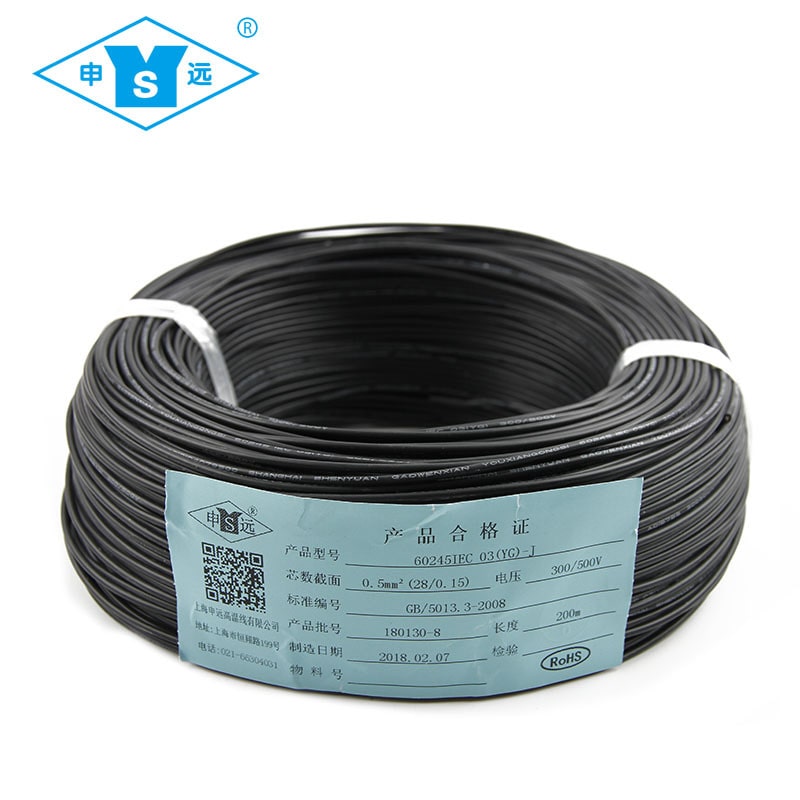
#White Papers
The wires are cracking again?
Cable insulation sheath material
In the past two years, the fluoroplastic insulated cable products have been cracked many times. Once the insulation layer is cracked, the supporting products will not be used. What is the problem that causes the cable insulation and sheath material to crack? How do you avoid that risk?"
The phenomenon of cable insulation sheath material cracking
Self - resolving cracking after heating in operation
Collision cracking at low temperature
Cracking found during long use or storage
Use discoloration and fragmentation outdoors
Mechanical damage cracking and other cracking
The reason of cable insulation sheath material cracking
The main component of cable insulation sheath material is high polymer, which relies on strong chemical bonds to maintain the fixed position of each other. Once the chemical bonds are damaged or damaged by external damage or aging, mainly due to oxidation reaction, the polymer chain will break a lot and its molecular weight will be reduced, which is finally reflected in the material cracking.
Cracking can be roughly classified into three categories:
Mechanical damage cracking
Chemical etching
Infiltration of strong acids, strong bases, solvents, gases and water
Chemical cracking of cable insulation sheath material. The principle is that corrosive chemicals and polymer materials have a chemical reaction, or get involved in the polymer, resulting in the polymer chemical bond rupture, thus the overall structure appears cracking phenomenon.
3 .Aging cracking
Electrical aging, thermal aging, photoaging
Aging and cracking of cable insulation sheath material. Its principle is light, electricity, heat and other energy to the polymer "intrusion" for a long time; As a result, electrons within the polymer may escape or undergo oxidation reactions, leading to the fracture of chemical bonds of the polymer and the degradation of the molecule, resulting in the cracking of the overall structure.
Ways to avoid cracking
According to the phenomenon of insulation and sheath cracking of electric wires and cables, the specific causes of cracking are analyzed, and specific solutions are adopted to effectively protect all links of material selection, production, transportation, installation and use.
Some common ways to avoid:
1. Choose materials that meet the application environment (voltage, temperature, oil and chemical resistance, etc.)
2. Pay attention to process parameters during production to avoid "internal injury" (stomata, water vapor, etc.)
3. Prevent collision during transportation
4. Installation, laying or cutting line assembly protection (pipe threading, light blocking, oil proofing, etc.)
Corresponding detection means
In order to prevent wire and cable cracking, different cable standards have their own detailed testing means, the implementation of these tests to verify and test products, is the guarantee of product safety.
Common test methods:
1. High temperature performance: thermal shock, thermal aging, thermal overload, thermal extension, high temperature pressure, thermal deformation
2. Low temperature performance: low temperature winding, low temperature impact, high and low temperature cycle
3. Oil resistance: oil resistance test, chemical resistance, ozone resistance, light resistance
4. Mechanical properties: tensile strength, elongation, rolling, extrusion, tearing
5. Three control experiments: mold, salt spray, damp and hot
Shenyuan newly developed -K1 and -K2 two series of products
In order to reduce the probability of product cracking, our company has been developing new anti-cracking materials with suppliers.After two years of research and development and efforts, is now officially launched two series of products: -K1 and -K2 series.
These two series of products mainly upgrade the original fluoroplastic products of our company and improve the mechanical properties of the products.
After two years of testing and testing, it has been verified that K1 and K2 series are materials with higher mechanical strength and better anti-cracking performance. At the same time, after customer use and feedback, it is verified that the performance of K1 and K2 series products is more excellent, there is no adverse phenomenon, anti-cracking performance is far better than ordinary fluoroplastic products!
Carefully make every meter cable, protect the safety of electricity in high temperature environment.
-- Shanghai Shenyuan Hi-Temp Wire Co.,Ltd