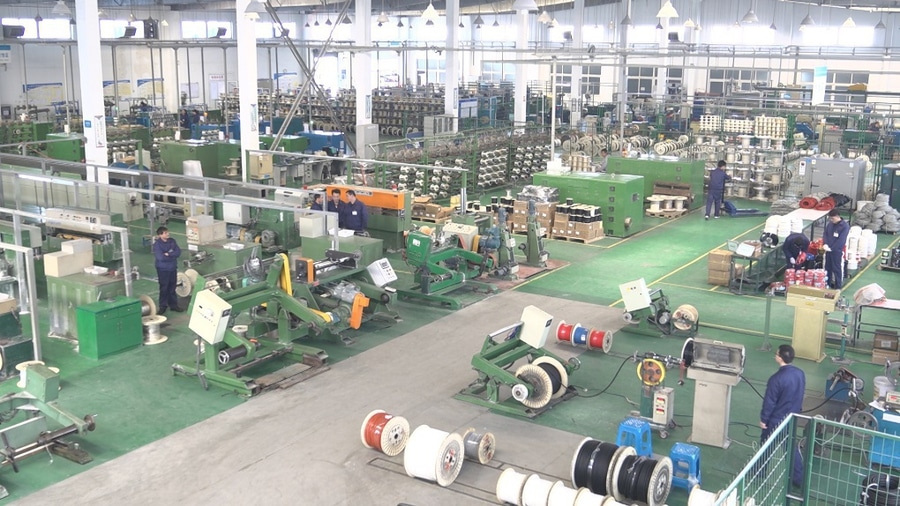
#Product Trends
Analysis of the advantages and disadvantages of common wire and cable insulation materials
cable insulation materials
UL758 series of electronic wire and high temperature special wire, its main insulation materials are polyvinyl chloride, crosslinked polyolefin, silicone rubber and fluoroplastics.The quality, processing efficiency and application range of wire and cable are directly affected by the type energy of insulation material.To fully understand the different characteristics of different insulation materials will be beneficial to material selection and product quality control.
PVC insulated wire and cable
PVC insulation material is a mixture of stabilizer, plasticizer, flame retardant, lubricant and other auxiliaries added in PVC powder.After decades of production and use, the current PVC manufacturing and processing technology has been very mature.
PVC insulation material has a very wide range of applications in the field of wire and cable, and has significant own characteristics:
In the wire surface color difference, matte, printing, processing efficiency, hardness, conductor adhesion, wire itself mechanical and physical properties and electrical properties can be effectively controlled, low cost, easy to process.
PVC insulated wire can easily reach the flame retardant grade specified in various standards and has very good flame retardant performance.
Generally used in rated 1000V AC and below voltage grade, can be widely used in household appliances, instrumentation, lighting, network communication and other industries.
PVC also has some disadvantages, which limit its use:
Because it contains a large amount of chlorine, a large amount of smoke will be emitted when burning, which will suffocate people, affect visibility, and produce some carcinogens and HCl gas, which will cause serious harm to the environment.
Poor performance of acid and alkali resistance, heat resistant oil and organic solvent resistance, and PVC wires are easily damaged and cracked in the specific environment.
With the development of low smoke halogen free insulation material manufacturing technology, gradually replacing PVC insulation has become the inevitable trend of cable development.
XLPE insulated wire and cable
XLPE insulation has the following advantages over thermoplastic polyethylene:
Improved heat resistance and deformation, and improved mechanical properties at high temperature;
Enhance chemical stability and solvent resistance, and basically maintain the original electrical properties;
The temperature can be up to 250℃ for a short time, and the carrying capacity of cross-linked polyethylene is much larger for the same thickness of wires and cables;
XLPE insulated wire and cable has excellent mechanical, waterproof and radiation resistance.
XLPE insulated wire and cable has obvious advantages, but also has some disadvantages of its own, which limits its use:
Poor heat resistance and adhesion. Overvoltage can easily cause the mutual adhesion between wires, which can seriously cause the insulation to break into short circuit.
