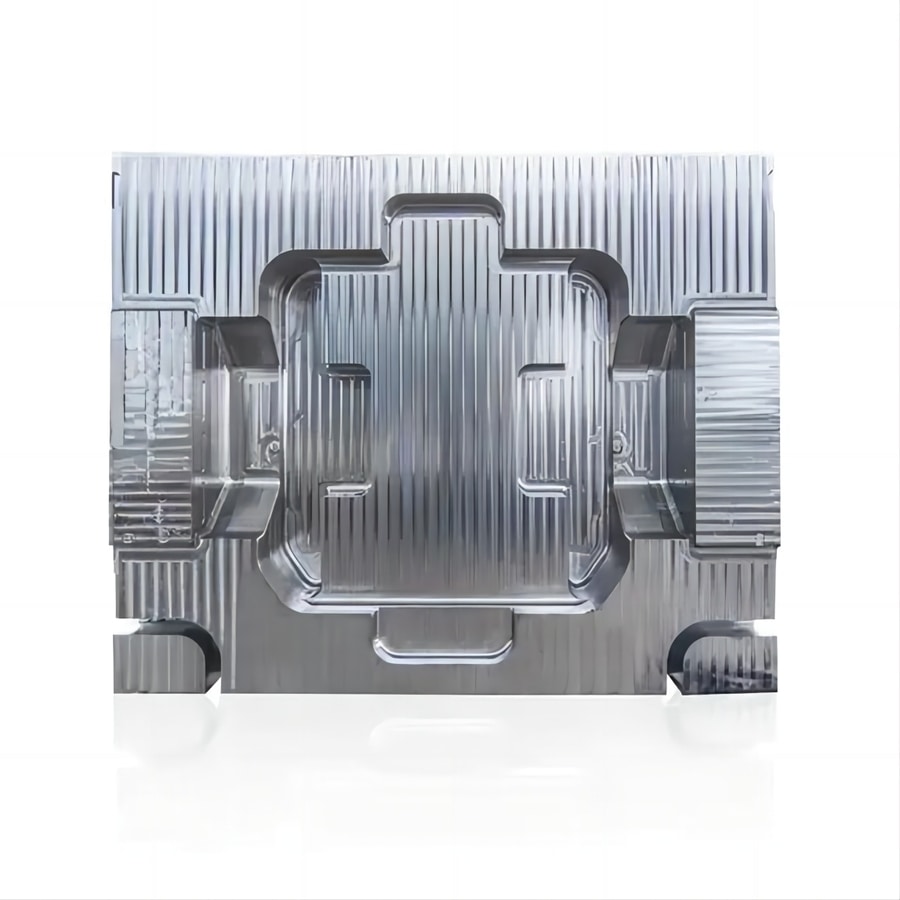
#Industry News
New Energy Vehicle
How Does Enhanced Thermal Conductivity Inside The One-Piece Die-Cast Body Structure Of New Energy Vehicle Rear Warehouse Mould Contribute To The Performance And Longevity Of Electric Vehicles?
In the unexpectedly evolving landscape of the automobile industry, the shift in the direction of sustainable mobility has caused the sizeable adoption of recent electricity motors (NEVs), with electric powered automobiles (EVs) at the leading edge. A critical thing of electrical car layout is the thermal control of key additives, specially the battery device. The one-piece die-cast body structure of the rear warehouse mold performs a pivotal position in enhancing thermal conductivity, contributing substantially to the performance and longevity of electric cars.
Thermal control is a critical attention in EVs because of the warmth generated at some point of numerous operational phases, especially throughout charging and discharging cycles of the battery. Excessive warmness can degrade the performance and lifespan of the battery, affecting the general efficiency and range of the electrical vehicle. The enhanced thermal conductivity offered via the only-piece die-solid frame structure addresses this task via several key mechanisms.
Firstly, die casting allows for using specific alloys with excellent thermal conductivity properties. Aluminum, a typically used fabric in die casting, possesses advanced thermal conductivity as compared to standard materials. The one-piece construction ensures a non-stop and homogenous structure, taking into consideration efficient warmness dissipation at some point of the rear warehouse mold.
The integration of better thermal conductivity in the one-piece die-forged body shape helps the creation of a greater powerful warmth control machine. Heat generated by the battery or different components within the rear warehouse may be correctly transferred and dissipated, preventing localized hotspots that might cause thermal strain and premature degradation of the substances.
Furthermore, the structural design and precision manageable through die casting enable the incorporation of features which includes cooling channels and fins at once into the body shape. These factors beautify the surface vicinity to be had for heat dissipation, further enhancing the thermal performance of the rear warehouse mold. The result is a greater powerful and controlled thermal environment within the EV, selling most advantageous running conditions for important components.
The blessings of more desirable thermal conductivity make bigger past instantaneous performance profits. By mitigating heat-related stresses on the battery, the one-piece die-cast frame shape contributes to extending the overall lifespan of the EV's electricity garage machine. This is specifically critical within the context of electric car possession, in which battery substitute fees and issues about degradation over time are key concerns for consumers.
Moreover, the toughness of the electric car's components translates to a extra sustainable and economically viable transportation answer. A sturdy thermal control system reduces the need for common renovation and replacements, aligning with the broader goal of making long lasting and environmentally friendly mobility answers.
In conclusion, the enhanced thermal conductivity supplied by the only-piece die-solid body structure of the rear warehouse mould in new energy automobiles, in particular electric vehicles, is a important enabler of advanced performance and extended durability. This innovation contributes to the ongoing evolution of electric mobility by addressing one of the key demanding situations in electric car layout, ensuring that these cars now not only meet however exceed the expectations of purchasers in phrases of efficiency, reliability, and sustainability.