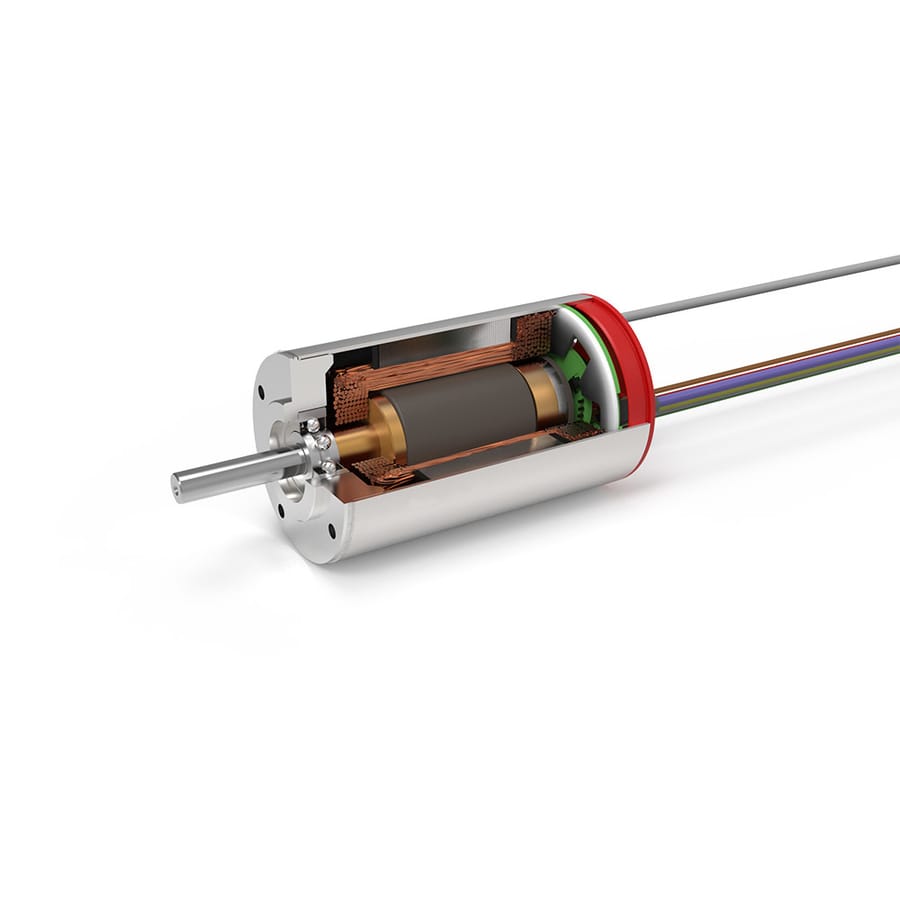
#Industry News
Thermal Considerations for Ironless Brush DC and Brushless DC Motors
Converting electrical power into mechanical power always comes with losses during the process
These power losses are mainly turned into thermal power and tend to be higher in magnitude when the delivered mechanical power is greater. The thermal energy generated inside an electric motor creates a temperature rise that will result in a heat transfer from warmer to colder (thanks to conduction and convection), and eventually carries the heat outside of the motor.
One of the biggest challenges for electric motor manufacturers is to ensure that the instant internal temperature of the motor never exceeds its various components’ maximum, admissible temperature. Depending on the design of the motor and the materials used, the thermal phenomena will dictate the motor’s performance.
Designers typically consider two areas of improvement to increase the performance of a motor without overheating and damaging its components:
Minimize the losses: improve the power conversion’s efficiency by generating less heat for a given mechanical power output (enabling a greater mechanical power for the same heat creation).
Improve the motor’s ability to lead the generated thermal energy to its surrounding environment (heat dissipation) so that the internal temperature rise lessens, allowing greater thermal energy generation for the same internal temperature rise.
To help you understand this phenomenon, we will use an analogy of water filling a bathtub that is simultaneously leaking. See Figure 1.
The water flow coming out of the faucet corresponds to the thermal energy generation inside the motor. As soon as water gathers in the bathtub, the pressure at the bottom will result in a leakage that will send the water out of the bathtub, corresponding to heat dissipation. The higher the water level, the higher the pressure at the bottom of the bathtub, and therefore the greater the flow of water leakage.
Similarly, the heat dissipation of a motor is proportional to the delta between the inside temperature of the motor and the outside (ambient) temperature. But as the water flow depends on the outlet hole diameter, the heat dissipation also depends on the thermal resistance, which defines “how difficult” it is to carry heat out of the motor. The lower the thermal resistance, the easier and faster the heat will be led outside the motor, meaning a greater dissipation power.
A bathtub has a finite capacity and will overflow if the water level exceeds a certain point. Similarly, the components of a motor have a given thermal capacity and having the instant temperature exceed a certain level can damage the components within seconds. The motor’s rated performance must match the requirement of keeping its temperature within the admissible operating temperature range.
Usually, the most critical component is the coil, as this is the very place where the joule heating occurs. In the case of excessive temperature, the insulation coating around the copper wire would end up melting, resulting in permanent damage to the motor.
STEADY-STATE OPERATION
Brush DC Motor
A coreless brush DC motor is typically designed as a self-supporting coil rotating in the airgap between a permanent magnet and the housing, which are both part of the stator.
The joule heating power (W) produced in the rotating coil is directly linked to its electrical resistance R (Ω) and to the current flowing through it, I (A). There are no iron losses as the rotor is ironless. See Figure 2.
As the coil temperature rises, the heat will transfer from the coil to the tube (1), and then from the tube to the ambient environment (2), as shown on figure 2. These two successive steps have different thermal resistances (Rth1 and Rth2, respectively), since individual materials have disparate thermal conductivities, and the shape, mass and surface area of each part also has an influence on how heat will be transferred.
Read the whole paper on portescap.com