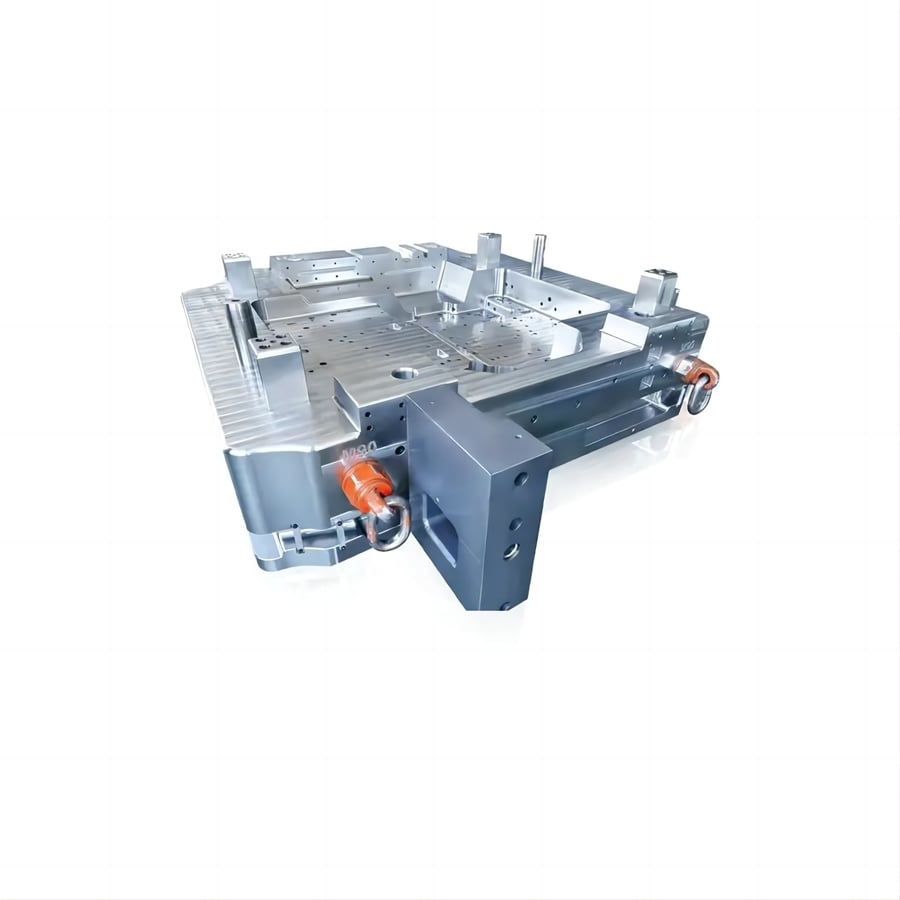
#Industry News
Alignment And Tolerance Control Are Critical Characteristics Of The Mold Frame For The Rear Warehouse Left-Right Structure In A New Energy Vehicle (NEV)
Alignment And Tolerance Control Are Critical Characteristics Of The Mold Frame For The Rear Warehouse Left-Right Structure In A New Energy Vehicle (NEV)
Alignment and tolerance control are critical characteristics of the mold frame for the rear warehouse left-right structure in a new energy vehicle (NEV). These features ensure that the mold frame is manufactured with precision and accuracy, which is essential for the proper assembly and functionality of the vehicle's rear cargo area. Here's a closer look at these characteristics:
Precision Manufacturing: Alignment and tolerance control involve precision manufacturing processes. During the fabrication of the mold frame, advanced machining techniques are used to achieve precise dimensions and shapes. Computer-aided design (CAD) and computer numerical control (CNC) machining are often employed to ensure accuracy.
Tight Tolerances: Tolerances refer to the allowable variations in dimensions and alignment. In the context of the mold frame, tight tolerances mean that the frame's components must conform to strict dimensional specifications. This ensures that all parts fit together as intended.
Exact Component Alignment: Alignment control ensures that various components, such as mounting brackets, hinges, and attachment points within the rear warehouse, are positioned accurately. Proper alignment is crucial for the seamless integration of seats, cargo storage features, and other elements.
Consistency Across Production: Consistency is key in manufacturing, especially in the automotive industry. Alignment and tolerance control measures are implemented across the production line to maintain uniformity in the mold frame's dimensions and alignment for every NEV produced.
Quality Assurance: Stringent quality control procedures are in place to verify that the mold frame meets the specified alignment and tolerance criteria. This may involve precision measurement tools, such as laser scanners and coordinate measuring machines (CMMs), to ensure compliance.
Reduction of Assembly Issues: Precise alignment and tolerance control help reduce assembly-related issues during the vehicle's manufacturing process. When components fit together correctly, assembly becomes more efficient, and the risk of rework or modifications is minimized.
Enhanced Functionality: Accurate alignment and tight tolerances directly contribute to the proper functioning of the rear warehouse. Components like rear doors, seats, and cargo management systems operate smoothly when they are correctly aligned.
Seamless Panel Fit: Alignment control extends to the fit and finish of exterior panels, such as rear doors or hatchbacks. Proper alignment ensures that these panels close securely, providing a weather-tight and aesthetically pleasing appearance.
Crash Safety: Accurate alignment is essential for maintaining the structural integrity of the NEV, especially in the event of a collision. Properly aligned components can absorb and distribute impact forces more effectively, contributing to crash safety.
Customer Satisfaction: A well-aligned and precisely manufactured mold frame enhances overall vehicle quality and customer satisfaction. Owners appreciate a vehicle that is free from alignment issues, rattles, or functional problems in the rear warehouse.
Noise and Vibration Control: Tight alignment and tolerance control can reduce noise and vibrations in the rear warehouse area, providing a quieter and more comfortable driving experience for passengers.
In summary, alignment and tolerance control are integral characteristics of the mold frame for the rear warehouse left-right structure in an NEV. They ensure that the frame and its associated components are manufactured with precision, consistency, and accuracy, ultimately contributing to the vehicle's quality, safety, and functionality.