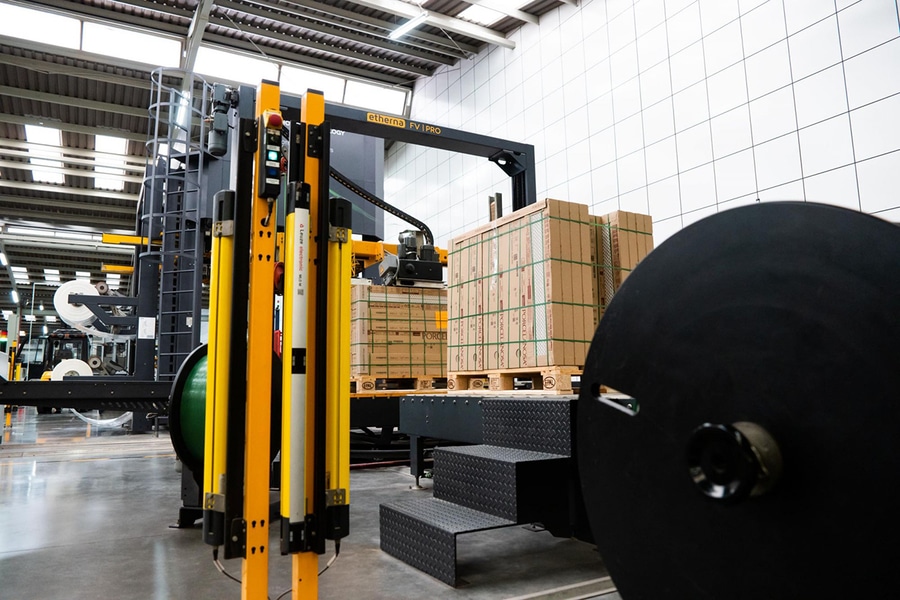
#Industry News
Strapping Systems Guide
Strapping Systems Guide: Keys to choose an Automatic Strapping System
Deciding what type of Automatic Strapping system we need is not as simple as it may seem, since the safety of our cargo during transportation and handling will depend on it. Strapping is especially important in grouping boxes, packages or bulky packages, fragile and/or heavy loads, and mainly unstable loads. Therefore, choosing a specific Strapping System affects not only the packaging process itself but also the company’s profitability since it will reduce losses and prevent accidents in the loads transport.
In this article, we will analyze the aspects to consider before buying an Automatic Atrapping Machine for pallets or boxes, to optimize our end-of-line and logistics process.
FACTORS TO TAKE INTO ACCOUNT IN AUTOMATIC STRAPPING
Choosing the right automatic pallet strapping machine is not a simple task. There are several options on the market, each with its characteristics and applications, and the final decision will depend on several crucial factors that will determine the efficiency, safety, and costs of your packaging process. The following factors are listed below.
1. PRODUCT TYPE, CHARACTERISTICS, AND CONDITIONS
The first and most important point is everything related to the load and its characteristics (format, weight, fragility, quantity, etc.). By analyzing these aspects, we can orient ourselves to look for strapping systems that are compatible with the load.
- Type of load: Solid, liquid, or gaseous product formats, fragile, delicate, or robust products, etc. The type of strapping and strapping tension depends, to a large extent, on the nature of the product. For example: in the case of boxes with heavy but fragile material, it is important to strap horizontally but also vertically to join the load to the base.
- Dimensions and weight: What are the dimensions and weight of the products or packages to be strapped? Knowing this data is important to determine the load capacity of the pallet strapping machine. For example: high and unstable loads (such as drums, stacked boxes, etc.) will require vertical strapping or a similar restraint system (such as a stretch wrapper with a strap applicator).
- Product surface: Is the product surface smooth, rough, or uneven? The surface texture can affect the adhesion of the strap and the need for edge protectors or other protective materials as well as the handling, transportation and storage conditions throughout the logistics process.
