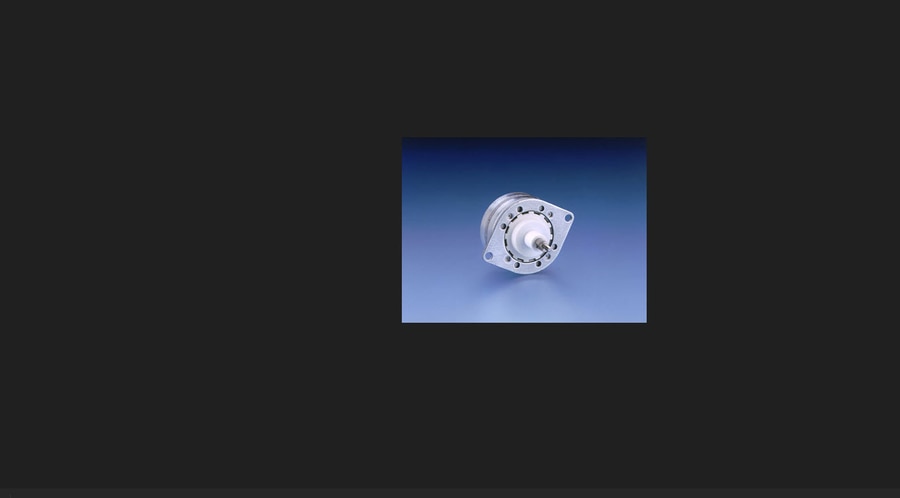
#Industry News
Speed Impact on Stepper Motor Torque Performance
The Effect of Speed on Stepper Motor Torque Performance
Stepper motors are generally selected for applications where precise positioning, holding torque, and dynamic torque at low speeds are required. They have also been used to deliver relatively high torque at high speeds, though this is certainly uncommon due to how the stepper motor operates. Motor performance is measured in terms of speed and dynamic torque generated at given driving conditions (input voltage/current). The torque generated in stepper motors is proportional to the current supplied to the coils, up to the saturation limit; in other words, the higher the current in the coil, the higher the torque. However, the winding’s inductance (L) and resistance (R) limits the current in the coil, thus limiting the generation of torque.
Understanding the Electrical Time Constant
Stepper motors have two phase windings that are mounted on separate stators. An electrical circuit for one phase of the motor can be represented by a simple circuit as shown in Figure 1. (Click on the link to see the figure on our website).
In stepper motors, the current is supplied in steps/pulses. Ideally, the current step pulse is a square wave, i.e. zero rise and fall time. However, as shown in Figure 2, the current shows an exponential time-dependent response due to the coil inductance and resistance. By looking at the current equation and Figure 2, it’s clear that the current takes some time to reach its max value in the coil.
The time constant (τ) of the LR circuit is given as L/R. The electrical time constant is defined as the amount of time required for the current in the winding to reach 63% of its rated value. For example, if the rated current of the stepper motor is 2 A per phase, and after one time constant if the current in the winding is 1.264A, then the corresponding motor output torque will also be proportionally less than the rated torque at the rated current.
Why Do Stepper Motors Deliver Less Torque at Higher Speeds?
To achieve the rated torque output from the motor, the current in the coil must reach its rated value. When the motor is operating at lower speeds, there is ample time available for the current to reach its rated value in the coil. This means at lower speeds, a stepper motor can provide the rated torque. At higher speeds, however, the time constant plays a crucial role. When a stepper motor is running at higher speeds, the number of pulses supplied to the motor in a given time frame is very high, which means there is a lesser amount of time available for the current to reach its rated value. The rated value of the current can’t be reached in one phase winding before the current is supplied to the next phase, and as the current is not able to reach its rated value, a stepper motor cannot generate the rated torque and performance decreases at high speeds.
We can understand this phenomenon by looking at Portescap’s 42M048D1B motor.
The time constant for the selected motor is 0.807 ms; i.e. the current will reach 63% of its rated value in 0.807 ms. The time required for the current to reach its rated value is equivalent to 5τ. In this example, this time will be 4 ms, which corresponds to 250 PPS. If the current in the windings reaches its rated value, then we can get rated torque from the motor.
We can overcome this limitation and can still use the stepper motor to obtain the required torque at high speeds by using one of two methods:
Using a Chopper Driver. A chopper driver uses the technique of turning output voltage to the motor on and off rapidly (chopping) to control the current in motor windings. The chopper driver applies very high voltage to the stepper motor at every step, which causes a rapid increase in current. As the chopper driver maintains a constant current in the motor windings even at high speed, we can achieve the required torque from stepper motors at high speeds.
Keeping a Lower Electrical Time Constant. If the application needs high torque from stepper motors at high speeds, then the winding needs to be customized to keep the L/R as low as possible. Design engineers at Portescap can customize the motor design for these applications in order to achieve the required torque at the desired speed.
Want more information on using stepper motors in a high speed, high torque application? Reach out to Portescap here – we’ll be happy to help!