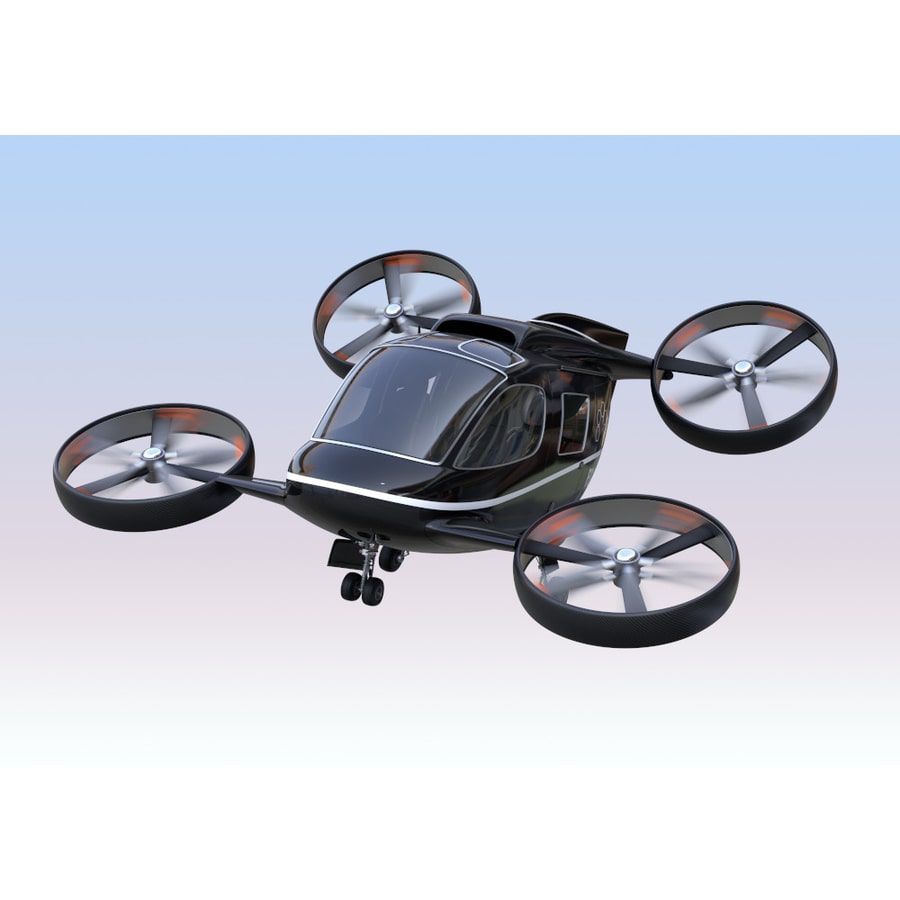
#White Papers
Advancing A&D Systems with Micro Motors
Advancing Aerospace And Defense Systems With Precision Miniature Motors
ADVANCING AEROSPACE AND DEFENSE SYSTEMS WITH PRECISION MINIATURE MOTORS
Aerospace and Defense applications are demanding, requiring extremely precise and power-dense motion control solutions; accordingly, these are some of the most challenging applications for motion control engineers to design and implement. Typical A&D specifications necessitate motors that can withstand extreme temperature ranges, operate under severe shock and vibration conditions, and fit in constrained space – all while maintaining high performance levels. This article will review these stringent requirements and address the design challenges of the precision miniature motor manufacturer.
MINIATURE MOTOR TECHNOLOGIES COMMONLY USED IN AEROSPACE AND DEFENSE APPLICATIONS
Three motor technologies are frequently used for motion requirements in A&D applications: Brush DC Coreless, Brushless DC (BLDC), and Stepper. DC Coreless and BLDC motors are usually selected for their higher efficiencies and lower weight, with BLDC motors being available in both cylindrical and flat forms and utilizing slotted and slotless winding technologies. Stepper motors are also an ideal selection for applications where precision is required but price-to-performance is the primary driver.
All three technologies are adaptable to not only the challenging performance requirements of typical A&D applications, but also to their extreme environmental conditions. Temperature requirements are a key example, as they can range from -55°C/-67°F to 200°C/392°F; this means that all motion control components must be specially designed to survive in these extremes and to sustain high-performance levels throughout the entire operational range. Advancements in materials, particularly metals used in motor housings, special bearing lubricants, specialty coatings for electronics, and plastics for insulation of the coils allow mini motors to operate reliably in these conditions.
