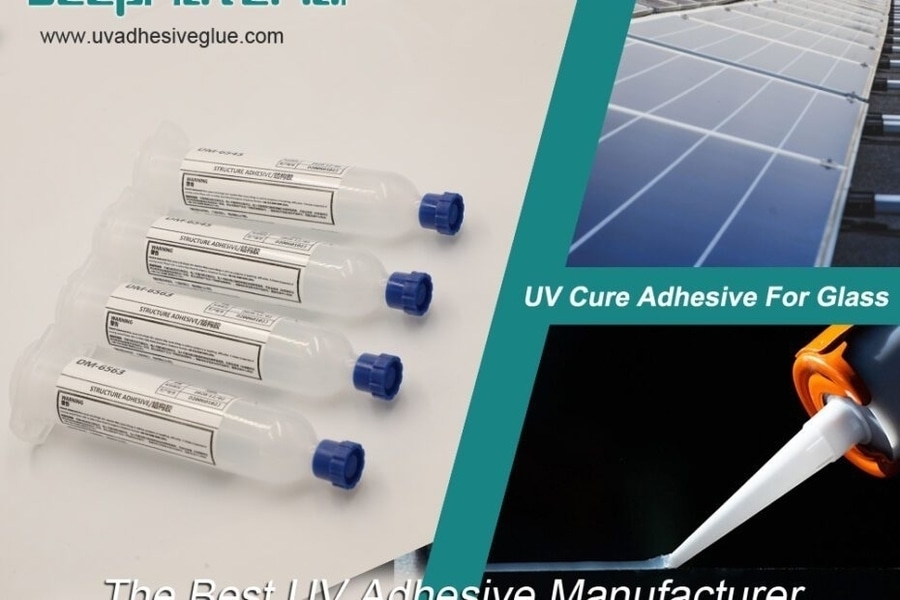
#Industry News
How UV Curable Adhesive Systems Improve Efficiency in Automotive Assembly
Best UV Adhesive Glue Manufacturer
UV curable adhesive systems are a type of adhesive that cures when exposed to ultraviolet (UV) light. These adhesive systems have become increasingly popular in automotive assembly due to their numerous benefits and efficiency. Adhesive systems play a crucial role in automotive assembly as they are used to bond various components together, ensuring structural integrity and durability of the vehicle.
Benefits of UV Curable Adhesive Systems in Automotive Assembly
One of the key benefits of UV curable adhesive systems in automotive assembly is their faster curing time. Unlike traditional adhesives that require hours or even days to fully cure, UV curable adhesives can cure within seconds when exposed to UV light. This significantly reduces the assembly time and allows for faster production cycles.
In addition to faster curing time, UV curable adhesive systems also offer improved bond strength. These adhesives form strong bonds that are resistant to temperature fluctuations, vibrations, and other environmental factors. This ensures that the components remain securely bonded throughout the lifespan of the vehicle.
Another advantage of UV curable adhesive systems is the reduced waste and rework. Traditional adhesives often require mixing and have limited pot life, which can lead to waste if not used within a certain timeframe. UV curable adhesives, on the other hand, do not require mixing and have an unlimited pot life until exposed to UV light. This eliminates the need for excess adhesive and reduces the chances of rework due to adhesive failure.
Furthermore, UV curable adhesive systems offer increased design flexibility. These adhesives can be applied in precise amounts and in various patterns, allowing for intricate bonding of different components. This flexibility in design enables automotive manufacturers to create innovative and lightweight vehicles without compromising on strength and durability.
How UV Curable Adhesive Systems Improve Efficiency in Automotive Assembly
The use of UV curable adhesive systems in automotive assembly improves efficiency in several ways. Firstly, the reduced assembly time due to faster curing allows for increased production speed. This means that more vehicles can be manufactured within a given timeframe, leading to higher productivity and profitability.
Moreover, UV curable adhesive systems contribute to improved quality control. The fast curing time ensures that the adhesive bonds are formed consistently and uniformly, reducing the chances of defects or inconsistencies in the assembly process. This results in higher quality vehicles that meet or exceed industry standards.
