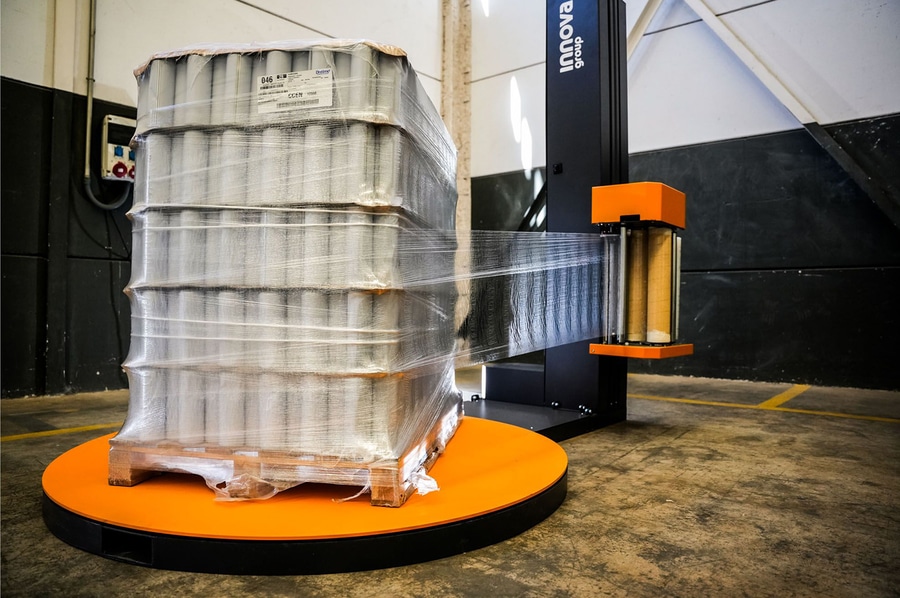
#Industry News
The Top 10 FAQs of Semi-Automatic Wrappers
Top 10 Frequently Asked Questions about Semi-Automatic Stretch Wrappers
What types of film can be used in semi-automatic wrappers? How can I program different wrapping cycles? What essential maintenance is required for a semi-automatic pallet wrapper? These are some of the common questions that customers often ask about the operation and usage of stretch wrappers. These systems are widely used by many companies because they are highly adaptable packaging systems that are efficient and easy to use.
At Innova Group, as pallet packaging solution experts, we often receive questions from customers. That’s why we’ve summarized in this article the top 10 frequently asked questions about a Semi-Automatic Stretch Wrapper.
THE TOP 10 FAQS OF SEMI-AUTOMATIC WRAPPERS:
1. What Are The Different Types Of Semi-Automatic Wrappers Available, And How Can One Choose Between Them?
2. What Are The Features Of A Turntable Semi-Automatic Wrapper?
3. What Types Of Film Are Used In A Semi-Automatic Wrapper?
4. What Accessories Can Be Added According To The Stability Objective?
5. What Accessories Are Useful To Facilitate Pallet Access To The Wrapper?
6. How Is A Semi-Automatic Wrapper Programmed And Controlled?
7. What Types, Sizes, And Formats Of Loads Are Commonly Handled By Semi-Automatic Wrappers?
8. What Technical Aspects Should I Consider When Choosing A Semi-Automatic Wrapper?
9. What Maintenance Is Required For A Platform-Type Semi-Automatic Wrapper?
10. What Safety Considerations Should Be Taken Into Account In A Semi-Automatic Packaging System?
1. WHAT ARE THE DIFFERENT TYPES OF SEMI-AUTOMATIC WRAPPERS AVAILABLE, AND HOW CAN ONE CHOOSE BETWEEN THEM?
Semi-automatic stretch wrappers can be divided into various types according to the technology or wrapping system they use:
- Rotary turntable: This type of stretch wrapper with turntable is the most widespread. The machine has a turntable where the pallet is placed and rotates while the film is applied around the product. It has a higher production capacity, is sturdy, and provides more uniform wrapping. Its advantage lies in its versatility, ease of use, and quick wrapping process.
- Rotary arm: The Rotary Arm Stretch Wrapper keeps the pallet in place while the wrapping arm rotates around the pallet to apply the film. Its main advantage is that for light or fragile loads, the arm performs the rotations, not the load.
- Robotic arm wrappers: With this type of wrapper, an industrial robot manipulates the stretch film and applies it around the pallet in a similar way to the rotary arm wrapper. These wrappers are ideal for small-scale production and/or complex loads, but they do not offer the same speed as turntable or arm stretch wrappers.