Poor heat transfer resistance. Not suitable for temperature resistance above 200℃.
It is difficult to control the color difference between batches, and there is a certain bottleneck in manufacturing technology and high cost.
There is no relevant national standard for electrical and electronic connection wire of this kind of insulation wire.
Silicone rubber insulated wire and cable
Most silicon rubber wires and cables adopt cold extrusion and high temperature vulcanization process. In many synthetic rubber wires and cables, due to its unique molecular structure, silicon rubber has better performance than other ordinary rubber:
Very soft, good elasticity, tasteless and non-toxic, not afraid of high temperature and cold resistance.
Silicone rubber has much better heat resistance than ordinary rubber, can be used continuously at 200℃, can be used for a period of time at 350 ℃.
Silicone rubber has high resistivity and its resistance value remains stable over a wide range of temperature and frequency.
The silicon rubber insulated wire and cable has the above series of advantages, which are widely used in the high voltage installation line of TV set, high temperature resistance line of microwave oven, induction cooker, coffee pot, lamp lead, UV equipment, halogen lamp, oven and fan internal connection line, especially in the field of small household appliances.
But some of its own shortcomings limit its wider use, such as:
Poor tear resistance. Wear and tear easily, resulting in a short circuit. The current protection measures are silicone insulation plus glass fiber or high temperature polyester fiber braided layer.
The vulcanizing agent added in vulcanizing molding is mainly used at present, which contains chlorine element and completely halogen-free vulcanizing agent (such as platinum vulcanizing) has strict requirements on the production environment temperature and high cost.
XLEPDM wire insulation
XLEPDM insulated wire advantages of polyolefin insulated wire and ordinary rubber insulated wire:
Soft, flexible, elastic, high temperature non-adhesion, long-term aging resistance, resistance to harsh weather (-60 ~125 ℃).
Ozone resistance, uv resistance, electrical insulation resistance, chemical corrosion resistance.
Oil and solvent resistance is similar to that of general neoprene insulation. Common hot extrusion processing equipment is used for processing. Irradiation crosslinking is adopted to make the processing simple and low cost.
It is widely used in the fields of refrigeration compressor lead, waterproof motor lead, transformer lead, mine moving cable, drilling, automobile, medical equipment, ship berth and general electrical wiring.
The main disadvantages of XLEPDM wire are:
Poor tear resistance with XLPE and PVC wires.
Poor adhesion and self-viscosity, affecting the subsequent processing.
Fluoroplastic wire insulation
High temperature resistance, can adapt to high temperature environment of 150~250℃;
Under the condition of the same section conductor, fluoroplastic cable can transmit a larger allowable current, which greatly improves the application range of this kind of insulated wire. Because of this unique performance, fluoroplastic cable is often used in aircraft, ships, high temperature furnaces and electronic equipment internal wiring, wiring, etc.
Good flame retardancy, high oxygen index, small flame diffusion range and less smoke. The wires made from them are suitable for tools and places that require strict flame retardancy. For example: computer network, subway, vehicles, high-rise buildings and other public places.
Excellent electrical performance, lower permittivity of fluoroplastics. Therefore, compared with coaxial cables of similar structures, fluoroplastic cables have less attenuation and are more suitable for high-frequency signal transmission. It is commonly used as the internal wiring of transmission and communication equipment, the jumper between the feeder and transmitter and video audio line.
Perfect mechanical and chemical performance, weather aging resistance and mechanical strength; And is not affected by various acids, bases and organic solvents. Therefore, it is suitable for large environmental climate change and corrosive occasions, such as petrochemical, oil refining, oil well instrument control, etc.
Good for welding connection. As a result of the general plastic melting temperature is low, easy to melt at high temperature, the need for skilled welding technology, and some welding points must have a certain welding time, which has become the reason why fluorine plastic cable is popular. Such as communication equipment and electronic equipment internal wiring.