Additionally, the use of UV curable adhesive systems in automotive assembly leads to lower labor costs. The fast curing time eliminates the need for lengthy drying or curing processes, reducing the amount of time and labor required for assembly. This allows manufacturers to optimize their workforce and allocate resources more efficiently.
Types of UV Curable Adhesive Systems Used in Automotive Assembly
There are several types of UV curable adhesive systems used in automotive assembly, each with its own unique properties and applications. Acrylic-based adhesives are commonly used for bonding interior and exterior components, as they offer excellent adhesion to a wide range of substrates and have good resistance to temperature and humidity.
Epoxy-based adhesives are another type of UV curable adhesive system used in automotive assembly. These adhesives provide high bond strength and are often used for structural bonding applications, such as bonding metal components together. Epoxy-based adhesives also offer excellent chemical resistance and durability.
Silicone-based adhesives are preferred for applications that require flexibility and resistance to extreme temperatures. These adhesives can withstand high temperatures without losing their adhesive properties, making them suitable for bonding components in the engine compartment or other areas exposed to heat.
Factors to Consider When Choosing UV Curable Adhesive Systems for Automotive Assembly
When choosing UV curable adhesive systems for automotive assembly, several factors need to be considered. Firstly, the substrate materials play a crucial role in determining the type of adhesive system to be used. Different adhesives have varying adhesion properties to different substrates, so it is important to select an adhesive that is compatible with the materials being bonded.
Environmental conditions also need to be taken into account. Factors such as temperature, humidity, and exposure to chemicals or UV radiation can affect the performance of the adhesive. It is important to choose an adhesive system that can withstand the specific environmental conditions of the automotive assembly process.
Curing requirements are another important consideration. Some applications may require a fast curing time, while others may require a longer curing time for proper bonding. It is essential to select an adhesive system that can meet the specific curing requirements of the assembly process.
Production volume is also a factor to consider when choosing UV curable adhesive systems. High-volume production may require adhesives that can be applied quickly and efficiently, while low-volume production may allow for more manual application methods. The adhesive system chosen should be able to meet the production volume requirements without compromising on quality or efficiency.
Applications of UV Curable Adhesive Systems in Automotive Assembly
UV curable adhesive systems have a wide range of applications in automotive assembly. One common application is the bonding of interior and exterior components, such as dashboard panels, door trims, and exterior body panels. UV curable adhesives provide strong and durable bonds that can withstand the rigors of daily use and exposure to various environmental factors.
Glass bonding is another important application of UV curable adhesive systems in automotive assembly. These adhesives are used to bond windshields, windows, and sunroofs to the vehicle body. The fast curing time of UV curable adhesives allows for efficient installation of glass components, ensuring a secure and watertight bond.
Structural bonding is a critical application where UV curable adhesive systems are used. These adhesives are used to bond metal components together, providing structural integrity and strength to the vehicle. The high bond strength and durability of UV curable adhesives make them ideal for applications that require load-bearing capabilities.
Sealing and gasketing is another important application of UV curable adhesive systems in automotive assembly. These adhesives are used to create seals and gaskets that prevent leaks and provide protection against moisture, dust, and other contaminants. UV curable adhesives offer excellent sealing properties and can be applied in precise amounts to ensure a tight and reliable seal.
Final Thoughts
In conclusion, UV curable adhesive systems offer numerous benefits and are becoming increasingly popular in automotive assembly. The faster curing time, improved bond strength, reduced waste and rework, and increased design flexibility make these adhesive systems highly desirable for automotive manufacturers.
The efficiency improvements brought about by UV curable adhesive systems, such as reduced assembly time, increased production speed, improved quality control, and lower labor costs, contribute to higher productivity and profitability for automotive manufacturers.
For more about choosing the UV Curable Adhesive, you can pay a visit to DeepMaterial at https://www.epoxyadhesiveglue.com/uv-curing-uv-adhesive/ for more info.