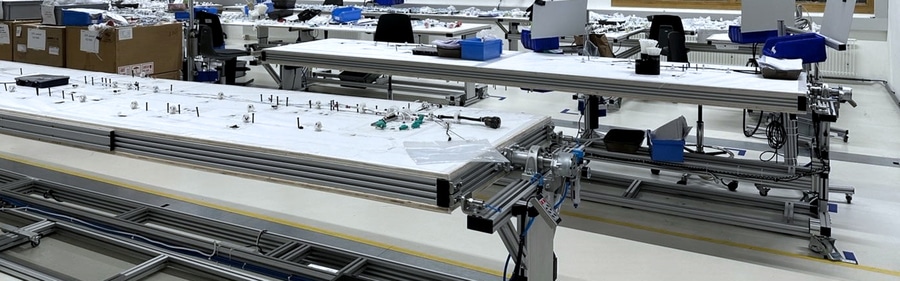
#Industry News
Short changeover times with modular assembly tables
Short changeover times with modular and ergonomic assembly tables made of aluminum profiles
Initial situation:
The internationally active Swiss company Pilatus Aircraft Ltd is known for its globally unique aircraft such as training and smaller multi-purpose aircraft. Various wiring harnesses are required for the different aircraft, which differ greatly in terms of design, such as length and shape. Depending on the design of the wiring harness, simple tables were lined up in the required shape and fitted with the appropriate boards. Although this method worked in principle, it made it difficult to work comfortably and safely. On the one hand, you bump into the table legs when working and on the other hand, a comfortable, ergonomic posture is not possible. In addition, positioning the tables is awkward and time-consuming.
Challenge:
Pilatus' aim was to obtain a workstation system that would increase ergonomics and safety for employees, while at the same time being modular and flexibly adaptable and expandable at any time. The changeover time for the tables and boards for installing the various wiring harnesses was also to be shortened and simplified. No more than two employees should be required to convert the large work surfaces.
Solution:
Phoenix Mecano worked closely with KKS Ultraschall AG to develop a customised design proposal. This co-operation was based on a long-standing partnership and a deep understanding of the specific conditions at KKS Ultraschall AG. With the help of the STEP files provided, the customer was able to gain a detailed insight and make the necessary adjustments before the final production of the machine enclosure, which made the development process particularly efficient. The excellent communication and mutual understanding made the collaboration much easier. Even minor changes were implemented quickly and efficiently, which supported the entire development process. Phoenix Mecano also took into account special requirements such as conformity to standards and the use of closed profiles. After completion, Phoenix Mecano organised the transport of the machine enclosure to KKS Ultraschall AG, with modular delivery due to the size of the machine enclosure. This modularity facilitated assembly on site and ensured seamless integration with the etching and cleaning system. In addition, Phoenix Mecano provided KKS Ultraschall AG with storage space in order to solve any space problems flexibly and efficiently.
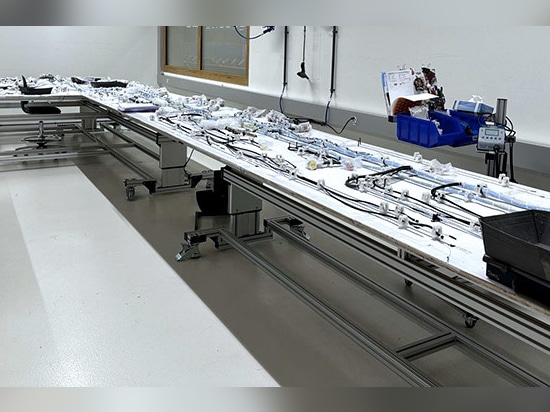