Operating within high shock and vibration environments is a second common challenge that must be considered. Special design considerations are necessary to allow miniature motors to perform in these extreme environments, as even small movements of the motor coils can lead to motor damage. Motor design must ensure that the critical internal components of the motor (rotor, shaft, bearings) and the connected components (gearboxes, encoders) are adequately secured to prevent movement when exposed to the most severe shock and vibration conditions.
Exposure to the potentially hazardous materials often encountered in these applications is a third potential motor failure mode that must be addressed. Motor design engineers seek to incorporate advanced materials coupled with specialized sealing designs within the motor. The optimum design ensures that the motor can operate at peak efficiencies in these extreme environments and, more importantly, that the motor operates safely and reliably.
AEROSPACE AND DEFENSE APPLICATIONS REQUIRING MINIATURE MOTORS
A&D applications can be separated into three categories: commercial aerospace, military aerospace and defense, and spacecraft and rockets. The common element among these is the need for powerdense, lightweight motor designs that provide a form of actuation. From seat actuation to flight control systems, fin actuation, or valve control, precision miniature motors are an essential component of these applications.
Valves and Actuators
Various types of valves and actuators are used on aircraft vehicles to perform critical functions, including regulating the flow of fuel to the engine and controlling the airflow into the aircraft cabin. Due to their physical location in the aircraft, these devices are typically exposed to extreme environments and demand maximum power density and dynamic response from the motion system. Typical design considerations include:
• Modifications to the magnet material to ensure that magnet strength does not degrade as temperatures elevate
• Lamination material selection ensures that the motors can withstand extreme temperature ranges
• Properly selecting lead wires that connect the motors to the system electronics ensures they remain pliable in extreme cold and do not melt in extreme heat.
Each of these motor design modifications must be considered to ensure high-performance operation throughout the wide temperature extremes over the life cycle of the aircraft. Many of the legacy and current generation valve designs either use stepper motors that finely regulate position or brush DC motors that are an ideal fit for on/off valves. However, next-generation designs are gradually transitioning to using brushless DC motors for smart actuation applications. This is due to the BLDC motor’s precise positioning capabilities that can provide data on the number of operations, monitor any abnormal behavior, and supply maintenance information, thereby improving the overall reliability and performance of the equipment.
Window Shade and Seat Actuation
Electromechanical control for window shades and seat actuation is expanding innovations for private and commercial aircraft, being aimed at providing ease of use for passengers and increased control for the airline personnel. These systems allow the passenger to conveniently raise or lower the shade or seating surface at the touch of a button; they also allow flight attendants to control the cabin ambient light and assume proper seat position during takeoff and landing. Due to their high-power density, low noise, and low temperature rise, DC Coreless motors are primarily used in this application. The ability to operate motors without any control electronics is a clear cost advantage, while the high efficiency and low weight of the motor reduces power and fuel consumption - a key objective for every airline today.
Smart Defense
Smart munition applications involve one-time use where precision control in a high-speed/extreme vibration environment is imperative. Motor control and dynamics are key contributors to overall system performance, where every potential parameter that can even marginally affect performance during operation must be addressed in the motor design.
Dependent on design priorities, BLDC slotted, slotless, and flat designs are all appropriate motion solutions for fin control actuation systems. With high-power density and small package size, these motors reduce the weight of the actuation system and provide a high dynamic input response from the navigation system to ensure excellent flight control. With wing deployment applications, both brush DC and brushless DC technologies are an ideal fit. EO/IR applications typically utilize small brush DC and BLDC slotless motors with high-power density to minimize the overall system package size. Brush DC motors also help to reduce the overall footprint since only simple control electronics are needed for motor operation.
Overall, for simple motion systems, brush DC motors are the most cost-effective solutions to meet application requirements like performance, size, and extended life. For more complex requirements, a fully customized BLDC motor is likely the best solution.
CONCLUSION
One of the most difficult tasks facing motion solutions suppliers within the Aerospace and Defense space is tailoring the miniature motor system to the unique demands of each application. To do so, motor design engineers need to have expertise in fine-tuning design elements to align with application requirements, as well as be adept in adapting existing designs to optimize for SWaP (space, weight, and power) and varying environmental conditions. COTS (Commercial-Off-The-Shelf) motors prove to be the ideal fit for Aerospace and Defense applications in this context, as they present a blend of substantial power output within a compact, lightweight frame. Manufacturers equipped with an array of motor technologies possess an excellent capability to analyze specific requirements spanning diverse technologies. This often translates into offering customers a range of motion control solutions that precisely match their needs.