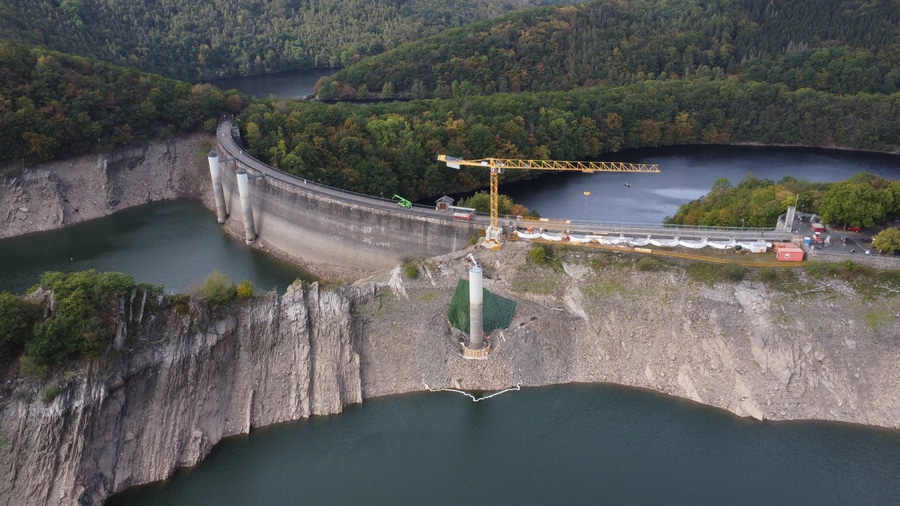
#Industry News
New coating for water tower in the Eifel
Circular formwork from PASCHAL makes bottom outlet tower of Urft dam earthquake-proof
Paschal's Circular Trapezoidal girder formwork (TTR) has been deployed on unusual terrain. The bottom outlet tower of the Urft dam in the Eifel region was renovated last autumn to provide it with better protection against earthquakes. As part of this, it was given a concrete coating. The formwork was doubly secured to increase the concreting speed: the TTR was fitted with a ring belt to absorb the pressure forces of the fresh concrete, and the formwork was also secured to the existing tower wall using anchors. By combining these two methods, it was possible to form the tower in seven phases, each 2.90 metres high.
The Urft dam, including its three bottom outlet towers, was built over 120 years ago. This dam, the oldest one in the northern Eifel, was also the largest in Europe at the beginning of the 20th century. On 19 October 1906, one year after it was officially commissioned, Kaiser Wilhelm himself visited the dam, according to the press spokesman of the Eifel-Rur Water Board, Marcus Seiler. In autumn 2020, two of the three towers were made earthquake-proof from inside thanks to a steel-reinforced concrete shell. The renovation of the third tower, built into the rock next to the dam wall, was started in autumn 2023, as the necessary preparations were much more complex. The renovation work had to be carried out from the outside because the gate valve used to drain the water is located inside the tower. "This was not an easy task, as the water in the dam had to be drained to the level at which the tower protrudes from the water," explains Marcus Seiler.
The Eifel is located on volcanic rock and is therefore an earthquake zone, even if the people living there are generally unaffected. "An extremely strong earthquake could cause a tower to sway, which could cause damage," says the press officer. The Eifel-Rur Water Board commissioned the construction company Bauunternehmung Bruno Klein from Jünkerath in Rhineland-Palatinate to make the bottom outlet tower earthquake-proof. This proved to be a logistical challenge for the construction company due to the steep slope with significant differences in elevation, which meant they had to position the crane on a plateau directly next to the dam wall to be near the almost 20-metre-high valve tower. Paschal's Circular Trapezoidal girder formwork (TTR) was chosen to form the new concrete coating.
Although the Bauunternehmung Bruno Klein construction company has often used climbing formwork for bridge construction and civil engineering, this project was far from an everyday occurrence for the family business. "Using the crane to move the platform elements and the fall protection was a particular challenge in this rough terrain. Nor do we often have to deal with a circular formwork with a radius this tight on a tower," confirmed Theo Mies, the site manager at Klein and the person responsible for this project. The experts from Paschal who helped and supported the Klein employees during the first few steps were therefore of great assistance. Foreman Martin Ketterer, who has worked at Paschal for 28 years, and his colleague Markus Schmitt travelled from the Black Forest region of Germany to be present on site for two days. Ketterer: "We provided the Klein team with assembly instructions and helped them to erect the platform brackets and boards, set up the formwork and suspend the climbing platform, which serves as a working and safety scaffold. This was not at all easy with the tight radius, as the rails run outwards in a trapezoidal shape on the circular formwork."
The diameter of the formwork required was just 3.80 metres. The nine panel elements of the TTR, totalling 34 m² of formwork, were made to measure to match the outer radius at the Paschal factory in Steinach and delivered on site. Site manager Theo Mies confirms that his employees benefited from the specialist advice. "The quotation and specifications themselves were very detailed and well prepared. My employees were so well instructed on site that they were able to handle and move the formwork for the remaining phases without any problems. Georg Hager, who provided us with technical support throughout the entire project, was available to us at all times and ensured that the supply of parts ran smoothly and that there were no delays. Even my foreman Hans-Gerd Schneider, who was a little sceptical at first, only had good things to say and was very satisfied with the on site support."