To choose the type of wrapper, factors such as packaging objectives, desired results, available space, and budget must be considered.
2. WHAT ARE THE FEATURES OF A TURNTABLE SEMI-AUTOMATIC WRAPPER?
Of the three types of wrappers, one of the most popular is the turntable type, offering different features and accessories. Some of the advantages of these stretch wrapping systems are:
- Higher load capacity: They allow wrapping larger and heavier pallets.
- More uniform wrapping: The film is applied consistently and evenly around the pallet, ensuring better load retention.
- Greater versatility: They accommodate different types of film, wrapping configurations, and adjustable tension.
- Easy operation: The operator only needs to place the pallet on the platform and start the wrapping cycle.
- Robustness and durability: Made with high-quality materials to ensure a long service life.
- Film tension control: Precise adjustment for different types of loads.
- Accessories and complements: They offer additional systems to improve wrapping and load retention, access to the wrapper, or operator safety, among others.
3. WHAT TYPES OF FILM ARE USED IN A SEMI-AUTOMATIC WRAPPER?
The most commonly used film in semi-automatic wrappers is linear low-density polyethylene (LLDPE) stretch film. This material offers high resistance, elasticity, and transparency, ensuring effective wrapping and load protection. There are different types of film in terms of thickness, width, and color to suit the specific needs of each application:
- Pre-stretched film: With thicknesses between 10 and 15 microns, this film is ideal for light and irregularly shaped loads. It is an economical and effective option to secure and contain the load during handling and short-distance transport.
- Hybrid films: These pre-stretched films with low thickness allow minimal stretch and are perfect for light or medium-weight loads.
- Stretch film: This is the most commonly used type of film in both semi-automatic and automatic pallet stretch wrappers. Depending on the type of load, films with different thicknesses and stretch capacities are required, ranging from 100% to 350% in models of stretch wrappers that support such capacities.
4. WHAT ACCESSORIES CAN BE ADDED ACCORDING TO THE STABILITY OBJECTIVE?
To optimize load stability with wrapping, various accessories can be incorporated into semi-automatic stretch wrappers:
- Reinforcement roping system: Applies a horizontal rope around the pallet before starting the wrapping, providing greater load retention.
- Film pre-stretch system: Pre-stretches the film before applying it, increasing its resistance and allowing greater material yield.
5. WHAT ACCESSORIES ARE USEFUL TO FACILITATE PALLET ACCESS TO THE WRAPPER?
Depending on the type of load and working conditions, different accessories can be used to improve pallet access to the base of the turntable stretch wrapper:
- Access ramp: For access using a manual or electric pallet truck, a ramp allows the pallet to be lifted onto the wrapping turntable via an inclined ramp.
- Low-profile platform: With a low-profile turntable, the pallet is placed directly on the turntable using a pallet jack, eliminating the need for a ramp or forklift.
- Formwork installation: An alternative to low-profile turntable is to install the turntable on the factory floor with a formwork pit, so it is in line with the ground, providing a safer and more stable entry for pallet trucks and forklifts.
- Pallet truck access: The turntable can have an access design for pallet truck forks, offering greater safety and centering of the pallet for wrapping.
- Safety stops: For forklift access, safety stops can be incorporated at the turntable to mark the pallet entry.
6. HOW IS A SEMI-AUTOMATIC WRAPPER PROGRAMED AND OPERATED?
The control system of semi-automatic pallet stretch wrappers is based on a programmable logic controller (PLC). This component enables the programming of various wrapping cycles based on specific application needs, pallet sizes, formats, wrapping finishes, and cycle characteristics. Parameters that can be configured from the PLC include:
- Number of film wraps at the base and top of the pallet.
- Wrapping start and end height, and additional height levels.
- Turntable and film carriage speed.
- Film tension and pre-stretch settings.
- Wrapping cycle recipes programming according to load formats and required wrapping types.
- Safety options and other extra functions.
- These parameters can be easily adjusted through an intuitive user interface where all the mentioned wrapping data can be added.
7. WHAT TYPES, SIZES AND FORMATS OF LOADS ARE COMMONLY HANDLED BY SEMI-AUTOMATIC WRAPPERS?
Semi-automatic pallet wrappers are extremely versatile and can handle a wide variety of loads and bundles on pallets from different sectors, including:
- Light and heavy loads.
- Stable and unstable loads.
