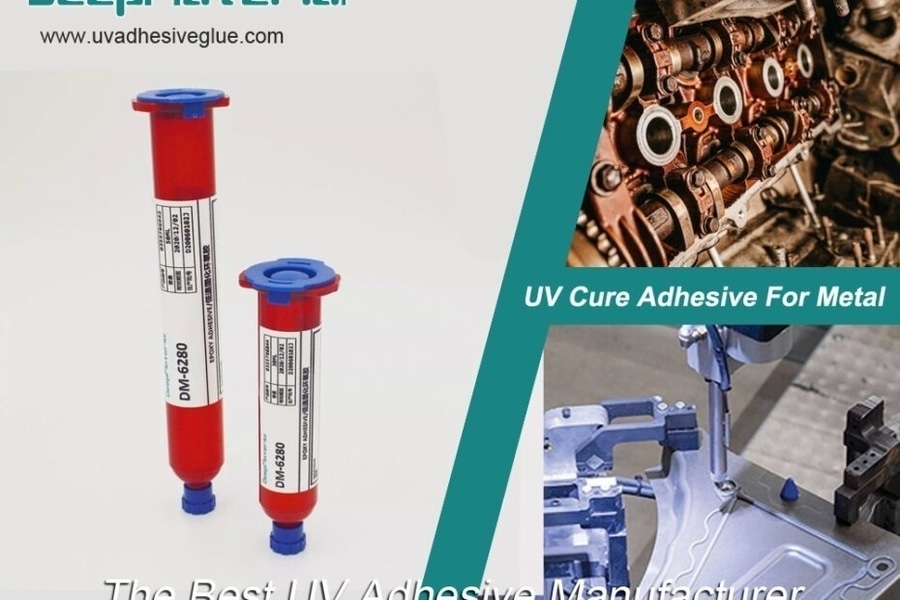
#Industry News
What Are The Characteristics Of UV Curing Adhesive? Is It UV Cure Adhesive For Metal?
Best UV Adhesive Glue For Metal Manufacturer
UV curing adhesives, also known as ultraviolet-curing adhesives or UV adhesives, are a type of adhesive that cures or solidifies when exposed to ultraviolet (UV) light. These adhesives have gained popularity in various industries due to their fast curing times, strong bonding capabilities, and versatility. While UV cure adhesive for metals, their suitability depends on several factors. Here are the general characteristics of best uv glue for metals:
Characteristics of UV Curing Adhesives:
Rapid Curing: UV curing adhesives cure quickly when exposed to UV light. This rapid curing process can take just a few seconds to a few minutes, depending on the adhesive formulation and the intensity of the UV light. This fast curing process allows for increased production speed and efficiency.
Strong Bonding: UV adhesives are known for creating strong bonds. They form cohesive bonds between surfaces, creating a robust and durable connection. The bond strength can vary depending on the specific adhesive and the substrates being bonded. UV curing adhesives can provide strong and durable bonds on a wide range of substrates, including metals.
Low Heat Generation: UV curing is a relatively low-temperature process compared to some other adhesive curing methods.UV adhesives cure without generating significant heat. This is especially important for sensitive materials and components that could be damaged by heat during the bonding process. This makes it suitable for bonding heat-sensitive materials and prevents damage to the substrates.
Clear and Transparent: UV adhesives often dry clear and transparent, making them suitable for applications where aesthetics or optical clarity are important, such as in glass bonding applications.
Versatility: UV adhesives are compatible with various materials, allowing for bonding between different substrates, including metals, plastics, glass, ceramics, and more. This versatility makes them useful in a wide range of applications.
Environmental Friendliness: compared to solvent-based adhesives, UV adhesives are often solvent-free and have low or no volatile organic compounds (VOCs), making them more environmentally friendly compared to some traditional adhesive types.
Controlled Curing: The curing process of UV adhesives is highly controllable. The adhesive remains liquid until it’s exposed to UV light, allowing for precise alignment and positioning of parts before curing.This is particularly useful for applications that require accuracy.
Resistance to Chemicals and Temperature: Some UV adhesives offer good resistance to chemicals, moisture, and temperature variations, enhancing their performance and durability in various environments.
No Mixing Required: Unlike two-part adhesives that require mixing before application, UV adhesives are typically single-component formulations that don’t need pre-mixing, this simplifies the adhesive process and reduces the chances of mixing errors.
Limited Gap Filling: UV adhesives are generally best suited for applications with minimal gaps between surfaces to be bonded. Their ability to fill larger gaps is limited compared to some other adhesive types.
