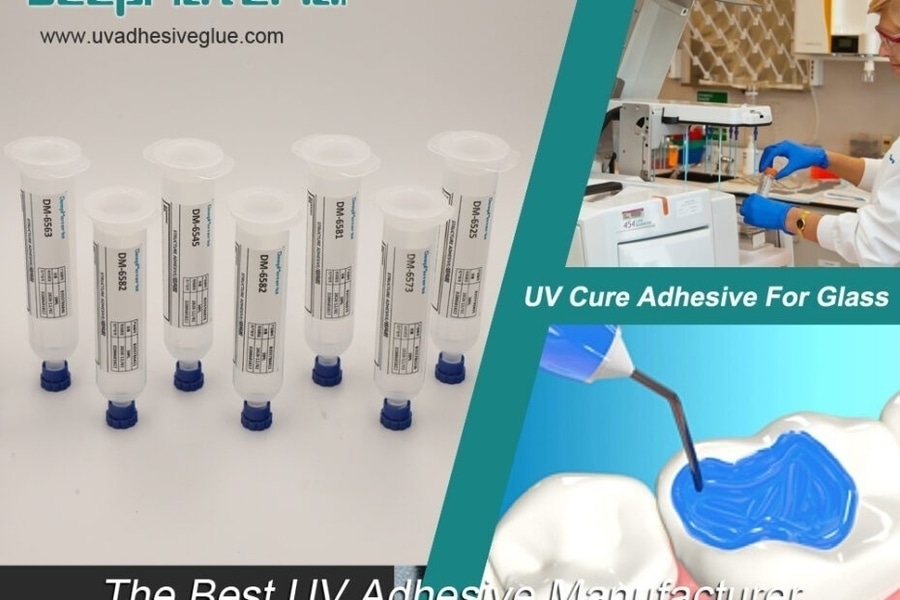
#Industry News
Innovations In UV Curable Pressure Sensitive Adhesive for Electronics Assembly
Best UV Curable Pressure Sensitive Adhesive Glue Manufacturer
UV curable pressure sensitive adhesive (PSA) plays a crucial role in electronics assembly. It is a type of adhesive that cures when exposed to ultraviolet (UV) light, creating a strong bond between two surfaces. This adhesive is widely used in the electronics industry due to its ability to provide fast and reliable bonding, as well as its compatibility with various substrates and materials.
In this post, we will explore the importance of adhesives in electronics assembly, the challenges faced in this field, and how UV curable PSA technology has advanced to address these challenges.
The Importance of Adhesives in Electronics Assembly
Adhesives play a vital role in electronics assembly as they are used to bond various components together. They provide mechanical support, electrical conductivity, and thermal management, ensuring the reliability and functionality of electronic devices. The choice of adhesive is crucial as it must meet the specific requirements of the application, such as temperature resistance, flexibility, and compatibility with different materials.
Choosing the right adhesive for electronics assembly is essential to ensure the longevity and performance of the final product. The adhesive must be able to withstand the harsh conditions that electronic devices are exposed to, such as temperature fluctuations, moisture, and vibrations. It should also provide excellent adhesion to different substrates, such as metals, plastics, and glass. Additionally, the adhesive should have good electrical conductivity to ensure proper functioning of electronic circuits.
Challenges in Electronics Assembly and the Need for Innovation
Electronics assembly faces several challenges that require innovative solutions in adhesive technology. One of the main challenges is miniaturization, where electronic components are becoming smaller and more complex. This poses difficulties in bonding these tiny components together, as traditional adhesives may not provide sufficient strength or precision.
Another challenge is thermal management, as electronic devices generate heat during operation. Adhesives used in electronics assembly must be able to dissipate heat effectively to prevent overheating and damage to the components. Additionally, the adhesive should have good thermal stability to withstand high temperatures without losing its adhesive properties.
Furthermore, the increasing demand for environmentally friendly and sustainable solutions has led to the need for adhesives that are free from harmful substances, such as volatile organic compounds (VOCs) and hazardous chemicals. Adhesive manufacturers are constantly innovating to develop adhesives that meet these requirements while maintaining high performance and reliability.
