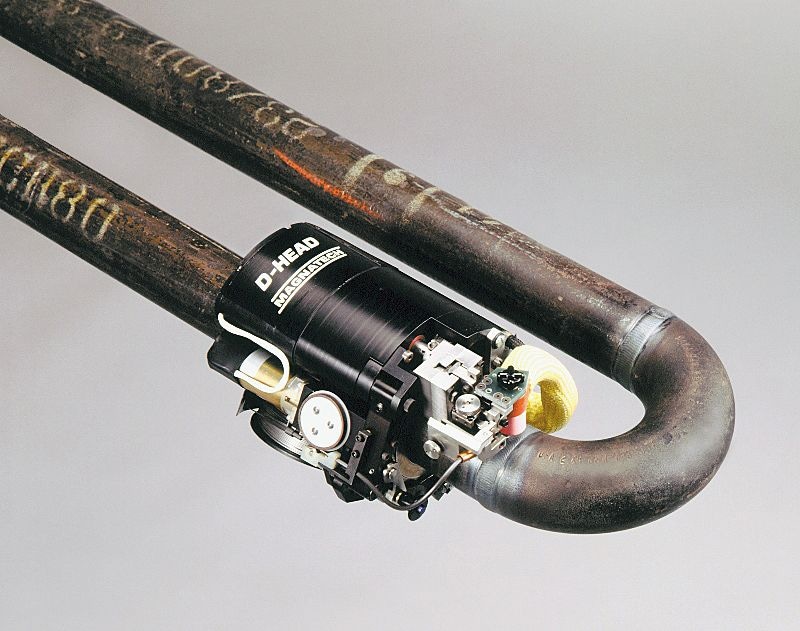
#Product Trends
NEW COMPACT PIPE WELDING SYSTEM FOR JOB SITE WORK
job site or in a fab shop.
The compact weld Head is designed for making circumferential butt welds where the pipe cannot be rotated. The
D‐Head can be used on pipe 25mm (1”) and larger. Only 50mm (2”) of radial clearance between pipes is required,
allowing use for applications difficult to weld manually because of access.
The redesigned Head incorporates all necessary functions required for multipass welding including Arc Gap Control,
filler wire feed capability, torch rotation, and torch oscillation with adjustable stroke width, speed, and
independent point “dwell”.
While many orbital weld Heads are limited to a limited size range, the D‐Head covers a broad size range from
25mm (1”) up to 356mm (14”) with the change of only one mounting component. A contractor can purchase the
equipment for a specific job, knowing that it can be used for future jobs as well.
The D Head mounts only on one side of the weld joint. Pipe‐to‐fitting welds can be made as simply as pipe‐to‐pipe
welds.
The D‐Head is capable of substantially increasing productivity by increasing the duty cycle of the welding process.
Customers have reported increased welding production by a factor of 2‐3 as compared to manual welding. The
weld Head can be used in any gravity position.
The T‐Head model is available to weld pipes 168mm (6”) and larger without limit.
The Pipemaster Model 516 incorporates all the controls to operate a multipass pipe weld Head. It is designed to be
used with commercially‐available power supplies providing up to 500 amps output to meet specific application
requirements. The two separable, man‐portable components can then be easily moved around a job site. The
handheld, waterproof Control Pendant is sealed to IP‐65, and the Controller to IP‐23. Programming is intuitive, and
100 programs can be stored in internal memory (solid state/flash = no moving parts). Software upgrades can be
sent as email attachments and downloaded to the Model 516 using the waterproof USB port. “Teach Mode” allows
rapid program development. Magnatech''s unique Auto Program capability allows the welder to enter pipe OD and
wall thicknesses. All weld parameters are automatically generated, eliminating trial and error development.