Customizable Formulations: UV curing adhesives can be formulated to meet specific requirements, such as flexibility, hardness, or chemical resistance, depending on the intended application.
No Post-Curing: UV adhesives typically don’t require additional post-curing processes once the initial UV exposure is complete, further streamlining production processes.
Low Odor: UV adhesives tend to have low or no odor, contributing to a more pleasant working environment for operators.
Low Shrinkage: UV adhesives often exhibit low levels of shrinkage during the curing process, reducing the likelihood of stress on bonded components.
Precise Application: UV adhesives can be applied precisely to small or intricate areas, making them suitable for applications that require fine detail.
Curing On Demand: The adhesive remains in its liquid state until exposed to UV light. This characteristic allows for greater control over the curing process, enabling adjustments and corrections before curing.
Adhesion to Different Substrates: UV adhesives can bond to a wide range of substrates, making them versatile in various industries, including electronics, medical devices, optics, automotive, and more.
It’s important to note that the performance of UV curing adhesives can vary based on factors such as adhesive formulation, substrate type, surface preparation, and curing equipment. Therefore, it’s essential to select the appropriate adhesive for a specific application and follow recommended application procedures for optimal results.
Use of UV Curing Adhesives on Metal:
UV curing adhesives can be used effectively to bond metal surfaces, but the success of the bonding process depends on several factors. These factors include the type of metal, surface preparation, adhesive formulation, and the specific requirements of the application. Here are some considerations for using UV cure adhesive for metal:
Surface Preparation: Proper surface preparation is crucial for achieving strong and durable bonds on metal surfaces. Metals are often coated with oils, residues, or oxidation layers that can hinder adhesion. Surface cleaning and, in some cases, roughening or treating the surface can improve adhesion.
Bond Strength: The bond strength achieved with UV curing adhesives on metal can be quite high, but it depends on factors like the adhesive formulation, surface preparation, and the specific conditions the bonded parts will be exposed to.Testing and selecting the appropriate adhesive for the specific metal application is essential.In some cases, surface treatments like primers or adhesion promoters might be necessary to enhance bonding.
Metal Type: UV adhesives can be used on various metal types, including aluminum, stainless steel, copper, and more. Different metals have varying surface energies and properties that can affect adhesion. Some metals, like aluminum or stainless steel, can form oxide layers that need to be addressed for effective bonding. Different adhesive formulations may be recommended for specific metal types.
UV Transparency: Metals are generally opaque and can block UV light. For effective curing, it’s important to choose an adhesive that can transmit UV light through the metal or to ensure that the adhesive can cure in the presence of some degree of blocked UV light.
Adhesive Formulation: There are UV curing adhesives specifically formulated for bonding metals. These adhesives are designed to provide good adhesion to metal surfaces, offering appropriate bond strength and durability.
UV Penetration: UV light needs to penetrate the adhesive and reach the interface between the adhesive and the metal surface to ensure proper curing. This may require careful consideration of adhesive thickness and the light absorption properties of the materials involved.
Gap Size: UV curing adhesives are generally better suited for applications with minimal gap sizes between the bonded surfaces. Larger gaps can lead to incomplete curing and reduced bond strength.
Curing Equipment: The equipment used to deliver UV light for curing must be properly calibrated and matched to the adhesive’s curing requirements. Insufficient exposure to UV light can result in incomplete curing and weaker bonds.
Compatibility: Some metals may react with certain adhesive formulations, affecting the bond strength or causing other issues. Compatibility testing is recommended, especially for critical applications.
Temperature and Environment: Consider the temperature range and environmental conditions the bonded parts will experience. Some UV curing adhesives may have limitations regarding their resistance to extreme temperatures or exposure to certain chemicals.
Application: UV curing adhesives can be used in various metal bonding applications, including electronics, automotive, medical devices, and optical components. It’s important to consider the specific requirements of each application and select an appropriate adhesive formulation.
In summary, UV curing adhesives can be effectively used on metal surfaces when the proper adhesive formulation is selected, and the metal surfaces are appropriately prepared. These adhesives offer rapid curing, strong bonds, and controlled application, making them suitable for various metal bonding applications across industries such as electronics, automotive, aerospace, and more. It’s important to consult with adhesive manufacturers and conduct thorough testing to ensure the desired bond strength and performance are achieved for your specific metal bonding needs.
For more about choosing the best UV glue for metal, you can pay a visit to DeepMaterial at https://www.uvadhesiveglue.com/uv-glue-for-glass-to-metal/ for more info.