The fact that the external formwork had to be installed without any clamping points proved to be a particular challenge when forming the bottom outlet tower. The custom formwork department designed a solution to counteract the fresh concrete pressure forces that arise during concreting and at the same time ensure that there was no loss of concreting speed. "Our formwork planners came up with a ring structure for this," reports Hans-Peter Steiner. The head of Paschal's training department explains further: "Individual steel straps were screwed together to form a ring or steel belt. The closed formwork ring then absorbs the tensile stresses. The principle is similar to a wooden barrel, which gets its stability from the steel rings attached to the outside."
The ring structure thus absorbs the tensile forces when the viscous concrete is poured. But that alone is not enough. Foreman Martin Ketterer explains: "The faster the height increase when pouring concrete, the greater the pressure of the fresh concrete. The ring belt alone would not have enabled the formwork to withstand the pressure and it would only have been possible to carry out the upwards concreting slowly. We worked with six anchors and we also inserted additional tie rods into the existing structure. So you're actually practically forming in a double-sided manner, because a counter-pressure is being generated."
With this double securing system – the anchoring plus the ring belt – it was possible to absorb the fresh concrete pressure and increase the concreting speed. This was much to the satisfaction of Theo Mies. "Without the anchors, we could only have concreted a maximum height of one metre per phase; this method meant that the full height of 2.90 m could be concreted directly in one go," says the site manager. The faster concreting process also meant that the concrete was of better quality and there were no visible lumps on the concrete surface.
The ring structure thus absorbs the tensile forces when the viscous concrete is poured. But that alone is not enough. Foreman Martin Ketterer explains: "The faster the height increase when pouring concrete, the greater the pressure of the fresh concrete. The ring belt alone would not have enabled the formwork to withstand the pressure and it would only have been possible to carry out the upwards concreting slowly. We worked with six anchors and we also inserted additional tie rods into the existing structure. So you're actually practically forming in a double-sided manner, because a counter-pressure is being generated."
With this double securing system – the anchoring plus the ring belt – it was possible to absorb the fresh concrete pressure and increase the concreting speed. This was much to the satisfaction of Theo Mies. "Without the anchors, we could only have concreted a maximum height of one metre per phase; this method meant that the full height of 2.90 m could be concreted directly in one go," says the site manager. The faster concreting process also meant that the concrete was of better quality and there were no visible lumps on the concrete surface.
Even though Paschal's formwork was used to move upwards seven times, strictly speaking, it was not a climbing formwork. Due to the confined space, the formwork was placed on the ground between phases, while the platforms were moved upwards separately. "In principle, we were climbing. It was impossible to avoid placing the formwork on the ground. We couldn't move it to the rear to place the reinforcing bars due to the lack of space," emphasises Martin Ketterer. "The formwork was cleaned and a biodegradable parting compound was applied in between formwork phases – this was easier to do in the construction site set-up area," adds Theo Mies.
On 20 November 2023, the time had finally come. The concrete coating for the valve tower was now complete. Thanks to the TTR circular formwork, the third tower of the Urft dam is now stable and will be able to withstand earthquakes in the future. The dam in the northern Eifel is now fully capable of protecting the people in the region from floods and droughts for at least another hundred years.
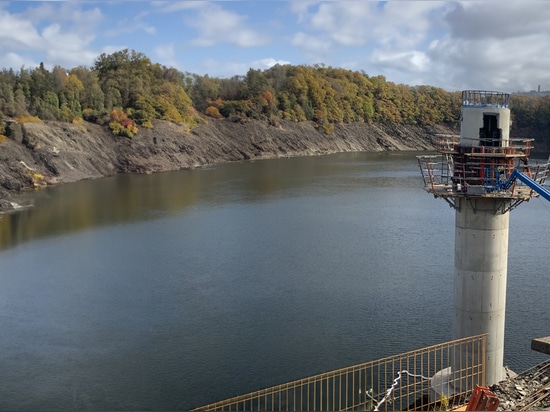
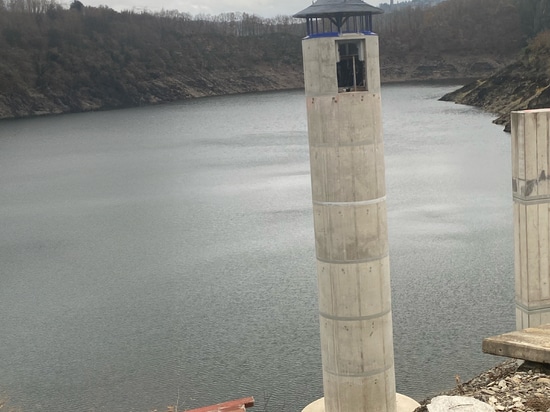