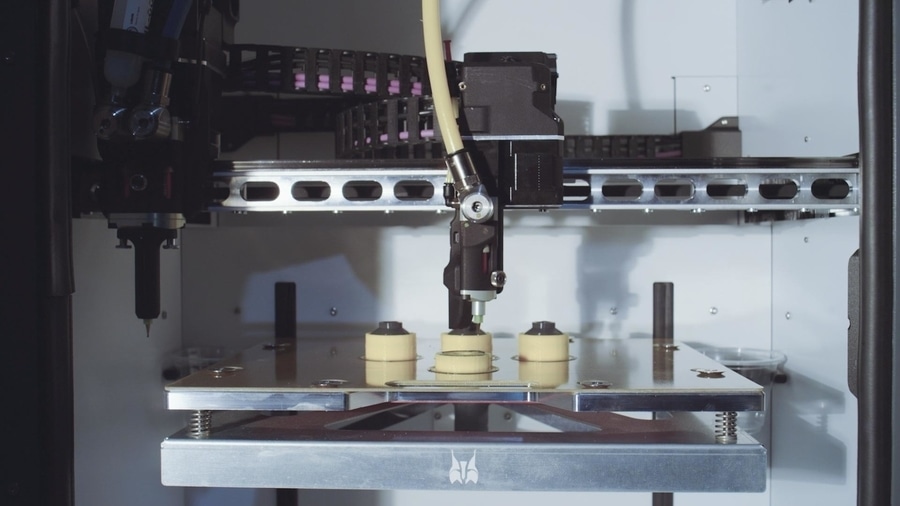
#Industry News
HOW SILICONE 3D PRINTING RESHAPES INDUSTRIAL MAINTENANCE AND PRODUCTION DYNAMICS
This article explores how 3D silicone printing, specifically the S300X 3D printer, serves as the anti-obsolescence tool for industrial equipment and produces unique and durable sealing components for demanding sectors.
In the ever-evolving landscape of industrial production and maintenance, silicone 3D printing is emerging as a transformative technology.
This innovative approach provides new solutions to overcome machinery obsolescence through the repair and replacement of complex components.
It also facilitates small-scale parts production, ensuring parts with exceptional robustness and durability.
This article explores how 3D silicone printing, specifically the S300X 3D printer, serves as the anti-obsolescence tool for industrial equipment and produces unique and durable sealing components for demanding sectors.
ACCELERATE INDUSTRIAL MAINTENANCE AND COMBAT OBSOLESCENCE
Silicone 3D printing revolutionizes the industrial approach to repairing elastomeric elements in industrial machines. The precision of the S300X silicone 3D printer, along with its ability to handle complex shapes using soluble support, enables the rapid repair of components such as bellows or joints.
Whether it’s complex machine components or specialized tools, silicone 3D printing provides a cost-effective and efficient solution to restore or enhance damaged parts to their original state.
The S300X can also produce other damping elements such as bushings or equipment protection parts, extending the lifespan of machines (see our article on silicone 3D printing applications in the Defense sector). Maintenance by silicone 3D Printing reduces downtime, lowers replacement costs, and extends the lifespan of sometimes irreplaceable equipment, addressing the challenges of industrial obsolescence.
APPLICATION EXAMPLE: SEAL IN THE RAILWAY SECTOR
A railway company faced an issue with a critical, out-of-stock component for its trains: a silicone bellows for the braking system, traditionally manufactured by injection molding.
The company could not afford the several months’ delay required for conventional manufacturing due to an unexpected incident.
In response to the urgent situation, Lynxter 3D printed the required part, saving considerable time and costs for the railway company. What would have taken weeks in the conventional supply chain was resolved in a few days, highlighting the agility and efficiency of silicone additive manufacturing in sealing emergency.
RESHAPING PRODUCTION: ELIMINATING MOLDS FOR LIMITED SERIES
Beyond repairs, silicone 3D printing opens new perspectives in small-scale production. Thanks to its flexibility, speed, and precision, it now allows design offices or maintenance centers to create custom components as needed, without requiring complex tools or molds. This agile production approach strengthens the efficiency of the supply chain, reduces excess inventory, and accelerates product development cycles.
Whether for prototyping or manufacturing small and medium series, silicone 3D printing streamlines processes and optimizes resource utilization. This approach finds relevant applications in areas such as limited-edition automobile production, the manufacture of test and measurement equipment in the aerospace sector (e.g., calibration tools), the design of components for satellites, or in research and development.
SEALING, DURABILITY: HARNESSING THE POWER OF SILICONE AND 3D PRINTING
Silicone stands out for its exceptional sealing and durability properties. Recognized for its chemical and thermal resistance, it provides excellent protection against weather conditions, UV rays, and is frequently used in outdoor applications. If your use involves exposure to outdoor elements, opting for Lynxter’s SIL-001 50 shore A silicone is a wise choice.
Silicone 3D printing takes all these characteristics to a higher level by allowing the creation of complex shapes with enhanced protection and damping capabilities.
Now, industries have the ability to design and manufacture various types of seals, caps, custom masks perfectly suited to their specific needs. This flexibility ensures tight seals, even in demanding environments (such as aerospace). Such an advancement significantly reinforces the lifespan and performance of equipment, reducing the risks of leaks, corrosion, and machine downtime.
With the S300X, silicone 3D printing emerges as a transformative technology. The inherent characteristics of silicone, amplified by 3D printing, allow the creation of complex and elaborate designs that redefine longevity and performance in various applications. Beyond maintenance, this agile technology extends to small and medium-scale production.
From aerospace to automotive, the fusion of silicone and 3D printing sets a standard for reactive and sustainable industrial advancement. The S300X embodies a form of responsiveness, adaptability, and ingenuity in the field of industrial maintenance and production.