Advancements in UV Curable Pressure Sensitive Adhesive Technology
In recent years, there have been significant advancements in UV curable PSA technology to address the challenges faced in electronics assembly. These advancements include improved curing speed, enhanced bond strength, and increased flexibility.
One of the key advancements is the development of UV LED curing systems, which provide faster and more efficient curing compared to traditional UV lamps. UV LED curing systems emit a narrow spectrum of UV light, allowing for precise control of the curing process. This results in faster production cycles and reduced energy consumption.
Another advancement is the formulation of UV curable PSAs with improved bond strength. These adhesives can provide strong and durable bonds even in challenging environments. They have excellent adhesion to various substrates, including metals, plastics, and glass, ensuring reliable bonding in electronic devices.
Furthermore, UV curable PSAs with increased flexibility have been developed to accommodate the miniaturization trend in electronics assembly. These adhesives can bond delicate and flexible components without causing damage or stress. They also have good resistance to temperature fluctuations and vibrations, ensuring the longevity of electronic devices.
Benefits of UV Curable Pressure Sensitive Adhesive in Electronics Assembly
UV curable PSA offers several benefits in electronics assembly compared to other adhesive types. One of the main advantages is its fast curing time. UV curable PSAs can cure within seconds when exposed to UV light, allowing for faster production cycles and increased productivity. This is especially beneficial in high-volume manufacturing environments.
Another benefit is the ability to achieve precise and uniform bond lines. UV curable PSAs can be applied in thin and uniform layers, ensuring consistent bonding across the entire surface. This results in improved reliability and performance of electronic devices.
UV curable PSAs also offer excellent adhesion to a wide range of substrates, including metals, plastics, and glass. They have good compatibility with different materials, ensuring reliable bonding in various electronic applications. Additionally, UV curable PSAs have good resistance to temperature fluctuations, moisture, and chemicals, making them suitable for harsh environments.
Applications of UV Curable Pressure Sensitive Adhesive in Electronics Assembly
UV curable PSA is used in various applications in electronics assembly. One of the main applications is bonding surface mount components to printed circuit boards (PCBs). UV curable PSAs provide strong adhesion between the components and the PCB, ensuring reliable electrical connections. They also offer excellent thermal management, dissipating heat generated by the components.
Another application is bonding flexible circuits and displays. UV curable PSAs can bond delicate and flexible components without causing damage or stress. They provide excellent adhesion to flexible substrates, ensuring reliable bonding in flexible electronic devices.
UV curable PSAs are also used in the assembly of touchscreens and displays. They provide optical clarity and excellent adhesion to glass substrates, ensuring high-quality displays. UV curable PSAs can also be used to bond protective films and coatings to electronic devices, providing scratch resistance and durability.
Testing and Quality Control of UV Curable Pressure Sensitive Adhesive
Testing and quality control are essential in ensuring the consistency and reliability of UV curable PSA in electronics assembly. Various tests are conducted to evaluate the adhesive’s performance, such as bond strength, peel strength, shear strength, and temperature resistance.
Bond strength tests measure the force required to separate the bonded surfaces. Peel strength tests measure the force required to peel the adhesive from a substrate. Shear strength tests measure the force required to slide one surface relative to another. These tests ensure that the adhesive provides sufficient strength and durability in the specific application.
Temperature resistance tests evaluate the adhesive’s ability to withstand high temperatures without losing its adhesive properties. The adhesive is subjected to elevated temperatures for a specified period, and its bond strength is measured before and after the test. This ensures that the adhesive can withstand the operating conditions of the electronic device.
Final Recommendation
In conclusion, UV curable pressure sensitive adhesive plays a crucial role in electronics assembly. It provides fast and reliable bonding, excellent adhesion to various substrates, and good thermal management. The advancements in UV curable PSA technology have addressed the challenges faced in electronics assembly, such as miniaturization and thermal management.For more about choosing a UV Curable Pressure Sensitive Adhesive for Electronics Assembly, you can pay a visit to DeepMaterial at https://www.uvadhesiveglue.com/ for more info.