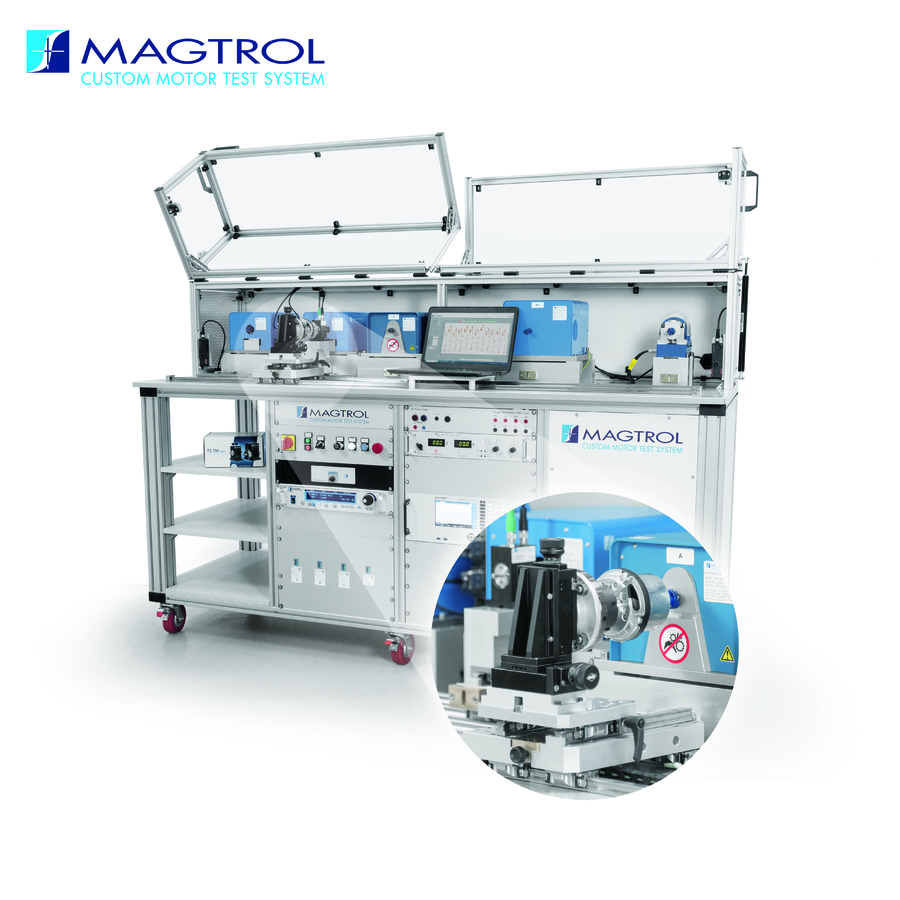
#Industry News
All-in-one multi-line test bench
Based on customer needs and specifications, magtrol built a multi-line turnkey motor test system with integrated cogging, back-emf, friction and performance tests.
Five testing lines, mounted side by side on a common table, allow for easy and fast testing of electric motor parameters. The Motor Under Test (MUT) is held in place by a concentric quick-change fastener, mounted on sliding rails to allow precise positioning in front of each testing station.
At the 1st line, a CTS 100 Cogging Test System allows the measurement of friction and cogging torque through a TS 100 Torque Sensor (50 mN·m; encoder 5 000 PPR - Pulse per Revolution; index 1 PPR). At this station, the MUT (not powered) is slowly driven (speed 1 ... 10 rpm) and the torque versus angle position is recorded, allowing precise measurements of the motor magnet’s effect around 360° of rotation with torque detection better than 1 mN·m of resolution. Linear or Polar as well as FFT graphs can be displayed or printed.
In order to keep the angular position, the MUT remains connected to the TS Series Torque Sensor and both move along the sliding rails to the 2nd station for Back-EMF testing. At this step, the tested sample is driven ≤10 000 rpm, while current and tension of Back-EMF (Back Electromagnetic Forces) are recorded. Testing software correlates Cogging versus Back-EMF system at the same angle position.
The platform that supports the motor under test is then disconnected from the torque sensor and can move to the next testing stations which have their own torque and speed measuring capabilities.