- Exposure conditions: What environmental conditions will the products be exposed to during transportation and storage? If there is a risk of humidity, dust, extreme temperatures or chemical agents, a strap resistant to these conditions should be chosen. For example, when stored outdoors for long periods of time, strapping may lose tension.
2. HANDING, TRANSPORT AND STORAGE CIRCUMSTANCES
Concerning transport and handling, it is necessary to ask ourselves some questions about the entire path of our cargo. The necessary strapping tension, the choice of strapping type and the need for additional protective materials such as corner protectors or other safety accessories are directly and indirectly affected by these circumstances:
- Handling: How will the products be handled? Will they be moved manually, with a pallet truck, forklift, or AGV? How many workers do we have? How much working space do we have?
- Transportation: Will we use land, sea or air transportation? Will it be short or long distance?
- Storage: How will the products be stored: on shelves, stacked on the floor, or in containers? Will the environment be wet or dry?
There are several levels of strapping: first-level strapping (strapping the box or package) and second-level strapping (strapping the product to the pallet). It is recommended to strap the load on both levels for maximum efficiency.
At Innova, we offer automatic box strapping systems that also incorporate vertical pallet strapping technology, a more precise solution for box and pallet securing.
3. TYPES OF STRAP: CHARACTERISTICS AND APPLICATIONS
If our cargo is robust and bulky, we cannot use a strap with inferior characteristics. The load will not be well protected and will suffer significant damage. In this section, we will talk about the four types of strap: PET, polypropylene, polyester, and textile, briefly summarizing the characteristics of each one and their applications to choose the best material for our cargo.
1. POLYPROPYLENE (PP) STRAP
PP or Polypropylene strapping is economical, versatile, flexible, and adaptable. It is the most common choice due to its low cost (much cheaper than PET). It is moisture resistant, making it ideal for humid or temperature-changing environments, and it is also highly resistant to corrosive environments.
Applications:
- Box and pallet packaging (irregular loads, different formats, etc.).
- Indoor and outdoor use.
- Ideal for light and medium loads.
2. POLYESTER (PET) STRAP
PET or Polyester strapping is extremely resistant, so it is recommended for heavy loads and demanding conditions since it is highly resistant to humidity, chemical products and abrasion. It offers great holding capacity, adapting to the shape of the load. It is mainly used in palletizing, ceramic products and construction materials. A great advantage it offers is that it can be applied 100% automatically.
Applications:
- Palletizing of heavy products.
- Packaging of building materials and ceramic products.
- Ideal for loads that require a firm and resistant fastening.
3. STEEL STRAP
This type of strapping offers maximum strength, supporting extremely heavy loads. It has high stiffness and strength, so it is recommended for demanding conditions.
Like PET strapping, it also has abrasion resistance and low elongation and generally has a waxed finish to avoid strapping problems. Their cost is much higher than polypropylene or polyester strapping, so usually, if the load is not so extremely heavy, PET strapping is resorted to.
Applications:
- Steel and construction industry.
- Packaging of heavy machinery and bulky products.
- Ideal for loads that require maximum security and resistance.
4. TEXTILE STRAP
This is a sustainable and environmentally friendly strap that usually replaces steel strapping. Like steel strapping, it offers high strength, as well as elasticity and great adaptability to different types of loads. It absorbs impacts and reduces the risk of injuries. The disadvantage of textile strapping is that it is mostly used, manually.
Applications:
- Packaging of fragile or abrasion-sensitive products.
- Loads requiring secure and sustainable securing.
- Industries seeking to reduce their environmental footprint.
It should be remembered that strapping can also be replaced by other packaging materials and systems, such as seals or film wrapping, but the desired fastening results will not be the same as using strapping.
4. TYPES OF AUTOMATIC STRAPPING:
We have talked about our load and the types of strapping, but which strapping system would be the ideal one taking into account the above factors? We know that there are two types of pallet strapping: horizontal and vertical. Therefore, the recommended applications for each are as follows:
- Horizontal pallet strapping: serves to compact the load in a block. It provides a very strong fastening of the load to each other, perfect for tall or unstable products. It can also be used to reinforce the stability provided by vertical strapping.
