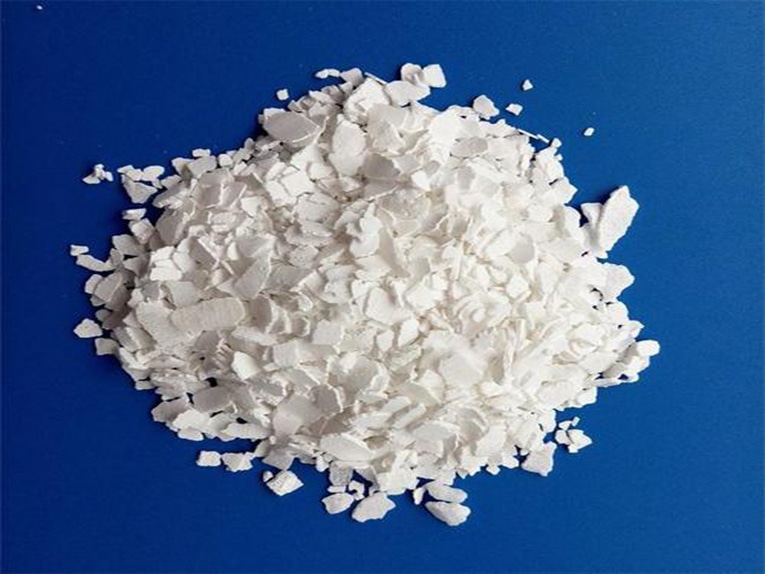
#Industry News
Calcium Chloride Dihydrate Drying Technology
Ideal Choice for Calcium Chloride Dihydrate Drying Equipment
Calcium chloride, a chemical substance composed of chlorine and calcium, has the chemical formula CaCl2. Slightly bitter. It is a typical ionic halide, which is white, hard pieces or particles at room temperature. Common applications include salt water, road ice melt and desiccant used in refrigeration equipment. Because it easily absorbs moisture and deliquesces in the air, anhydrous calcium chloride must be stored in a sealed container. Calcium chloride has important application value in the fields of food manufacturing, building materials, medicine and biology.
Calcium chloride is divided into calcium chloride dihydrate and anhydrous calcium chloride. For the drying of calcium chloride dihydrate, if user adopts fluidized drying process, the drying air temperature is high, the air volume is large, the heat utilization rate is low, the energy consumption is high, and the the exhaust gas volume is large, and the dust removal pressure is large.
The development directions of calcium chloride dihydrate drying process are as follows:
1) The emission of exhaust gas after drying should reach the emission standard and be minimized as possible;
2) Reducing steam consumption and electricity consumption, thereby reducing operating costs;
3) Large-scale equipment and high automation;
4) Stable operation of equipment and corrosion resistance.
The Annular Tube Split Type Steam Rotary Dryer of Shandong Tianli Energy Co., Ltd. is an ideal choice for calcium chloride dihydrate (annual output of 50,000 to 300,000 tons/set ) drying equipment. The steam rotary dryer is a rotary equipment that uses the heat of steam to dry materials through indirect heat exchange. The heat exchange tube in the dryer cylinder rotates with the cylinder body, and the material entering the dryer is lifted and stirred by the heat exchange tube in the cylinder body, and is dried by the heat provided by the heat exchange tube. The dried product moves from the higher end to the lower end by the inclination of the dryer, and is discharged from the discharge port at the lower end, and the moisture-carrying gas is discharged by the induced draft fan after purifying and dedusting. During the drying process, the material is in sliding contact heat exchange with the entire circumferential surface of the annular tubes with the rotation of the dryer. The contact method between the annular tubes and the material is the co-current full-area sliding contact heat exchange.
The Annular Tube Split Type Steam Rotary Dryer of Tianli Energy has the following characteristics:
1) More annular tubes per unit volume, larger heat exchange area;
2) The heat exchange tube components are easy to disintegrate, and each group of heat exchange tube components can be withdrawn separately from the feed end, which is convenient for maintenance and replacement;
3) The spacing of the heat exchange tubes is adjustable, which effectively improves the material flow state at the feed end;
4) The material and the annular tubes are in co-current contact, which can effectively reduce the wear of the material particles on the heat exchange tubes, especially suitable for highly abrasive materials, which greatly improves the service life of the heat exchange tubes;
5) The equipment runs stably and is suitable for continuous production. It can run continuously for 8000 hours annually.