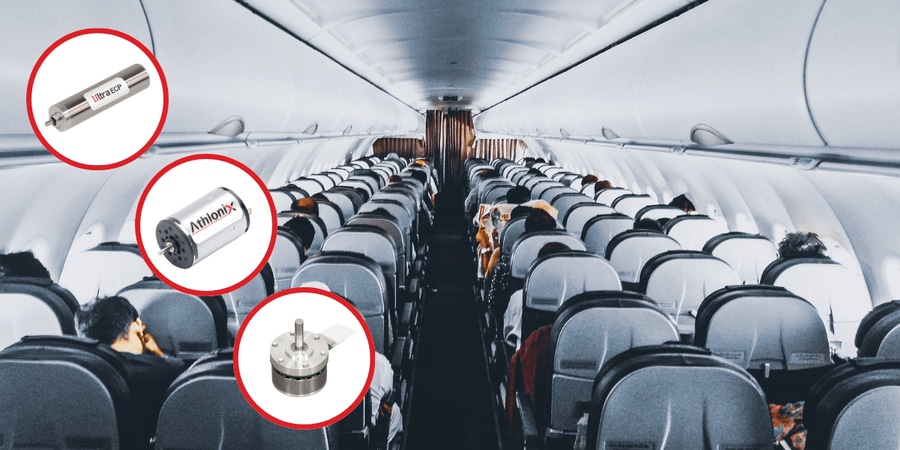
#Product Trends
Aerospace Motor Technology Options
Decoding Micro Motor Selection for Aerospace Applications
In the Aerospace industry, reliability and durability are non-negotiable. The need to meet Size, Weight, and Power (SWaP) targets further adds to the challenge, as these applications demand efficient and compact solutions that excel in harsh environments. DC motor technologies, including brush DC coreless, BLDC cylindrical (slotted and slotless), and BLDC slotted flat motors, emerge as optimal choices to meet these demands, offering a range of diverse form factors tailored to specific application needs.
Brush DC coreless motors consist of a rotor, made in a coil arrangement fixed to a shaft, and a stator with fixed magnets. Since the coil arrangement is not constructed from iron laminations, the motor is considered ironless. Ironless designs have significant advantages since typical iron core losses are eliminated. The motors are commutated using precious metal or graphite brushes that lower the contact resistance and friction, as well as simplify the control electronics.
BLDC cylindrical motors utilize a stationary coil with a rotating permanent magnet. The coil windings, which are part of the stator, can be energized and electrically commutated; this eliminates the need for a commutator and brush system.
Within BLDC technology, there are two unique motor topologies: slotted and slotless. The primary difference between the two designs is in the stator winding. In slotted motors, the coil wire is inserted into lamination slots, which can be further ruggedized by overmolding the assembled stator. Slotless motors use a self-bonded coil design which can be easier to manufacture.
Brushless DC slotted flat motors, meanwhile, have a unique setup with coils inserted into lamination slots within an outer rotor configuration. This provides a tailored solution for A&D applications, ensuring efficiency and reliability without unnecessary complexity.
Motor Selection Criteria for Aerospace Applications
DC motor technologies offer a range of solutions perfectly suited for the demanding requirements of the Aerospace industry, with each option bringing its own set of advantages to the table. However, tradeoffs do exist among these motor technologies, depending on the specific criteria required by the application. Key motion system parameters to consider when selecting a motor for your application include:
Torque Density. DC motors offer high torque in compact designs, with up to 3-5 times the maximum continuous torque transiently. BLDC slotless and slotted motors provide up to 10 times the maximum continuous torque without magnetic saturation. Flat BLDC outer rotor motors offer high torque density with a lower form factor.
Friction Losses. Brushed DC motors minimize friction with low-friction brush and commutator materials. Precision DC motors designed for A&D minimize losses through careful consideration of motor bearings.
Iron Losses. Iron-core DC motors suffer eddy current losses at higher speeds, while ironless motors, favored for higher-speed applications, eliminate iron losses. BLDC motors with iron cores can minimize iron losses through strategic design and material selection.
Maximum Speed. Small DC motors and flat BLDC designs can operate continuously at 10,000 RPM or higher, while cylindrical BLDC designs can exceed 40,000 RPM. High-speed motors feature bearing systems balanced for minimal vibration.
Cogging Torque. Coreless DC motors and BLDC slotless motors eliminate cogging torque, while slotted BLDC motors can minimize it through design adjustments.
Motor Life. Brushed DC motor life is limited by brush and commutator wear, whereas BLDC motors, commutated electronically, are limited by bearing life.
Inertia. BLDC slotted motors are preferred for low rotor inertia applications, while BLDC slotted flat designs have higher inertia due to larger rotors.
Robustness. BLDC slotted motors are most robust, suited for harsh environments due to their stator and rotor designs. BLDC flat motors, though less robust, can be designed to meet A&D requirements.
Conclusion
The Aerospace industry demands a comprehensive array of motor technologies capable of meeting diverse application requirements with unwavering reliability and efficiency. From compact designs to high torque densities, DC motor solutions offer a spectrum of performance tailored to specific needs, all while navigating the challenges of SWaP constraints. BLDC slotless and DC coreless motors stand out not only for their efficiency and compactness, but also for their ability to withstand the rigorous standards of DO-160G and MIL-STD-810, making them invaluable assets in environments where resilience is paramount.
Are you navigating the complexities of selecting the perfect motor for your application? Reach out to Portescap engineers here, who will provide