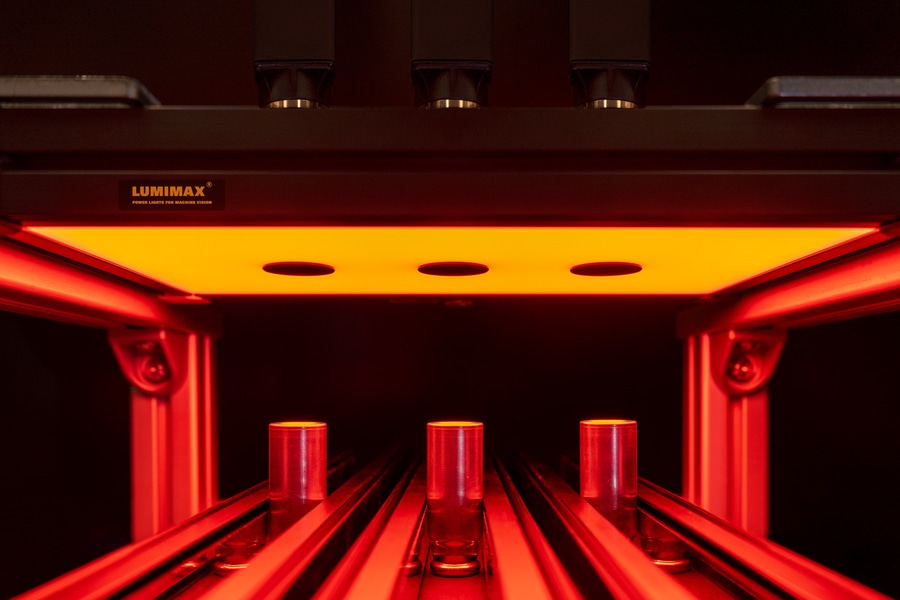
#Industry News
Flexible LUMIMAX ML Area Lights
Efficient solutions for individual image processing requirements
Special lighting solutions are always in demand if particular application-specific requirements have to be met regarding sizes, light characteristics, durability or similar. However, such products are generally costly and require a great deal of time depending on complexity and development cost. The flexible concept behind the new LUMIMAX ML Area Lights (ML = modular lighting) is useful here. Thanks to its modular design, customised amendments to the size, form and lighting characteristics for development can be implemented quickly without additional costs. The ML range therefore fills the gap between readily available standard products and intricate special products.
With LED Area Lights of the ML series, LUMIMAX now has a new flexible illumination concept in its product range. Whilst it looks like a simple area light for Machine Vision applications on first glance, it is actually the foundation for far more complex lighting solutions. Its modular design makes it possible to design customised lighting solutions without requiring a great deal of time or sky-high development and procurement costs. Furthermore, the design allows for illumination sizes of up to 1 m² and more. This enables considerably larger detection areas than ever before to be reliably illuminated, even from greater distances.
The length and width of the lighting can be freely customised in 50 mm increments. As well as simple square and rectangular designs, it is possible to create special shapes such as L-shapes, U-shapes or frame lighting with a rectangular gap. Classic round camera holes can also be flexibly positioned in the light field. For example, complete test stations including several cameras can be illuminated evenly with the aid of a large area light. The arrangement of the LEDs ensures homogeneity of the whole light field right up to the very edges of the illumination.
Although the new ML Lighting series has not been on the market for long, it has already been used to resolve a few complex applications. Here are two customer-based applications that illustrate how flexible this new range of lights is in terms of integration. Together with MM-SmartMachine, a specialist machinery manufacturer, a production facility was optimised for pre-assembling coffee capsules after the client had discovered a problem within quality control. The facility consists of one or two-lane machines with an intake of eight or 16 components. Due to the image processing system, a maximum of 16 different parts were checked per cycle, with 45 cycles taking place per minute. At this point, the control station carries out various quality checks on coffee capsules with filter paper. As well as checking weld seams, the filter paper is also checked for holes, errors, dirt and any snippets of paper that may be present. The scratchings on the dome of the plastic part are also inspected during the test process. With the previous system, the process time for the entire quality assurance was 1.2 s for analysis of all 16 components, including transmission of the result to the software that was used. However, the old PC-based camera system caused sporadic breakdowns and led to quality issues due to image shift. This resulted in assessment results that did not apply to the actual component. As the required quality factors could not be recognised with the naked eye, such malfunctions were often recognised too late, leading to repeated production losses and high costs. Furthermore, technical support for the old system, dating back to 2006, was no longer available from the previous systems supplier. Acquiring the necessary replacement parts was also only possible to a limited extent. In general, it was no longer possible to properly maintain the production facility.
