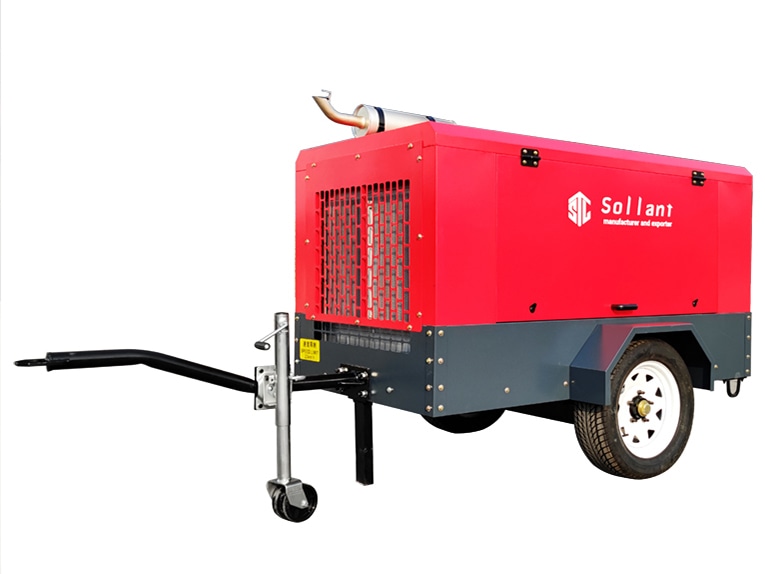
#Product Trends
Sequence of air compressor empty operation - air compressor load operation
1. How does the air compressor run empty? Answer: The air compressor must first run empty and then run under load in the official test run. The sequence of empty runs is as follows:
(1) Remove the intake and exhaust valves at all levels.
(2) When the air compressor starts idling, first turn on the motor starter switch several times in succession to observe the running direction of the air compressor and whether the various mechanisms are working normally. If there is no abnormal phenomenon, then switch on and run for 5 minutes, 30 minutes, and 4-8 hours in sequence. Check the condition of each part of the air compressor before each operation, and start and operate after confirming that it is normal.
(3) When the moving mechanism adopts circulating lubrication, the pressure before the lubricating oil is input into the distribution piping system during operation shall not exceed the specified value in the equipment technical documents, but shall not be lower than 1 kg/c㎡. The temperature of the lubricating oil in the crankcase or the fuselage is: the air compressor with a crosshead must not exceed 60°C; the air compressor without a crosshead must not exceed 70°C.
(4) The acoustic response of each moving part during operation is normal, and there must be no impact sound or noise.
(5) During dry operation, the fasteners of the connecting parts of the air compressor should not be loose.
(6) The oil injector should fill the cylinder well, and the cooling water should be smooth.
2. How does the air compressor operate under load?
Answer: The first load operation of the air compressor is carried out after empty operation and purging.
The air compressor should operate under load according to the following requirements:
(1) After starting the machine, gradually close the vent cutting or oil-water blowing cutting, and run for 1 hour at 1/4 rated pressure of the air compressor; run for 4-8 hours at 1/2 rated pressure.
(2) The air compressor operates under the minimum pressure, and the pressure can only be increased gradually after there is no abnormal phenomenon;
(3) For large-scale high-pressure air compressors, the operating time at nominal pressure shall not be less than 24 hours;
(4) During operation, check the following items:
——The pressure, temperature and oil supply of lubricating oil. The oil pressure shall not be lower than 1 kg/c㎡ before being sent into the distribution piping system. The lubricating oil in the crankcase or the fuselage should be wet: the air compressor with a crosshead should not exceed 60°C. The temperature without crosshead shall not exceed 70°C.
——The air compressor runs smoothly, and the sound of each moving part should be normal.
——Measure the inlet and outlet water temperature and check the cooling water supply. The cooling water is not allowed to flow intermittently, have air bubbles and blockage. The cooling water discharge temperature shall not exceed 40°C.
——The flange parts, shaft seals, intake and exhaust valves, cylinder heads and water jackets of various national surveying and mapping bureaus must not leak air, oil or water.
——Intake and exhaust valves should work normally and be safe and sensitive.
——There must be no loosening of the connecting parts.
——Measuring the exhaust gas temperature and pressure at all levels shall comply with the provisions of each technical condition.
——The heating condition and current value of the electric motor shall comply with the regulations.
(5) After the operation is completed, disassemble and inspect the following items:
Disassemble the gas cutting at all levels and the front cover of the cylinder at all levels, check the friction of the cylinder mirror, and find out the reason if there are friction marks.
——Check the friction on the surface of the piston rod, and there should be no wear marks and dragging phenomenon.
——Disassemble the gas cuttings at all levels, check the fit between the cutting pieces and the cutting body, and replace them with spare parts if there are cracks in the cutting pieces.
——Check the friction between the cross slide and the friction surface of the fuselage guide rail.
——Remove the connecting rod big end shoe and crosshead pin, and check the friction condition of the friction surface.
——Replace the lubricating oil in the fuselage. After the air compressor runs for the first time, due to the loosening of the machine parts and the cleaning effect of the lubricating oil, a large amount of finely divided metal powder enters the lubricating oil. Therefore, all the lubricating oil should be replaced after the machine has been working for 24 hours. After running for 200 hours, change the oil again. After changing twice, change the oil according to the regular maintenance requirements.
——In order to make the joint evenly, there must be sufficient lubricating oil everywhere during the initial operation.