- Different pallet sizes, from standard Euro pallets (1200 x 800 mm / 47 x 31 inches) and American (ISO, 1200 x 1000 mm / 48 x 40 mm) to medium pallets and customized sizes.
- Loads with irregular shapes are common in picking processes.
Loads without pallet bases: Some pallet stretch wrappers allow wrapping individual products according to their size or loads not transported with a pallet.
8. WHAT TECHNICAL ASPECTS SHOULD I CONSIDER WHEN CHOOSING A SEMI-AUTOMATIC WRAPPER?
In addition to the previous questions, it is important to consider some technical aspects when choosing a semi-automatic stretch wrapping system:
- Load capacity: What is the maximum load weight I need to wrap?
- Wrapping height: What is the maximum height I need to wrap my products?
- Wrapping speed: How quickly should a pallet be completely wrapped? Do I need to increase production and thus the number of wrapped pallets per hour?
- Pre-stretch system: What pre-stretch do I need to work with? How much film do I need to reduce per load?
- Reinforcement roping system: Is the reinforcement roping option essential to secure my product?
- Control options: What type of control options do I need, such as a simple control panel or a programmable PLC system?
- Integration with other systems: Do I need the wrapper to integrate with other systems, such as conveyors or production lines?
- Stretch wrapper installation: Consider aspects such as available space in the factory, need of formwork pits, technical installation requirements (electrical power, compressed air, etc.), among others.
9. WHAT MAINTENANCE IS REQUIRED FOR A PLATFORM-TYPE SEMI-AUTOMATIC WRAPPER?
Regularly maintaining a stretch wrapper is crucial to ensure its longevity and efficiency. It typically includes:
- Lubrication of moving parts.
- Inspection and replacement of worn components.
- Cleaning the equipment to prevent dust and residue buildup.
- Software updates when necessary. As it is a semi-automatic device, basic maintenance is often performed by the customer in the factory, but at Innova, we always recommend manufacturer maintenance as it will always be more thorough and meticulous.
10. WHAT SAFETY CONSIDERATIONS SHOULD BE TAKEN INTO ACCOUNT IN A SEMI-AUTOMATIC PACKAGING SYSTEM?
Safety is a priority when working with machinery, and even more so with semi-automatic equipment that requires operator handling. Some considerations that should be taken into account in the use and handling of a stretch wrapping system are:
- Specialized training for operators.
- Use of personal protective equipment (PPE).
- Safety systems: emergency stop system, control panel location outside the wrapping area, optional fencing installation, etc.
- Regular inspections and scheduled maintenance to detect potential risks and failures, as mentioned in the previous point.
In conclusion, these questions cover a wide range of topics that are important when choosing a semi-automatic stretch wrapper. At Innova Group, with over 20 years of specialization in packaging systems, we manufacture our semi-automatic wrappers using quality components that are 100% European.. Additionally, we take care of every detail of the stretch wrapper, from system configuration and its complements to installation, commissioning, technical service, spare-parts and beyond.
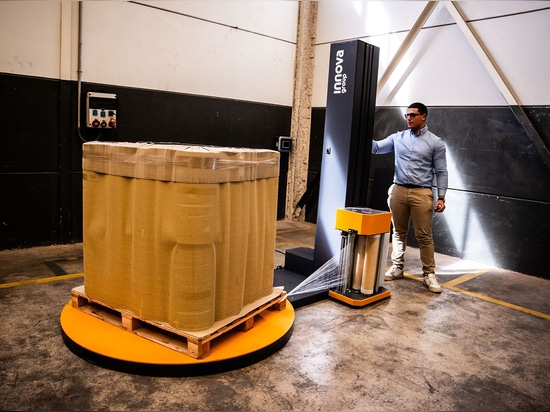
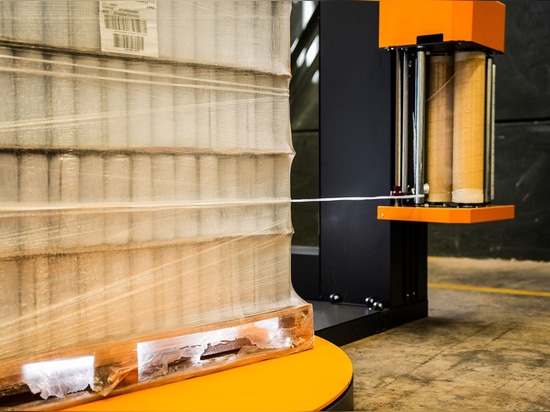