The project objective with MM-SmartMachine was therefore to implement a new image processing system that offered state-of-the-art technology, remote operation and potential for extending testing. As you would expect, there were several challenges to overcome. On the one hand, no changes could be made to the structure of the existing production facility. Hence, it was necessary to develop a perfectly fitting area light for the available slot, as standard lighting would not cover the entirety of the housing in question.
Modular Area Lighting from the LUMIMAX ML series was chosen. The lighting housing consists of aluminium profiles instead of fully milled aluminium assemblies, which ensures greater flexibility in terms of sizes. The available installation space was so limited that the area lighting also had to be fitted with a particularly narrow frame on two sides. As a result, maximum light output can be ensured despite the compact installation conditions. Generally, a single or double-sided narrow edge is available on request for particularly compact designs on all sizes of the ML Lighting series.
Another structural challenge was the current linear transfer system, which produces dark spots in different positions and therefore prevents homogeneous lighting of the tested parts. A deliberate brightness curve was created within the area light to balance out this inhomogeneity. Amongst other things, special tests and corresponding adjustments were required at the client’s premises in the USA. This counterbalanced the changing light conditions so that all 16 components could be checked at the same time and also be evaluated with the software in use with just a single camera setting. A position-based image acquisition is therefore no longer necessary.
As is often the case within industrial automation, it is a very fast inspection process, therefore other factors must be taken into account when optimising the image processing system. The quality check should not slow down the production of coffee filters. In order to allow for images and evaluation of test images to take place whilst in motion, area lights are operated in flash mode. Flash lighting is not merely orders of magnitude brighter: when the trigger signal is sent, the maximum light output of the illumination is available within a period of time measurable in single-digit microseconds. This quick availability in conjunction with enormous luminous intensity means a very short exposure time can be set on the camera. Movement of the 16 test objects can essentially be frozen. For the human eye and the camera, the moving objects seem to come to a complete stop. The new image processing system now creates all 16 component images, including evaluation within 560 ms. In general, the user was able to improve quality assurance and minimise production losses.
The flexibility of the LUMIMAX ML series was also a benefit in another case study. A Machine Vision solution was developed for the company Netstal together with IMD AG, a Swiss provider of industrial measurement and inspection systems within the plastic packaging materials sector. Netstal is also based in Switzerland and is a worldwide leader in the manufacture of injection-moulding machinery for preforms (bottle blanks), seals in both the food and non-food sectors, thin-walled and IML packaging and medical products. A new generation of systems for monitoring production had to be developed for the PET preforms sector. In this case, the image processing system is used for checking various parameters and potential defects in terms of colour and shape. For example, black dots, air bubbles and stains may occur. A phenomenon known as short shots can also take place. These are incomplete material injections, which become clear at the top of the thread and mean that the bottle is not watertight. The counterpart to these is known as long gates, which means that the injection point is too long.
A backlight application was developed that could be fully integrated into the production process in order to best monitor the preforms in line with the aforementioned quality criteria. The PECO LUX system consists of a sliding surface that is backlit, above which several cameras are arranged that inspect the bottle blanks in transmissive light. Whilst the previous model consisted of two smaller sliding surfaces, the latest generation now has one continuous area. This increases the homogeneity of the lighting, which was a key requirement of the application. In addition, the backlit slides are required in differing widths, as they are directly integrated into the system so that they fit the relevant injection-moulding machine. Three different sizes are currently in use. The flexibility of the LUMIMAX ML series came to the fore once again – even on a larger scale. Currently, the largest illumination that is required has an active light field of 1,100 x 300 mm, as well as a considerably lower weight relative to comparable lighting fields. As a result of the continuous, larger sliding surface and the increased number of cameras, the inspection rate – the ratio between produced and inspected preforms – was increased. This aspect is of particular importance on injection-moulding machines with large tools. In addition, replacing the older, smaller lighting for the new, larger area lighting resolves the problem where test objects are stored on the central bar, where previously the two lights bumped into each other. As the bottle blanks are checked when in motion and when sliding through the area light, the lighting specialists at LUMIMAX also chose flash mode for this application. As a result, the system also benefits from the aforementioned benefits of high light output and the standstill effect of the sliding preforms.