The 3 remaining test lines are equipped with different dynamometers for load performance testing of the Motor Under Test. The dynamometers execute loading profiles while torque, speed, current, tension and temperature (amongst other parameters) are recorded, allowing the calculation of Input / Output Power and issue Efficiency Curves of the motor. This specific Customized Motor Test System (CMTS) is composed of an HD 106 Hysteresis Dynamometer (18 mN·m; 7 W; ≤ 30 000 rpm), a WB 23 Eddy-Current Dynamometer (80 mN·m; 500 W; ≤ 100 000 rpm) and a 4 WB 2.7 Eddy-Current Dynamometer (0.6 N·m; 1 kW; ≤ 50 000 rpm). This customized combination allows a wide range of the customer’s devices to be tested. Each test line can be activated by a switch selector on the system’s front panel as well as configurated through the software.
The test bench integrates a high-end 4 channel Zimmer LMG 641 power analyzer, with precision current sensors. In the 3 last testing stations, the device under test is powered by a DC power supply integrated in the bench and controlled by the software. The DSP 7001 controller provides a closed loop regulation either in torque or speed mode along the testing profile.
Easy to use, Magtrol M-Test Software controls the system and enables the user to quickly set test parameters and sequences in torque or speed control, curve mode, closed loop or open loop. Test setups can be saved and recalled any time. It allows the acquisition of complete testing data (torque, speed, current, efficiency, power input, power output, temperature, resistance), temperature rise and related data during motor operation. M-TEST Software has the flexibility to test a variety of motors in a multitude of configurations. The data generated from this user-friendly program can be stored, displayed and printed in tabular, graphical formats or universal data reports and is easily imported into a spreadsheet. Clear and professional reports can be issued.
The Customized Motor Test System includes protection covers with safety switches preventing the system to run while the doors are open. A continuity testing as been conducted for assuring the appropriate grounding of each device, in compliance with the highest European Health & Safety regulation.
This realization shows large Magtrol’s competencies and flexibilities to supply high-end state of the art Motor Test Benches according to specific customer needs.
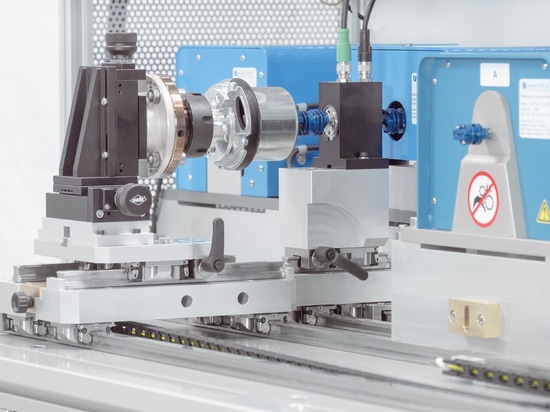
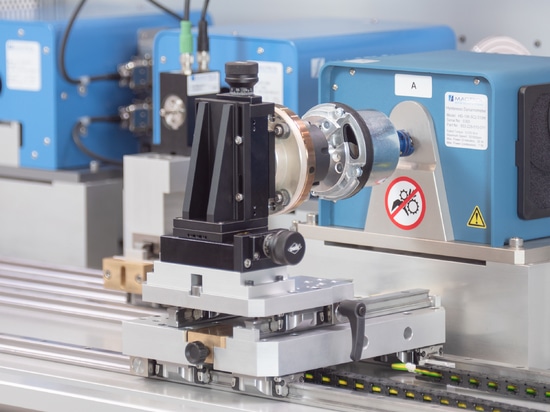
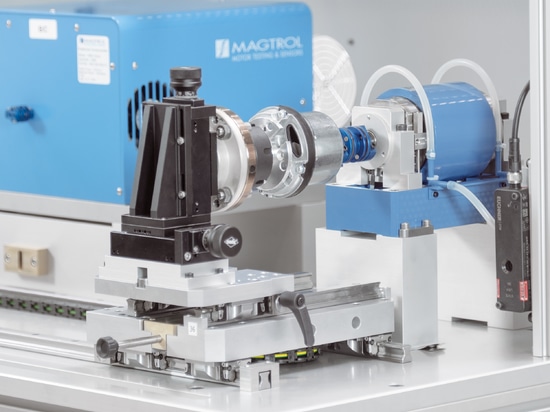