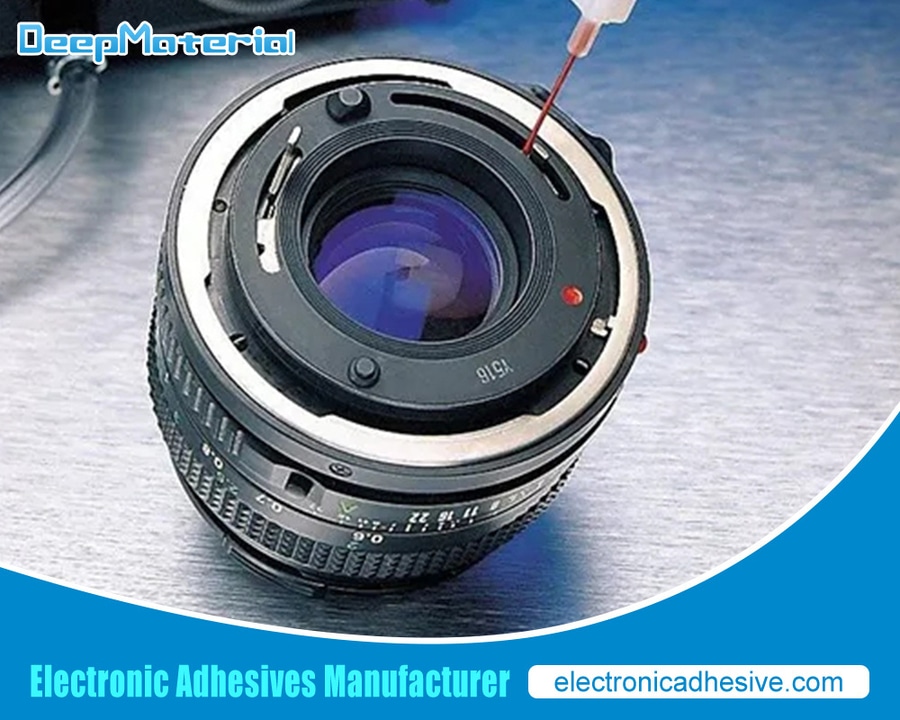
#Industry News
he Best Adhesive Glue for Electronics: A Comprehensive Guide
Best Electronic Adhesive Glue Manufacturer
Choosing adhesive glue is crucial for ensuring optimal performance and durability in electronics. Electronics require specialized adhesives that handle various factors such as heat, moisture, and electrical conductivity. This article provides an in-depth look at the best adhesive glues for electronics, discussing their types, properties, applications, and considerations to help you make an informed decision.
1. Understanding Adhesive Types for Electronics
Electronics use adhesives for various purposes, including securing components, providing insulation, and enhancing structural integrity. The primary types of adhesives used in electronics are:
1.1. Epoxy Resins
Epoxy resins are widely used in the electronics industry due to their excellent adhesive properties and resistance to environmental factors. These adhesives are known for their strong bonding capabilities and are ideal for applications requiring durability and chemical resistance.
Advantages:
Strong Bonding:Epoxy resins create a solid, durable bond that can withstand mechanical stresses and vibrations.
Chemical Resistance:They resist chemicals, solvents, and moisture, making them suitable for harsh environments.
Electrical Insulation:Epoxy resins provide excellent insulation, preventing short circuits and electrical interference.
Disadvantages:
Curing Time:Epoxy resins typically require a curing time ranging from a few hours to several days, depending on the formulation.
Difficulty in Removal:Once cured, epoxy resins are difficult to remove, which can be a disadvantage if repairs or modifications are needed.
Popular Epoxy Resins:
Loctite E-120HP:Known for its high strength and resistance to temperature extremes.
Araldite 2011:Offers a balance of strength and flexibility, suitable for various electronic applications.
1.2. Silicone Adhesives
Silicone adhesives are renowned for their flexibility and resistance to extreme temperatures. They are commonly used in electronics where thermal expansion and contraction are significant factors.
Advantages:
Flexibility:Silicone adhesives remain flexible even after curing, making them ideal for components that experience thermal cycling.
Temperature Resistance:They can withstand high and low temperatures without degrading, making them suitable for electronic devices exposed to varying temperatures.
Moisture Resistance:Silicone adhesives are highly resistant to moisture and can withstand exposure to water and humidity.
Disadvantages:
Lower Strength:Compared to epoxy resins, silicone adhesives may have lower shear strength, which can be a limitation for specific applications.
Long Cure Time:Some silicone adhesives have a longer curing time, which can delay manufacturing.
Popular Silicone Adhesives:
Dow Corning 3145 RTV:Provides excellent thermal stability and flexibility, suitable for high-temperature applications.
Momentive RTV162:Known for its moisture resistance and long-term reliability.
1.3. Acrylic Adhesives
Acrylic adhesives offer a fast cure time and high shear strength, making them suitable for applications requiring rapid assembly. They are often used to bond plastics and metals in electronics.
Advantages:
Fast Curing:Acrylic adhesives typically cure quickly, accelerating the manufacturing process.
High Strength:They provide solid bonds and can handle high shear and peel forces.
Versatility:Acrylic adhesives can bond various materials, including plastics, metals, and glass.
Disadvantages:
Limited Temperature Resistance:Acrylic adhesives may not perform better in extreme temperatures than silicone adhesives.
Lower Chemical Resistance:They may resist certain chemicals and solvents less.
Popular Acrylic Adhesives:
3M Scotch-Weld DP420:Offers high strength and fast curing, suitable for metal and plastic bonding.