In summary, the optimisation of PECO LUX brought about improvements in the entire testing process, whilst calibration of the system is simpler and more accurate. Thanks to the large, continuous lighting solution, a very high degree of homogeneity is ensured along with maximum brightness. Other light sizes can be implemented quickly and easily where required due to the flexible design based on aluminium profiles.
Both described applications show once again that lighting often has to satisfy extremely specific requirements within the field of industrial image processing. With the aid of the LUMIMAX ML series, an alternative was created that provides fast solutions whilst keeping development costs and time low. The modular design means that the lighting developer now has a practical basic model that can be readily adapted and used to resolve mechanical challenges in a simpler manner. Approximately 60% of the development work can be saved per project. This allows for short delivery times and better pricing conditions. The lighting housing is made of aluminium profiles, providing a range of benefits such as good availability, lower manufacturing costs and greater flexibility in terms of design. A T-shaped groove (size 5) on the circumference of the housing simplifies handling as well as mechanical integration into industrial environments, even with larger lighting areas.
Electrical commissioning is simple whilst saving resources thanks to the integrated controller technology, as well as the standardised M16 push-in connector. Switch signals can, like the output, also be provided via a single cable. Even with larger lighting areas, high light outputs can provide bright, highly contrasting images and therefore ensure reliable, reproducible implementation of test applications.
In order to keep all options in mind, a range of product configurations can be seen on the LUMIMAX website, via which many typical test applications can be realised. In addition, many adjustments can also be made to your specific machine vision applications.
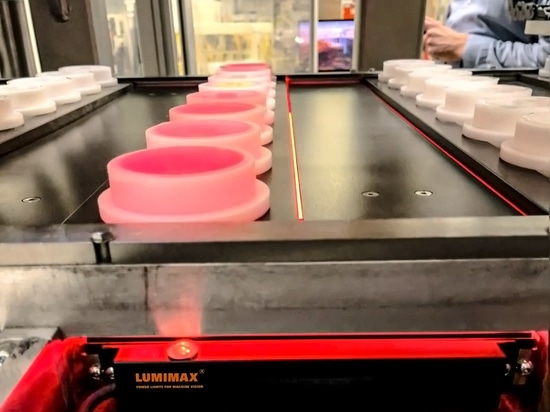
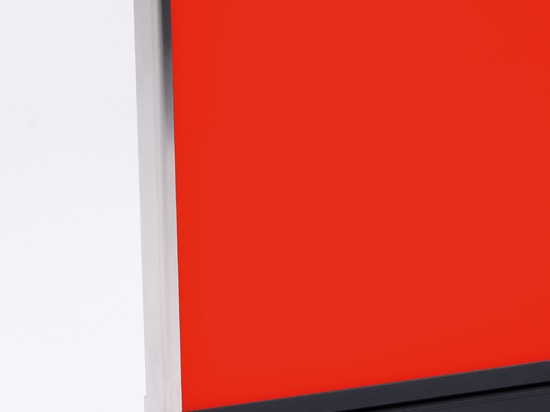
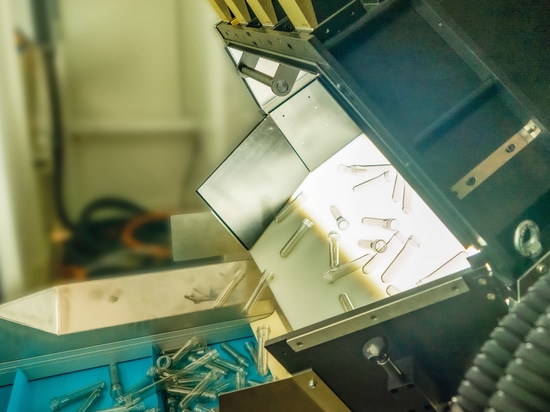