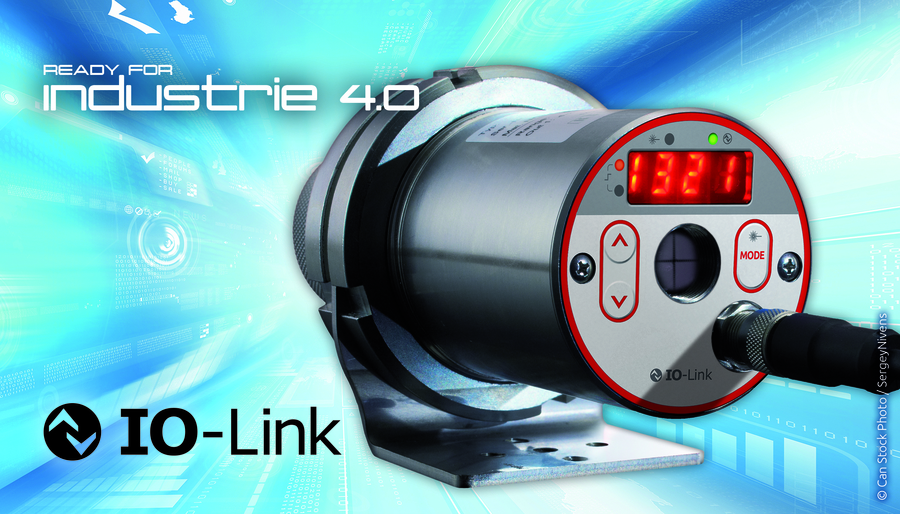
#Product Trends
New pyrometer series with modern IO-Link interface according to IEC 61131-9
In order to be able to manage the large amount of new process data of the "smart" sensors, a new interface technology with higher transmission rates had to be created.
The implementation of integrated networking and communication from the machine level to the ERP software is a high challenge for automation technology in machine and plant construction as well as for the manufacturers of sensors and actuators in this extremely rapidly developing technology, in order to be able to follow the state of the art and the innovative machine concepts. In order to be able to manage the large amount of new process data of the "smart" sensors, a new interface technology with higher transmission rates had to be created.
In this context, the world’s leading manufacturers of control and fieldbus systems joined forces 2007 years ago to create a uniform, system and company independent new standard. The result was the invention of the IO-Link interface technology. Sensors and actuators with IO-Link communication interface can be operated in all common fieldbuses such as Profibus, Profinet, Modbus, EtherCAT or CAN-bus and thereby solve one of the still largest problems of bus specific device interfaces.
When specifying the IO-Link interface in accordance with IEC 61131-9, particular emphasis was placed on standardization, operational safety and simple hardware and software commissioning and cabling of the intelligent and complex sensors and actuators. Therefore, IO-Link is rightly called the industry's USB interface for controlling machinery and equipment. It was also important that the IO devices could also be easily implemented in existing systems.
Several measured values, diagnostic information for demand-oriented maintenance, information on operating states or fault messages can be transmitted in parallel via IO-Link. Parameterization takes place flexibly during operation via the control system, depending on the production conditions.
The central parameterization of the devices from the highest level of process control contributes to operational safety. When changing a sensor, the identification is automatically checked and the configuration parameters stored in the IO-Link master are transferred to the sensor. The connection of a wrong device or a faulty configuration is therefore excluded.
To follow this technological progress, KELLER ITS - one of the leading companies in the field of optical temperature measurement - has developed the new instrument series CellaTemp® PX. The focusable precision pyrometers are the first instruments of their kind worldwide to be equipped with the revolutionary IO-Link interface technology.
Altogether, the new CellaTemp® PX series has 22 basic models with measuring ranges from 0 – 3000 °C. In combination with the 5 focusable lenses, the more than 100 device versions can be used for various measuring distances and object sizes. You can choose between a through-the-lens sighting device, a laser pilot light or an HD video camera. The variety of variants covers the complete application ranges of optical temperature measurement from the iron and steel industry, the cement, glass or ceramic industry to combustion plants.
In order to be able to use the devices in existing process control systems with analogue signal transmission, the devices of the CellaTemp® PX series have the classic 0(4) – 20 mA analogue output as well as two switching outputs in parallel.
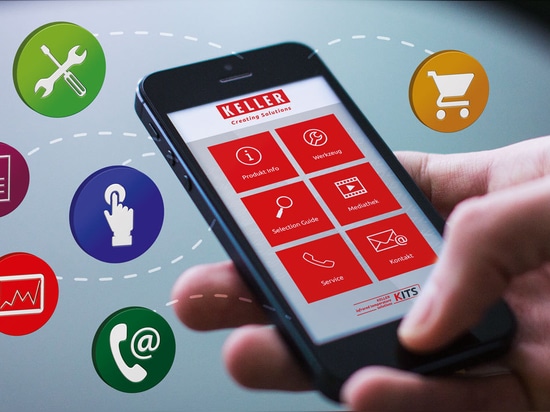