Loctite 406:Known for its fast setting time and strong bond on various substrates.
1.4. Conductive Adhesives
Conductive adhesives are used in electronics to provide both mechanical bonding and electrical conductivity. They are essential for applications such as attaching components to circuit boards and connecting conductive traces.
Advantages:
Electrical Conductivity:Conductive adhesives can conduct electricity, essential for making electrical connections in electronic devices.
Thermal Conductivity:Some conductive adhesives also provide thermal conductivity, helping dissipate heat from electronic components.
Disadvantages:
Cost:Conductive adhesives can be more expensive than non-conductive adhesives due to the materials used in their formulation.
Limited Flexibility:Some conductive adhesives may be less flexible, which can be a limitation in applications with significant thermal or mechanical movement.
Popular Conductive Adhesives:
Loctite 382:Provides good electrical and thermal conductivity, suitable for bonding components in electronic assemblies.
MG Chemicals 8331:Known for its high conductivity and resistance to temperature extremes.
2. Choosing the Right Adhesive Glue for Your Electronics
Selecting the appropriate adhesive glue for electronic applications depends on several factors. Here are vital considerations to help you choose the suitable adhesive:
2.1. Application Requirements
Bond Strength:Determine the strength of the bond required for your application. Epoxy resins may be more suitable for high-stress areas, while silicone adhesives may be better for flexible components.
Temperature Range:Consider the operating temperature range of the electronics. Choose an adhesive that can withstand the temperatures the device will be exposed to.
Moisture Exposure:If the electronics will be exposed to moisture or humidity, select an adhesive with good moisture resistance, such as silicone adhesives.
2.2. Material Compatibility
Substrate Materials:Ensure the adhesive is compatible with your bonding materials. Some adhesives work better with plastics, while others are designed for metals or glass.
Surface Preparation:Proper surface preparation is crucial for achieving a solid bond. Follow the manufacturer’s recommendations for cleaning and preparing surfaces before applying the adhesive.
2.3. Curing Time and Process
Curing Time:Consider the adhesive’s curing time and how it fits into your manufacturing process. Fast-curing adhesives can speed up production but ensure sufficient bonding strength.
Application Method:Choose an adhesive that is easy to apply and suitable for manufacturing. Some adhesives come in easy-to-use dispensers, while others may require specialized equipment.
2.4. Cost and Availability
Budget:Evaluate the cost of the adhesive in your budget. While high-performance adhesives may be more expensive, they may also provide better long-term performance and reliability.
Availability:Ensure that the adhesive is readily available from suppliers or manufacturers. Availability can affect production timelines and costs.
3. Application Tips for Electronics Adhesives
Proper application of adhesives is essential for achieving the best results. Here are some tips to ensure adequate bonding in electronics:
3.1. Surface Preparation
Cleaning:Clean the surfaces to be bonded to remove any contaminants, such as dust, grease, or moisture. Use appropriate cleaning agents and ensure the surfaces are completely dry before applying the adhesive.
Roughening:For some adhesives, roughening the surfaces can improve bonding strength. Lightly sand or abrade the surfaces to create a better grip for the adhesive.
3.2. Mixing and Application
Mixing:If using a two-part adhesive, follow the manufacturer’s instructions for mixing the components. Inaccurate mixing can affect the curing process and bond strength.
Application:Apply the adhesive evenly to the surfaces to be bonded. Avoid excessive application, which can lead to mess and potential bonding issues.
3.3. Curing and Testing
Curing:The adhesive can cure fully according to the manufacturer’s instructions. Do not disturb the bonded parts during curing, as this can affect the bond strength.
Testing:Test the bond strength and performance after curing to ensure it meets your application’s requirements. Perform any necessary quality checks before final assembly or use.
4. Future Trends in Adhesive Technology for Electronics
The adhesive industry continues to evolve with advancements in technology and materials. Here are some trends to watch for in the future:
4.1. Advanced Materials
Nanotechnology:Researchers are exploring using nanomaterials to enhance adhesive properties, such as improving strength, conductivity, and flexibility.
Biodegradable Adhesives:There is growing interest in developing environmentally friendly adhesives that degrade over time, reducing environmental impact.
4.2. Enhanced Performance
High-Performance Adhesives:New formulations are being developed to improve performance in extreme conditions, such as high temperatures and aggressive chemicals.
Smart Adhesives:Innovative adhesives with embedded sensors or responsive properties are being explored for applications in intelligent electronics and wearable devices.
4.3. Automation and Application Techniques
Automated Dispensing:Advances in automated dispensing systems make applying adhesives accurately and efficiently in manufacturing processes easier.
Precision Bonding:Improved application techniques enable more precise bonding in complex electronic assemblies, enhancing overall reliability and performance.
Conclusion
Choosing the best adhesive glue for electronics requires careful consideration of the adhesive types, application requirements, and specific needs of your project. Epoxy resins, silicone adhesives, acrylic adhesives, and conductive adhesives offer unique advantages and are suited for different applications. By understanding the properties and applications of these adhesives, you can make informed decisions and ensure the reliability and performance of your electronic devices.
Whether you’re working on consumer electronics, industrial equipment, or specialized devices, selecting the suitable adhesive and applying it correctly will contribute to your electronic products’ overall quality and longevity. Stay informed about the latest trends and advancements in adhesive technology to keep up with the evolving demands of the electronics industry.
For more about choosing the best adhesive glue for electronics: a comprehensive guide, you can pay a visit to DeepMaterial at https://www.electronicadhesive.com/ for more info.