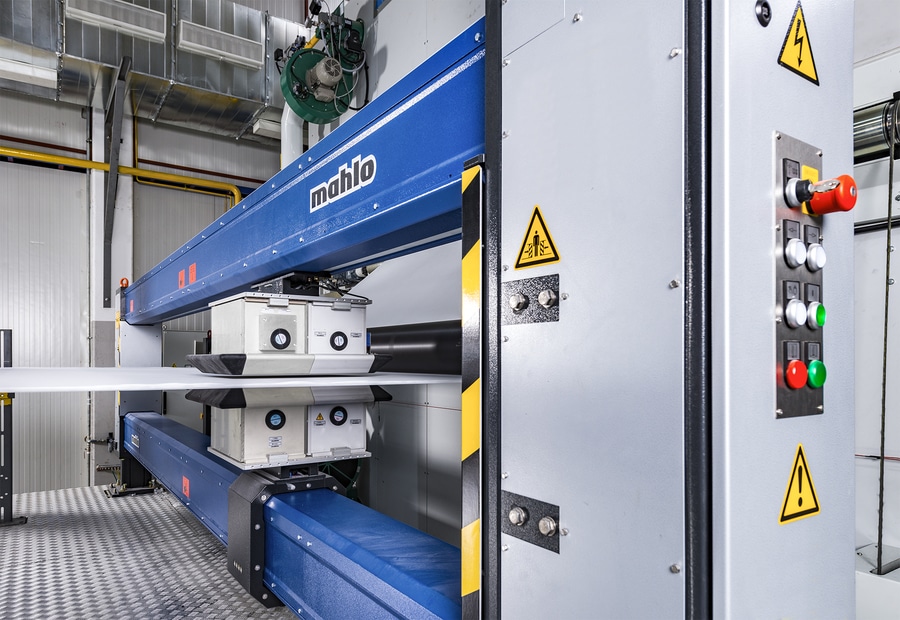
#Product Trends
Revolutionizing quality control of optical coatings with high-precision sensors
Mahlo GmbH introduces state-of-the-art white light interferometry for precise thin film thickness measurement in the electronics industry
Watching your favorite show on the TV, reading a message on your smartphone, checking email on your laptop, guiding to the destination in your car - we all have numerous activities where we use an LCD screen. This technology has transformed the electronics industry. LCD screens have become indispensable in our daily lives. But they also have a weakness: LCD screens have a problem with good visibility when used in a lot of ambient light. The solution is to increase the brightness and contrast of the screen far above normal levels compared to indoor use. This prevents direct reflections on the screen surface. This is done with optical films that are applied to the front.
Tapping into the growing market for optical films in China.
The films can change the transmission properties of light, including light projection, reflection, absorption and scattering. Optical coatings are used to improve the transmission, reflection or polarization properties of an optical component. An anti-reflective coating can reduce the reflection on any surface to less than 0.1%. This ensures the best image quality when working on a laptop or watching TV, even in direct sunlight.
Optical films are usually coated with several thin layers of materials such as oxides, metals or rare earth metals. Depending on the complexity of the products, several different coating applications are sometimes necessary so that they can exploit their full function. However, this is only possible if all layers have the exact required coating quantity. Even slight deviations from the specified tolerance values during production lead to malfunction and thus to considerable losses due to rejects.
Precision is what counts: The challenge of coating thickness control
Coaters therefore in many cases resort to measuring the basis weight on the running web. But especially with very thin coatings, online measurement poses a major challenge, as it must be extremely accurate.
In order to achieve a reliable result and thus a product that satisfies both manufacturer and customer, a sensor is needed that is capable of measuring the coating thickness directly on the running web with a high degree of precision. Mahlo GmbH + Co. KG, a German machine manufacturer with decades of experience, uses a measuring method that meets precisely these requirements. The special sensor technology is part of the Qualiscan QMS quality measurement system, which measures and controls important parameters by traversing sensors while the web is running.
Innovative sensor technology: white-light interferometry for unsurpassed measurement accuracy.
The Optoscope WLI sensor referred to uses the white light interference method. If clear or slightly opaque thin coatings are irradiated with white light, the light is partially reflected at both the upper and lower interfaces and interference colors are produced that are as colorful as a rainbow, as known from soap bubbles, for example. The frequencies of this interference are a measure of the layer thickness and are determined using an FFT algorithm. For the result to be unambiguously determined, the layer to be measured must have a different refractive index than the substrate layer. Under these conditions, a very high accuracy of up to 0.01 µm (10 nm) can be achieved.
In addition, the WLI also manages to indirectly determine extremely thin coatings in the nm range - down to 0.2 µm - for aqueous or solvent-based coatings on film, depending on the solids content. In the interference method, the values come directly from the material, due to the interaction of the reflections. The situation is different when measuring with beta or X-rays, which can be used before or after the coater. Here the values do not come directly from the material but are calculated from how the respective radiation interacts with the mass. In other words, how much back radiation or penetration hits the measuring sensor. The direct measurement is one of the reasons for the high measurement accuracy of very thin layers.
An advantage for manufacturers is also the possibility of one-sided measurement, which saves space during installation and is more cost-effective than a conventional O-frame. In addition, the white-light interference method does not require any special radiation protection requirements. This facilitates handling during operation.