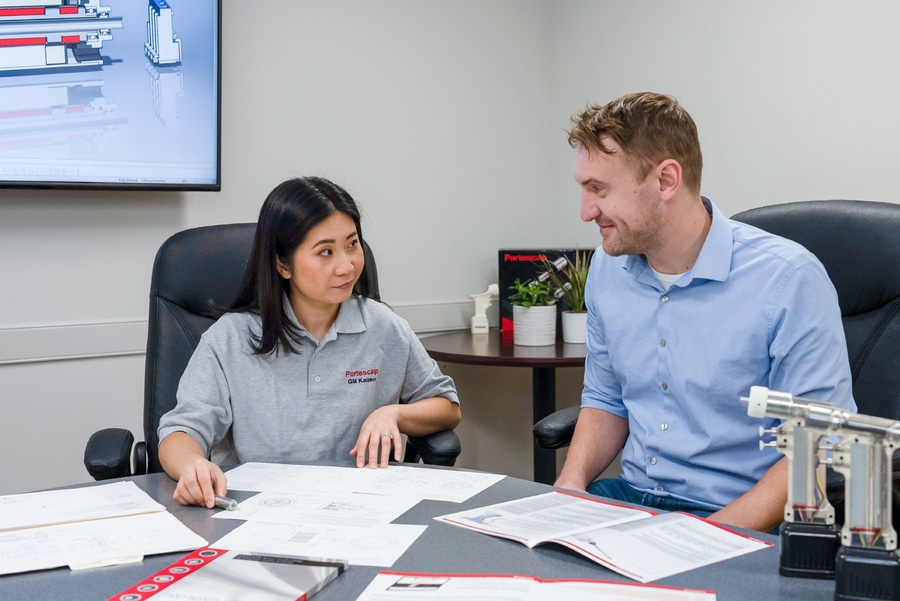
#White Papers
Why You Should Consult Motion System Experts Early
Starting Early: Why You Should Consult Your Motion System Engineers At the Onset of New OEM Projects
Starting Early: Why You Should Consult Your Motion System Engineers At the Onset of New OEM Projects
Electric motors — along with their power transmission, feedback and control devices — are critical to machines that rely on motion axes. Original equipment manufacturers (OEM) embarking on a new product’s development should therefore involve the motion specialists as early as possible in the project’s design. Since the motor and its output have a broad impact on the equipment’s overall design, early inclusion of the motion system experts will optimize the performance of the equipment and also streamline project development. This is especially the case for precision equipment that requires a miniature motor and motion system.
MINIATURE MOTORS ENABLE MORE PRECISE CONTROL
By controlling the torque, speed, acceleration and shaft position, the electric motor is the fundamental component that brings to life a variety of systems — from surgical robots to industrial machines. Some of these applications don’t require more than 1 kilowatt (kW) of power, necessitating small, lightweight motion systems.
Compact motion systems — which typically generate less than 1 kW and measure roughly 90 millimeters (mm) or less in diameter — must often meet complex application requirements. The motors and control systems that guide satellites or power the joints of a surgical robot, for example, need to provide pinpoint precision. Similarly, the motors that control medical equipment, such as patient infusion systems, must ensure absolute reliability. Such reliability is also a typical requirement for mission-critical military applications.
No matter the equipment, a motion system’s design requires careful consideration. These aspects will impact the equipment’s ability to fulfill its tasks according to the application’s speed and accuracy requirements. They will also affect the equipment’s ultimate size and weight, as well as its time to market and development costs, making it highly beneficial for OEMs to include the motion system experts at the earliest possible stage of a new project.
INCLUDE THE MOTION SYSTEM EXPERTS AT THE IDEATION PHASE
When OEM engineers turn their attention to concept development — and preferably, when they’re still in a product’s ideation phase — they should consider the motion system. Even if the discussions only include general assumptions of the motion system’s design, consulting the motion system engineers at this point will ensure later design choices aren’t constrained. Every OEM project has design objectives that are, more or less, set in stone. These attributes often relate to precision, speed and reliability — all of which significantly depend on the motion system. Early involvement of the motion system engineers will ultimately ensure these final objectives can be met in the most effective way.
Of course, if OEMs go it alone, their early decisions regarding the motion system will be based on standard products, limiting the equipment’s overall design. Although they can change the motion solution specifications at a later stage, this additional rework will delay time to market and drive extra costs.
ESTABLISH THE MOTION SYSTEM’S SPECIFICATIONS AT THE CONCEPT PHASE
At the concept stage, OEM engineers formalize their overall design and typically include an off-the-shelf motion solution for proof-of-concept purposes. Often, OEM engineers working alone will use an oversized motion system to widen the safety margin for torque and speed. While this approach can help the engineers zone-in on required operational performance, it also means they must scale down their final choice of motion system to meet the optimal parameters for mass, dimensions and energy efficiency.
One way to identify more accurate performance requirements earlier is to measure the current in the device across its range of load and speed working points, including all potential cycles and peak duty needs. With assistance from the motion system engineers, this approach will enable OEMs to more accurately determine the necessary motor size and required gear reduction to achieve the optimal speed-torque and inertia balance. During this stage, the OEM should also specify the feedback device, including its position in the design and motor drive controller.
Confirming these design aspects at the concept phase will also inform OEMs whether an off-the-shelf design can fulfill their objectives or whether customization is necessary. The outcome of this decision will have a high impact on the project’s overall time and cost.
CONFIRM THE MOTION SYSTEM’S DESIGN PRIOR TO THE FEASIBILITY PHASE
The feasibility stage is often the longest period in a project’s design. However, at this point the motion system’s form factor and performance requirements shouldn’t change in any significant way so long as the OEM has already made the appropriate decisions during earlier phases. Instead, motion system engineers should use the feasibility stage to fine-tune their motion solution to optimize the system’s performance and efficiency.
If the motion system design hasn’t been confirmed at an earlier stage, the decisions taken now — which may involve the size or type of motor, power transmission, feedback and control devices — could require significant equipment and integration rework. This outcome will inevitably add unnecessary time and cost to the project’s development.
Involving motion system specialists at the earliest stage will streamline the overall development process, improving time to market and reducing engineering costs. Most importantly, engaging with a motion designer at the outset is the most effective approach to optimize equipment performance and meet design objectives.
CONTACT AN ENGINEER