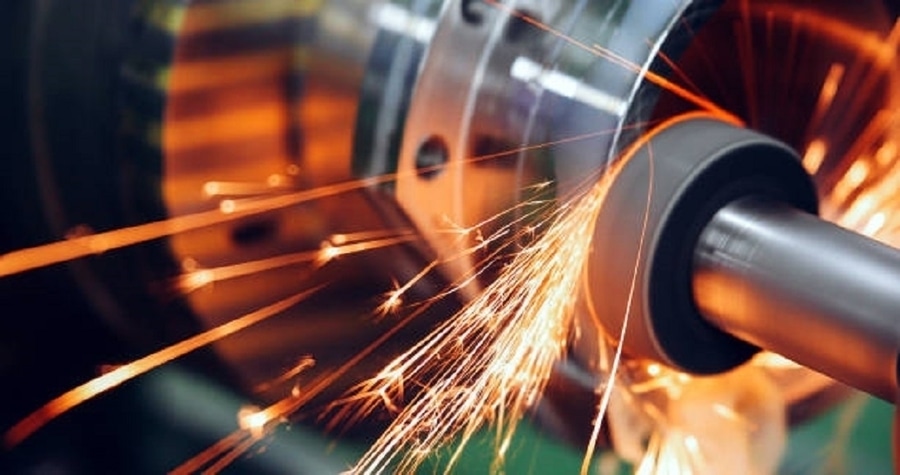
#Industry News
Surface Grinding
Process Details, Types and Applications
Surface grinding is an important machining process that uses a rotating grinding wheel with coarse grains to remove material from the surface of the workpiece to obtain a smooth and flat surface. Surface grinding can achieve high-quality surface treatment results for both metal and non-metallic materials.
Classification of surface grinding
According to the DIN 8589-11 standard, surface grinding is classified as a face-peripheral-longitudinal grinding process and is widely used in industrial production. Depending on the relative position of the grinding wheel to the workpiece surface, this process can be subdivided into:
1.Face-peripheral-longitudinal grinding
2.Face-peripheral-cut grinding
3.Face-longitudinal grinding (face grinding)
The process flow of surface grinding
Surface grinding includes several key steps, each of which is crucial to the accuracy and finish of the final product.
Workpiece selection: Determine the workpiece material to be ground, which can be metal, ceramic or other materials that require a smooth surface.
Mounting the workpiece: Secure the workpiece firmly to the grinder to ensure that it does not move during the grinding process.
Select grinding wheel: Select the appropriate grinding wheel based on the workpiece material and the desired surface finish.
Set up the grinder: Adjust the grinder parameters, including grinding wheel speed, depth of cut, and ensure proper alignment of the workpiece and grinding wheel.
Start grinding: Start the grinding process and bring the grinding wheel into contact with the workpiece surface to begin material removal.
Control feed rate and depth of cut: Remove material from the workpiece surface gradually by adjusting the feed rate and depth of cut. The feed rate determines how fast the grinding wheel moves over the workpiece surface, and the depth of cut determines the amount of material removed with each grinding pass.
Monitor and adjust: During the grinding process, use precision measuring tools (such as a micrometer or surface roughness gauge) to monitor the surface quality and size of the workpiece and adjust the grinding parameters as needed.
Final inspection: After grinding, inspect the surface of the workpiece to ensure that it meets the requirements for flatness, smoothness, and dimensional accuracy.
Clean the work area: Clean the grinder and work area to remove all debris and residues generated by the grinding process.
Applications of Surface Grinding
Surface grinding is widely used in many industrial fields, especially in manufacturing processes that require high precision and flatness. Its applications include but are not limited to electronic equipment, medical devices, automotive parts, and aerospace components.