
#Product Trends
Practical Solutions case study
Inspection of a Laser Weld Seam
Initial Situation:
The production of a client in automotive industry is subjected to extremely stringent quality requirements. This is valid particularly also for the precision of laser weld beams of fine mechanical work. 100% inline supervision is required for the following task: A laser weld beam (width ca. 200µm) has to be verified with respect to the presence of pores and geometrical anomalies. Camera inspection performed until now turned out to be not stable. Therefore the client is forced to implement an improved monitoring process.
Challenge:
Resolution required amounts to 4µm. The high gloss finished material may give rise to reflections, and the space for installation is restricted. A low form factor for the monitoring equipment is imperative.
QuellTech Solution:
The sensor QuellTech Q4-5 features a sufficient resolution and an extremely compact design (86x32x85 mm, lxwxh). Two laser scanners at distinct offset positions have been integrated, so only half the cycle time is required for an inspection. The high resolution of the sensor in the direction of travel is achieved by a sophisticated selection of optical components and a blue laser source of 20 µm width.
Result for the client:
The rugged design of the Q4-5 sensor configuration withstands the conditions in the surroundings of the inspection zone, proves to be stable and is able to recognize and to screen defective parts at once. Recorded measurement data deliver reliable statistics of the production quality, and hence have allowed an optimization of the entire production process.
QuellTech UG
Leonrodstrasse 56
80636 Muenchen, Germany
Contact: Stefan Ringwald
Phone: +49 89 12472375
Email: sringwald@quelltech.de
Web: http://www.quelltech.de/
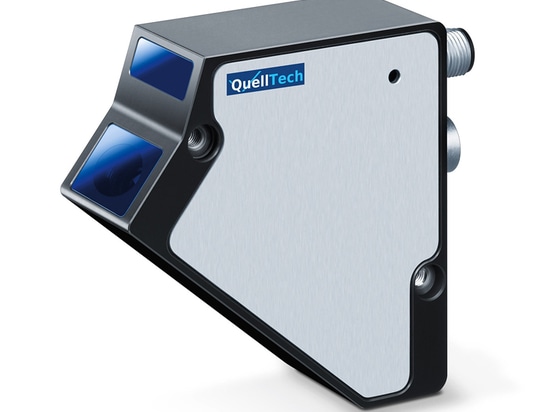