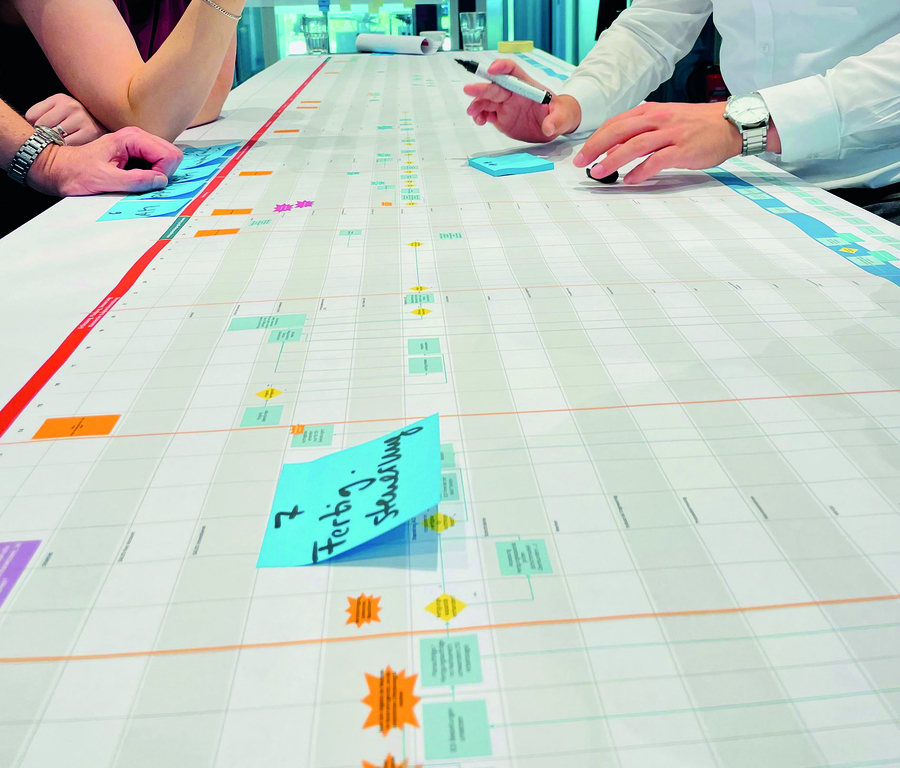
#Industry News
Quality to the Power of 2
Kendrion and INTORQ Establish Joint Quality Management System
After the acquisition of INTORQ by the Kendrion Group in 2020, the two brake manufacturers are now also merging their QM systems. The goal is to merge the know-how and experience of the two already certified companies in order to perform even better as a unit. The primary focus lies on customer satisfaction and benefits.
Starting last summer, Kendrion and INTORQ have been establishing a joint quality management system for the Industrial Brakes division. This brings together the experience and strengths of the two specialists for industrial brakes and further optimizes the internal process on behalf of the customers, who benefit from shorter delivery times and even better after-sales service.
“The merger between Kendrion and INTORQ gives our customers the best of two companies. You could say it's ‘quality to the power of two’,” explains Dr. Andreas Pusel, Head of Quality Management at Kendrion. “So it wasn’t a stretch to also optimize the internal and external processes in order to effectively take advantage of the strengths of both companies.”
When INTORQ was acquired by Kendrion at the beginning of 2020, both companies already had an integrated QM system according to ISO 14001 and an environmental management system according to ISO 14001. The Kendrion location in Villingen also has a certified energy management system according to ISO 50001. But due to the Covid-19 pandemic, the standardization of the management systems was delayed until the summer of 2022. “We wanted out employees to partake in the implementation and allow them to introduce their experience. But that wasn’t possible as all communication and discussions took place via teams,” Pusel explains.
New process map focuses on customers
Ultimately, three multi-day workshops proved to be the right format for the work process. The first two took place in Villingen and Aerzen, while at the third meeting a joint strategy was finally defined with representatives from both companies. All departments were represented with 10–12 participants, flanked by two employees from quality assurance and an external moderator. “In the first two workshops, we listed the processes at the respective locations and also examined the processes at the other locations,” Pusel describes the process. “What is good about our own system, what do we like about the other system and how do we want to merge them? In the joint workshop, a new process map was then developed and unanimously approved.”
While the divisions and their interaction were still the focus of the existing management systems and the processes were visualized accordingly, the jointly developed map now focuses on the processes with an emphasis on the needs and wishes of the customers. “Our focus wasn't on what the individual divisions are doing, but why we are doing it. Our primary focus lies on the needs of our customers,” Pusel concludes. “Our new management system focuses on their expectations and requirements and forms the basis for optimal service. By implementing this, our primary hope is to achieve a high level of customer satisfaction.”
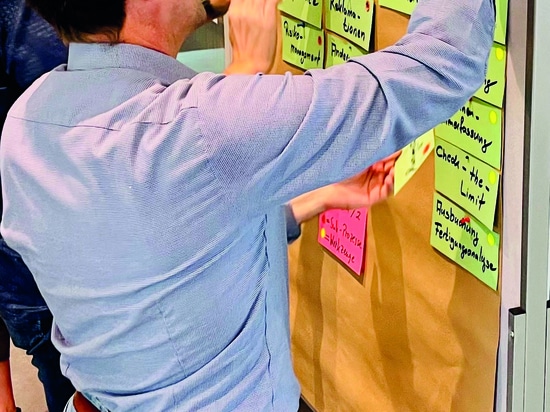