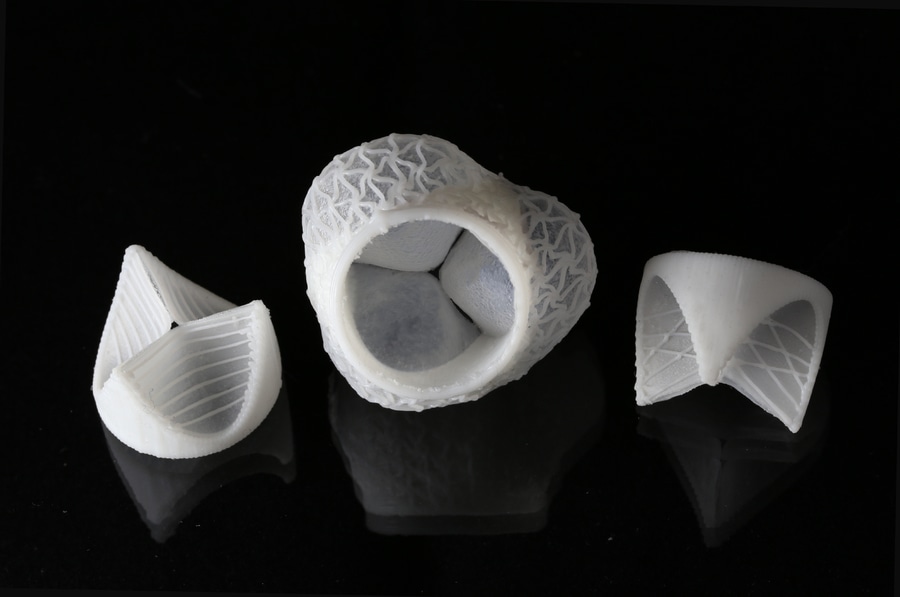
#Industry News
Bioinspired Artificial Heart Valves Made by Silicone Additive Manufacturing
preeflow® eco-PEN300 “prints” synthetic implant
In an additive manufacturing process, virtual heart valve models are created with the aid of a CT scan and a preeflow eco-PEN300 one-component dispenser: Fergal Coulter from the "Complex Materials Group" of ETH Zurich undertook research for medical technology - more precisely for the additive manufacturing of artificial heart valves. They were manufactured using custom medical-grade polysiloxanes, together with chemicals which resulted in stiff, medium, or soft silicones following UV-triggered polymerization. These materials conform to biocompatibility standards for cytotoxicity, as well as irritation and skin sensitization. (Source: https://www.cell.com/matter/fulltext/S2590-2385(19)30038-4 )
One process for customized results
A customized 3D printed mandrel is produced, derived from a patient’s C/T scan. As one of several production steps, a part of the artificial heart valve is applied by using the eco-PEN dispenser. The dispenser is also used to print silicone reinforcing fibers onto the leaflets and then strengthen the edges. The non-leaflet areas of the valve (the “intraaortic triangles”) are constructed according to the scan of the patient's aortic root. Then the silicone is cross-linked with UV light. In the second step, a silicone mold of the aortic root is created. An alginate is used to temporarily encapsulate the valve. The cap protects the valve leaflets and allows an over-hanging artificial vasculature and integrated stent to be applied. For this purpose, the assembly is scanned with a 1-dimensional laser. The surface is virtually recreated by computer. And the tool paths for an auxetic stent geometry are calculated. Afterwards, the eco-PEN300 is used again for printing: The printed struts are about 0.3 mm thick. Now the valve mandrel can be removed. The alginate cap is removed by oven dehydration. Depending on whether a coating was sprayed on as an intermediate step or not, the final result is a patient-specific artificial heart valve with a covered or windowed aortic stent.
The design of the completed heart valves is inspired by human biology (3-leaflet valves). Depending on the requirements, an individual geometry is implemented to obtain a tailor-made synthetic product. Through digital fabrication, an artificial valve is created as a functional implant. In contrast to the existing mechanical heart valves and tissue valves, this method is seen as promising for future applications.
The reasons for promising future applications:
▪ Completely individual heart valves are possible (based on a CT scan of the patient's own heart valve).
▪ The products are inexpensive to manufacture.
▪ Due to the materials used, immunosuppressors (blood thinners) may not be necessary in the future.
▪ Not only the design and geometry of the printed heart valve is similar to its biological counterpart, but also its functionality, which has been tested in detail on physiological blood pressure in Coulter’s experiments.
▪ The printed fiber-reinforced heart valve has lower mechanical stress and outstanding hemodynamics (= science of the movement of blood in the vascular system).
eco-PEN prints heart valve and stent
The task of the eco-PEN dispenser is to ensure the stability of the heart valve and atrioventricular valves. So that the system does not collapse when used under physiological conditions. As described above, the eco-PEN300 prints a part of the heart valve as well as a stent (= medical implant to keep vessels or hollow organs open) or a stent like structure for stability. The eco-PEN therefore also constructs the framework for the heart valve.
For implementation in this sensitive area, perfectly consistent precision in the area of micro dispensing is important: Repeatability must be guaranteed in dispensing such small quantities. Here the lightweight preeflow dispensers were able to convince. As the needle must always point perpendicularly to the precisely manufactured mandrel, the preeflow dispensing technology is complemented by an agile robot system.
Fergal Coulter about working with the preeflow dispenser: “The eco-PEN is an excellent extruder when printing with multiple different materials that have different viscosities and rheological properties. The precise volumetric dispensing of the pen removes variation in flow of the extrudate during long prints and reduces time spent in tailoring pressure profiles to achieve a constant material flow.”
An overview of the advantages of the high precision preeflow dispensers:
▪ Simple and flexibly adaptable to individual geometries
▪ Easy integration (the eco-PEN300 is used with a spacing of 300 µm and perpendicular to the curvature of the surface to be covered)
▪ Smallest dispensing quantities with absolute repeatability of > 99 %
The process can be clearly seen in this video: https://youtu.be/dvGsNAQ_yVA?t=40
To meet the requirements of the 3D printing market, ViscoTec has established its own Business Development Additive Manufacturing in 2016. The portfolio has been expanded: In the meantime, various 3D print heads have been developed, which can print both one- and two-component fluids and pastes and are even better suited for additive manufacturing.
Vision for the future
A vision of Fergal Coulter for future research: It could be possible to print stem cells (incorporate stem cells) and therefore integrate them into the valve - to match morphology.
This is still a dream of the future, but there are already initial ideas for using cell-laden hydrogels in 3D printing. One such project was also implemented with the help of a preeflow eco-PEN: Living cells were dispensed without damaging them. For "living" ventilation slits in sportswear. More information can be found here: https://www.preeflow.com/en/3d-printing-of-fluids/