Horizontal strapping has small disadvantages, as it is a slower and more complex method than vertical strapping as it has to be performed at various heights from the load, and may not be very suitable for small or irregularly shaped products.
- Vertical pallet strapping: its purpose is to secure the load to the pallet. This type of strapping is quick and easy to apply, provides good load securing and is a versatile solution. Contrary to horizontal strapping, it is not recommended for tall products due to the large strapping arch sizes required. In the case of ultra-high loads, we would recommend the use of the automatic stretch wrapper, as it also allows for the attachment and securing of the entire load to its base.
Remember that choosing the right pallet strapping machine will allow us to optimize the packaging process, protect the products, and reduce product-related costs due to damage, deterioration, and possible errors.
5. ACCESSORIES FOR AUTOMATIC STRAPPING
Automatic strapping systems allow the inclusion of a multitude of accessories to increase strapping safety or the performance that a strapping machine can offer. So knowing what accessories are available in a particular piece of equipment is also key to choosing a strapping system over another, or a particular brand or manufacturer,
At Innova, we provide a wide range of accessories to offer a better process in the box and pallets strapping and thus achieve more efficient packaging. Some of the most common accessories are:
For Horizontal Strapping:
- Edge band applicator system
- Automatic compactor
-
For Vertical Strapping:
- Edge band applicator
- 4-sided strapping
- Strapping displacer system
6. STRAPPING HEAD, THE KEY TO EFFICIENCY
The strapping head is also a component of the strapping equipment to be considered when choosing a specific strapping machine model. There are numerous systems on the market with different mechanics and processes, but the current trend is towards simpler strapping head equipment, with more electronics than mechanics, without sensors, with Smart motors, etc.
In Innova, for example, we offer a strapping head of our technology, the ODEN head, with a patented system to achieve greater precision and control in the automatic strapping of pallets. It offers numerous advantages over the conventional head: more strength and durability, lightness, compactness, and accuracy, in addition to a significantly lower maintenance reduction.
In short, a good strapping system is essential for the optimal operation of the company and the decision between one or the other must be studied in depth, analyzing a wide range of variables, especially if you work with a large catalog of products. Strapping systems provide the necessary security and, together with optimal packaging, we ensure that our cargo will arrive in excellent condition to its final destination.
At Innova, we are experts in end-of-line packaging systems, so if you have related questions or need a quote, do not hesitate to contact us. We will get back to you as soon as possible.
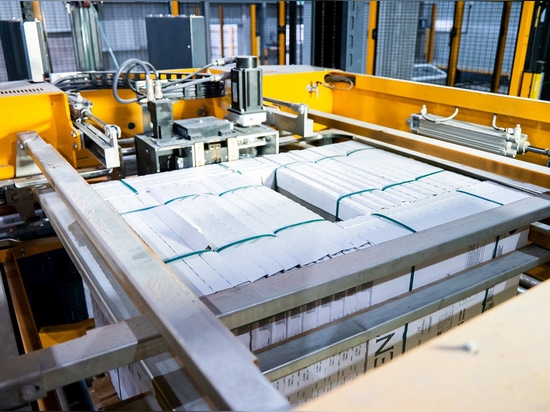
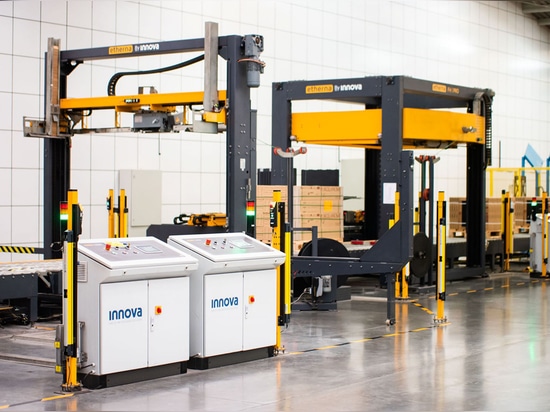