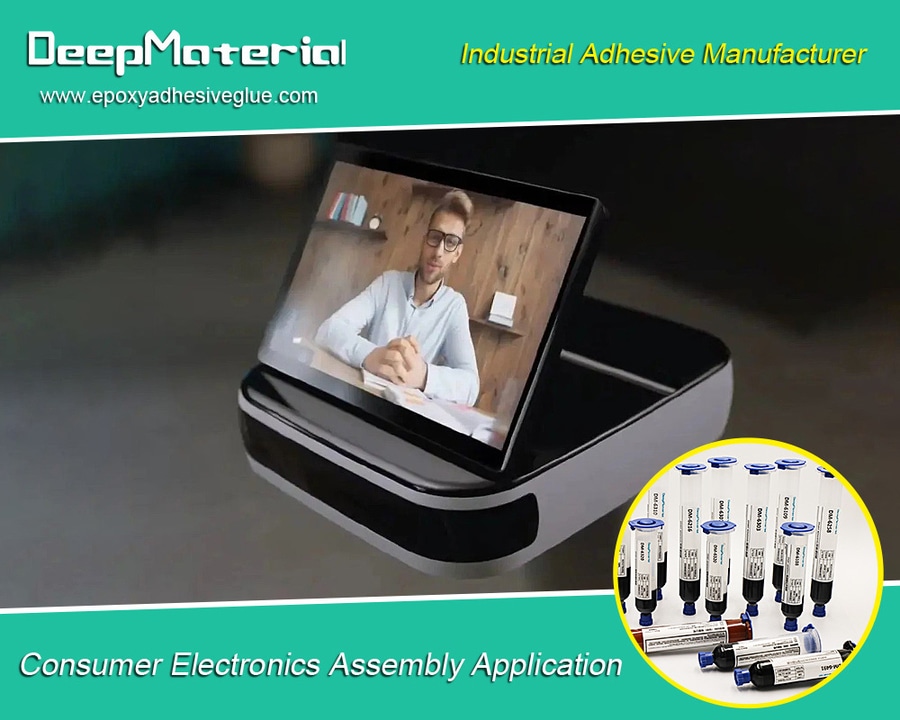
#Industry News
The BGA underfill process with underfill epoxy and other options
Best BGA Underfill Process Adhesive Glue Manufacturer
BGA stands for ball grid array. These need reliable underfill, and different materials can be used. BGA underfill protects circuit boards so that they don’t get damaged by different environmental threats, such as thermal damage. In industries such as medical, automotive, and aircraft electronics, there may be frequent severe shock and vibration. The process of adding an underfill is very beneficial to keep everything safe and in place.
Automated and manual underfill options
When picking a BGA underfill, you should evaluate your particular application and ensure that you find something that matches. At deep material, you can get a custom-made underfill if it is needed.
The underfill process can be automated or manual. This is the only way to find the best service. Different things determine the type of process that is needed. The first thing to do is find out which components within the assembly are most sensitive and need underfill. The right underfill material is chosen as well as the BGA underfill process for your PCB.
Working with the best manufacturer or supplier ensures that you find a product with the best specifications. It helps to find a curing process and underfill applications adaptable to the project and the needs. These processes are easy to adjust and readjust as needed until you find an optimal process for the application.
BGA underfill process
This is a surface-mount packaging that can be used for PCB assemblies. It can be used to mount devices such as microprocessors permanently. BGA makes it possible to use more interconnection pins instead of flat packages or dual lines because the bottom surfaces can be used instead of the perimeter alone. Interconnects are usually susceptible and fragile. They can therefore be easily damaged by impact and moisture. The underfill is added to protect the assembly and create better mechanical and thermal properties.
In many underfill processes, epoxies are used as the substance of choice. However, silicone and acrylic materials can also be used. The BGA underfill needs to offer the best thermal and moisture performances while providing a good component attached to the PCB as required.
The process involves:
• The application of the underfill in a line at the edge or corner of BGA
• Once the application has been made, the BGA has to be heated
• Through capillary action, the underfill is absorbed under the BGA
• The temperature is then maintained up to the time the underfill gets cured. This can take five minutes or hours. This usually depends on the material in use.
When BGA underfill is used in PCB assembly, it gives a strong mechanical bond between the circuit board and the BGA component. This also offers good protection to solder joints against forms of physical stress. Underfill material also helps heat transfer between the board and the component. In some cases, it acts as the heat sink for your component.
Choosing the right manufacturer
For superior outcomes, you have to be keen about where you source your underfill. Deep material stands as one of the best underfill manufacturers. You can get your BGA underfill custom-made to suit your needs specifically. DeepMaterial has been in the market for a long time and is well-versed in creating high-quality underfills and adhesives for various applications.