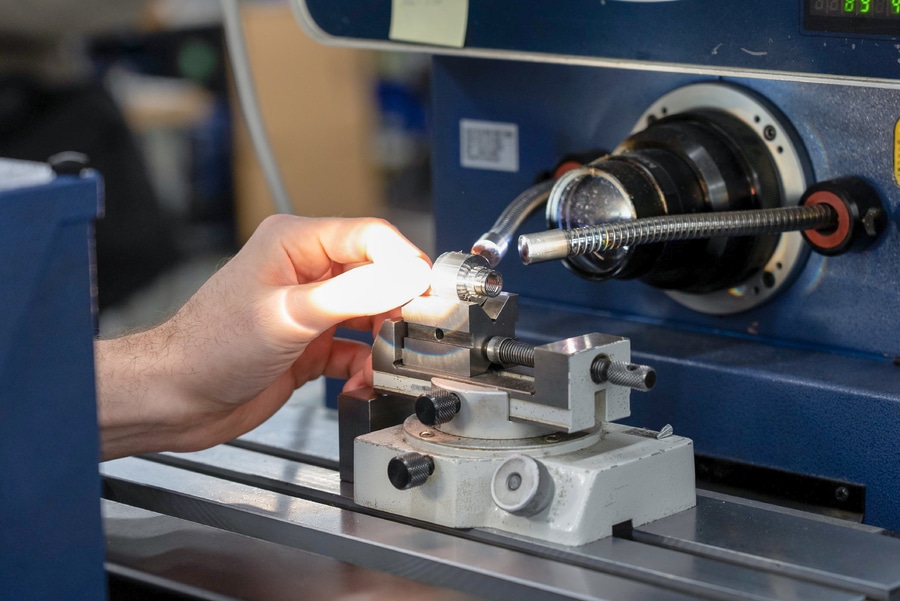
#Industry News
Joining Methods for Mini Motors
Joining Methods to Add Coupling Elements to Miniature Motors
Joining Methods to Add Coupling Elements to Miniature Motors
Miniature motors play an essential role in many applications such as handheld surgical tools and miniature mechanisms in small machines. To transmit power from the motor to the load requires frequent use of small pinions, couplings and other components that must be joined to the motor output shaft. This blog covers the most common joining methods used by customers in their miniature motor/gearbox solutions.
Joining devices to shafts with diameters from 0.8mm to 8mm can be challenging due to their small diameter and minimal gripping surface. When elements are joined to the output shaft, caution must be taken to avoid damage to the motor bearings and windings that affect motor system performance. The key parameter consideration is the amount of torque the joint will experience in the application. Best practice is to design the joint based on the desired safety factor above the stall torque rating of the motor.
Joining Methods, Advantages and Limitations
Permanent Joints
This type of joint is typically used in a final assembly where the joined device is not intended to be removed. Permanent joining methods include the press fit, laser weld, resistance weld, adhesive bonding, and threaded connection.
Press fit is a common method where the joined part is designed so that the inner bore size tolerance is slightly smaller than the diameter of the motor output shaft, which creates an interference fit. The advantages of the press fit design are that it is simple to manufacture and that the analytical joint strength calculations for round shafts are readily available. Press fit force should not exceed the manufacturer recommendation for the part being joined. The standard manufacturing process during the pressing operation is to support the motor shaft to avoid damage to the motor bearings or other device components. Since circumferential stresses will be generated on the shaft and the mating coupler, it is necessary to confirm the strength of both the joined device and the motor shaft.
Two types of welded joints are commonly used in miniature motion solutions (laser and resistance). Laser welding may be employed to create joints between the joining part and the motor shaft. The laser provides a concentrated heat source to rapidly melt and fuse the materials into a strong and precise joint. Typically, this method is required to optimize the welding parameters so that the desired joint quality and performance can be achieved. The lack of access to a laser welding machine and material incompatibility of the joining parts for laser welding can be constraining factors of this method.
Resistance welding creates a weld joint between the joining part and the motor shaft with an electric current passed through the joining materials. This current generates heat at the interface to create the weld. The limitations of this method are the potential lack of access to the resistance welding setup and material incompatibility of the joining parts for resistance welding.
Adhesive bonding uses a suitable adhesive to bond the joining part to the motor shaft with a strong and durable connection. Surface preparation, such as cleaning and roughening the mating surfaces, is important to ensure optimal adhesion. The adhesive selected should be compatible with the materials involved, the gap size of the joint, and the specific application requirements. It's also important to select adhesives based on factors such as temperature resistance, chemical compatibility, and mechanical strength. Adhesive bonding is the most common method to bond the metal shaft to a polymer component. A positive driving feature on the motor shaft and the polymer drive element is recommended for reliable power transmission over the desired device life.
A threaded connection may be used if the joining part has an internal threaded hole that matches the external thread on the motor shaft, which allows the part to be threaded onto the shaft. The standard shaft design on a miniature motor is normally a cylindrical diameter or is cylindrical with a flat or keyway, therefore, the need for a threaded shaft will require customization.
Non-Permanent Joints
These joints are used for either a temporary assembly or in applications where it may be necessary to separate the joined parts for maintenance or other purposes. Non-permanent joining methods include key/keyway, split/flexible couplings, and set screws.
The key and keyway method involves machining a keyway in both the motor shaft and the joining part. A key, typically a rectangular metal piece, is inserted in the keyway providing positive torque transmission between the motor shaft and the joining part. This method is limited to shaft diameters greater than ~4 mm due to the strength considerations of the components and the availability of a standard key size. Axial locking is accomplished by other means in the design.
In the split/flexible coupling method, the coupling bore encircles the motor shaft at one end and the driven shaft of the joining component at the other end. The coupling features a clamping mechanism, often in the form of screws, which when tightened clamps the coupling securely around both shafts to establish the joint between the driving and driven shafts. This coupling is usually flexible to account for small misalignments of the shaft axes.
Set screws are small screws that tighten against the flat surface of the motor shaft, which creates a localized clamping force to secure the joining part in place. Set screws typically have a threaded hole on the joining part into which the screw is tightened. Set screws are generally employed for light loads and are typically used in a pair.
The choice of joining method depends on the specific design requirements, the desired level of joint strength and reliability, the ease of assembly and disassembly, and the compatibility of the miniature motor with the joining component. Users should consider the unique needs of the application to determine the most suitable joining method. A combination of joining methods may be employed to achieve specific joint strengths in the application. Examples would include press fitting on a knurled shaft or combination of a press fit and adhesive bonding to provide additional joint strength.
As a miniature motion solution provider, Portescap offers guidance on joint designs specific to the application requirements or can provide a complete solution with the joining component fixed onto the motor shaft. Please contact our experts to discuss your specific application requirements.