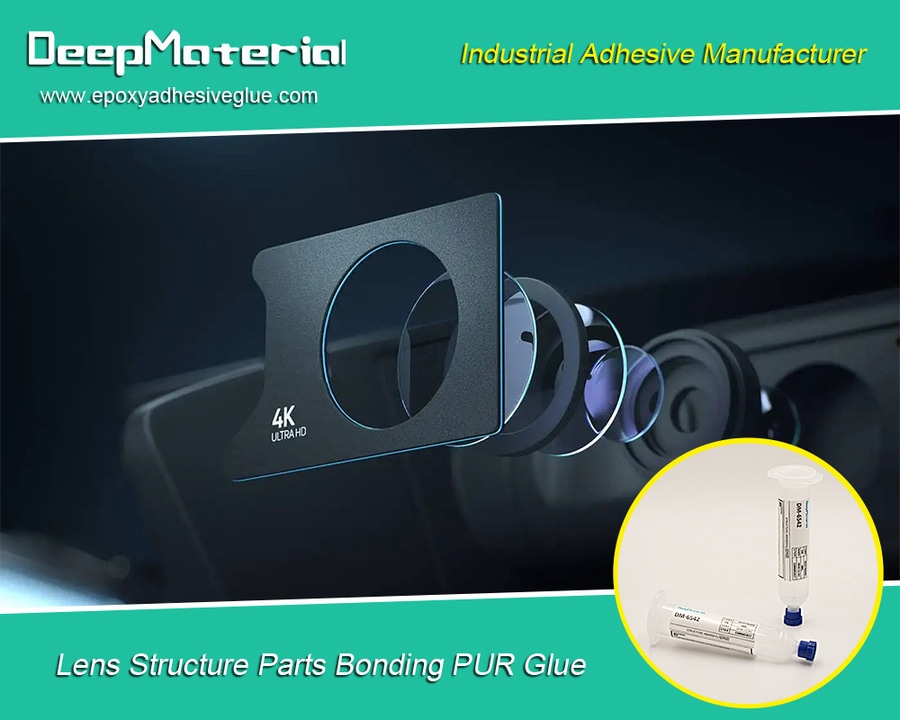
#Industry News
How To Find The Best Silicone Conformal Coating For PCB Manufacturer?
Best Silicone Conformal Coating For PCB Manufacturer
Silicone conformal coating is among the most popular for protecting electronic circuit boards. But just with the rest of the coating materials, you need to be careful with the product you choose if at all you are to achieve the desired results. Some of the important factors to consider when buying conformal coatings are:
• The price
• Environmental considerations
• Chemical resistance
• Temperature operating range
• The curing process
• Application requirements
When looking at silicone conformal coating, the environmental considerations and temperature range of operation are some of the most important factors. By looking at the two, you should be in a position to select the most suitable product for the protection needs you have.
Temperature range
Assemblies coated with conformal materials are exposed to different temperature ranges depending on their operations and functions. When seeking a good silicone coating, it helps to start by looking at the minimum and maximum temperatures the product can handle. You can then use this to compare the conditions the device is likely exposed to throughout its service life.
Estimating the assembly’s potential temperature exposure requires realistic and holistic appraisal; you might need expert advice. For instance, boards operating in unheated aircraft parts can reach -65 degrees when the aircraft is airborne and +100 degrees when on the runway. The heating effects on your circuit should be with regard to such projections. For silicone, the operating range is -65 degrees to + 150 degrees. The material can survive the range even with extended use.
Environmental considerations
Circuit boards are exposed to varying deleterious environments depending on what the devices are meant to do. Units placed in a protective housing that is partially sealed will have the conformal coating as secondary protection. They can be subjected to humidity and condensation as temperature changes within the housing. Acrylic is widely used for such, even though silicone is the better option for condensing environments. Below is what you should factor in when evaluating silicone coating for your application:
High humidity – Silicone materials are more porous to water vapor than other coating options when there is high humidity. In this regard, urethanes and acrylics tend to have better resistance to areas with high humidity levels; they offer better barriers because they are 2-component materials cross-linking significantly.
Corrosive gases – Corrosive environments are the toughest to protect because the gases expose voids and defects in the coating applied. Single-component materials are susceptible to corrosive gases; usually, two-component ones will be used for such areas. However, there are 1-part components that are UV curable and offer good resistance. Silicone materials work by reacting to create chemical bonds with metal surfaces to protect them from corrosion. Single-part silicone chemistries will, therefore, still offer good corrosion resistance.
Salt spray – when it comes to salt spray environments, you will only be successful when the assembly coating is even, void-free and uniform. Saltwater is chemically benign to conformal coatings, and silicone materials are used for such environments.
There is so much to consider when choosing the right conformal coating material. Even though silicone is among the best you can choose, it helps ensure it is ideal for your application. Get as much information as possible, and get assistance from conformal coating experts if need be.
For more about how to find the best silicone conformal coating for pcb manufacturer,you can pay a visit to DeepMaterial at https://www.epoxyadhesiveglue.com/how-to-evaluate-the-best-silicone-conformal-coating/ for more info.