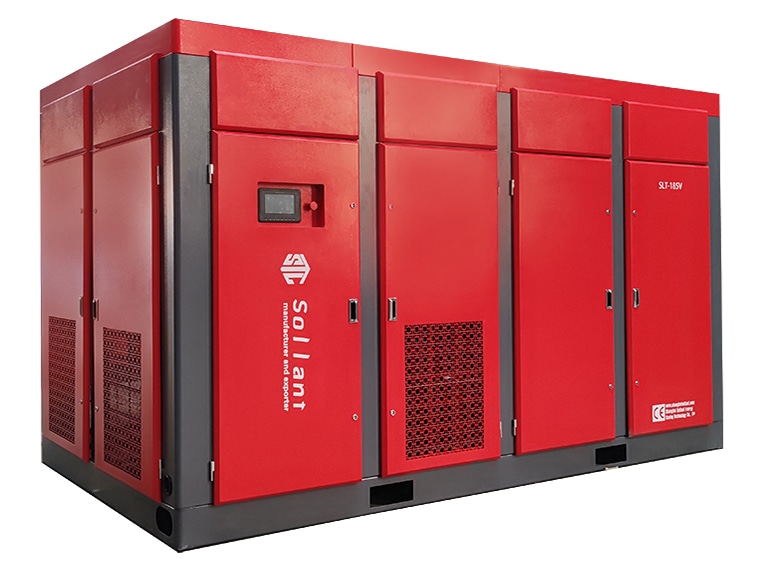
#Industry News
Precautions for the use of screw air compressors
The rotor of the screw air compressor must not be reversed. The rotor is the core component of the screw air compressor. The male screw has 4 teeth; the female screw has 6 grooves. The oil film protects and takes away the heat generated by the fricti
1.The output air pressure is generally 0.7MPa (the air inlet is 0), this air pressure and the radial force of the helical tooth rotation of the female and male screws cancel each other out, there is a gap of 0.02-0.04mm between the male and female screws, and the surfaces of the female and male screws do not touch . If the rotor reverses, the radial force of the helical tooth rotation of the female and male screws pushes to the right; the pressure of 0.7MPa at the air inlet (air outlet is 0) acts on the screw and pushes to the right, and the entire screw in the pump head moves to the right. There is friction between the end face of the screw and the inside of the pump head shell; the pressure cannot be established in the pump head, and the screw in the pump head has no lubricating oil, so the lubricating oil cannot be circulated, and the heat generated by friction in the pump head cannot be taken away, and heat is accumulated in the pump head instantly. High temperature is generated, which deforms the inner screw and outer shell of the pump head, and the female and male screws bite and lock. The end face of the inner rotor of the pump head and the end cover are stuck together due to high temperature, causing severe wear on the end face of the rotor, and even defect of parts, resulting in damage to the gearbox and rotor.
Method for checking the direction of rotation: Sometimes the phase sequence of the incoming line of the factory will change, or the incoming power supply of the screw air compressor will change, which will cause the phase sequence of the motor of the screw air compressor to change. Therefore, it is best to use a phase sequence meter to detect the phase sequence and Make a record. If there is no phase sequence table, be careful and mark the wiring before disconnecting the power line. If you forget to make a record, the following checks should be made before the air compressor is running: ① Press and hold the cooling fan contactor with your hand to see if the wind direction of the fan is correct. ② If the power line of the fan has been moved, manually jog the main motor momentarily to see if the rotation direction of the motor coupling is correct.
2. The rotor of the screw air compressor cannot deposit carbon:
(1) The cause of carbon deposition. ①Use low-quality lubricating oil that is not genuine from the original manufacturer. ② Use a fake or damaged air filter. ③Long time high temperature operation. ④The amount of lubricating oil is small. ⑤ When replacing the lubricating oil, the old lubricating oil is not drained or the old and new lubricating oil are mixed. ⑥ Mixed use of different types of lubricating oil.
(2) Check the carbon deposition method of the rotor. ①Remove the intake valve and observe whether there is carbon deposit on the inner wall of the pump head. ② Observe and analyze whether the lubricating oil contains carbon deposits from the surface of the oil filter and the inner wall of the lubricating oil pipeline.
(3) Required when checking the pump head. Non-professionals are not allowed to disassemble the screw air compressor pump head casing, and if there is carbon deposits in the pump head, only the professional and technical personnel of the manufacturer can repair it. The gap between the female and male screws in the pump head of the screw air compressor is very small, so be careful not to enter any impurities in the pump head during maintenance.
3. Regularly add grease to the motor bearing, and add it with an oil gun. The specific steps: ①Open the hole opposite the oil nozzle. ②The oil nozzle of the oil gun should be matched with the motor. ③Lubricating grease is divided into high-speed motor grease and low-speed motor grease; the two cannot be mixed, otherwise the two will react chemically. ④ The amount of oil in the oil gun is 0.9g per press, and 20g is added each time, and it needs to be pressed 23 times. ⑤If the grease is added less, the grease will not lubricate on the oil pipeline; if it is added too much, the bearing will heat up, and the grease will become liquid, which will affect the lubrication quality of the bearing. ⑥ Add once every 2 000 hours of operation of the air compressor.
4.Replacement of the main motor coupling The coupling should be replaced in the following situations: ①There are cracks on the surface of the coupling. ② The surface of the coupling is scorched. ③The coupling glue is broken.