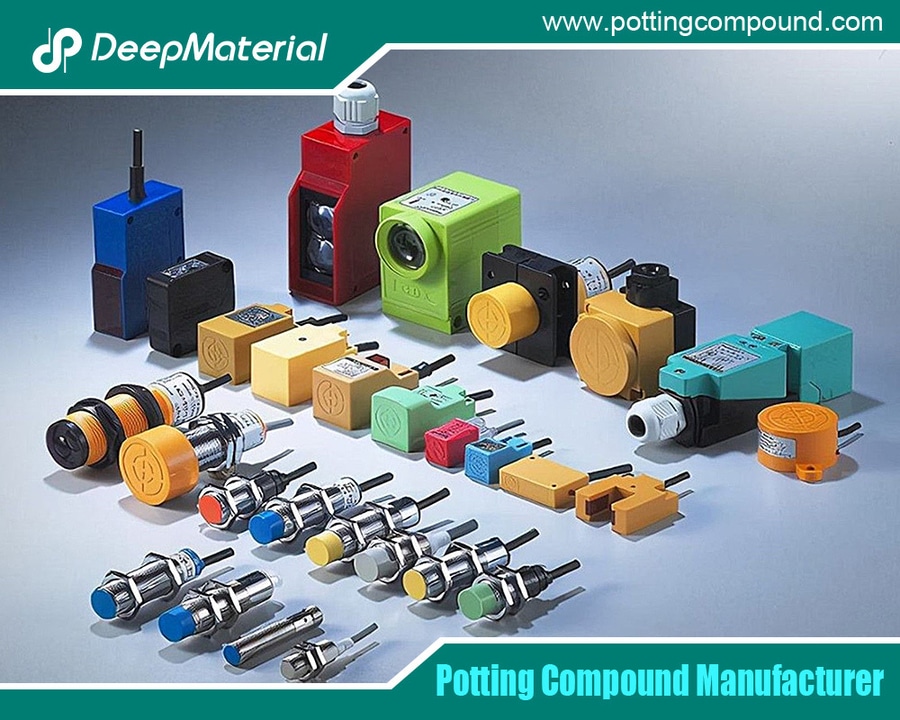
#Industry News
The Potting and Encapsulation Process: An In-Depth Guide
Best Potting Adhesive Glue Manufacturer
In the world of manufacturing and electronics, safeguarding components is paramount. Potting and encapsulation are two methods that serve this purpose. They are often used interchangeably, but they have distinct processes and applications. Potting involves enclosing a component in a protective material, while encapsulation refers to coating or encasing it. Both methods offer significant benefits, such as enhanced durability, protection against moisture, and improved thermal management. Understanding the potting and encapsulation processes can help manufacturers and engineers make informed decisions regarding their applications, materials, and techniques.
What is Potting?
Potting is the process of enclosing electronic components in a solid or gel-like material. This technique provides a barrier against environmental factors, such as moisture, dust, and chemicals, as well as mechanical stresses like vibrations and impacts.
Key Characteristics of Potting
Material Choices:Potting materials can include epoxies, polyurethanes, silicones, and other thermosetting resins. The choice of material depends on the specific application and required properties.
Application:Potting is commonly used to encapsulate circuit boards, sensors, and connectors to improve reliability and extend lifespan.
Thermal Management:The potting material can aid in heat dissipation, helping to prevent overheating in electronic components.
What is Encapsulation?
Encapsulation involves surrounding or coating a component with a protective layer. This technique offers similar protective benefits to potting but may allow for some degree of flexibility and ease of removal.
Key Characteristics of Encapsulation
Material Choices:Encapsulation materials can include various polymers, resins, and thermoplastics, selected based on the required properties and application.
Application:Common uses for encapsulation include protecting sensitive components in medical devices, electronics, and even pharmaceuticals.
Reworkability:Unlike potting, which often involves a permanent seal, encapsulation can allow for easier removal or replacement of components if necessary.
Applications of Potting and Encapsulation
Both potting and encapsulation processes are widely utilized across various industries, including:
Electronics
Circuit Boards:Potting protects circuit boards from moisture and mechanical stress.
Sensors:Encapsulation keeps sensors safe from environmental hazards, ensuring accurate readings.
Automotive
Electronic Components:Potting and encapsulation safeguard electronic control units (ECUs) and sensors from extreme temperatures and vibrations.
Aerospace
Critical Systems:Both processes protect vital components from the harsh conditions of high altitudes and varying temperatures.
Medical Devices
Safety and Reliability:Encapsulation is essential for protecting sensitive medical electronics and ensuring patient safety.
Telecommunications
Signal Integrity:Potting protects telecommunications equipment from interference and damage.
Materials Used in Potting and Encapsulation
The choice of material is crucial in both potting and encapsulation processes. Here are some commonly used materials:
Epoxy Resins
Durability:Excellent mechanical strength and resistance to chemicals.
Thermal Stability:Suitable for high-temperature applications.
Polyurethane
Flexibility:Provides a degree of flexibility, making it suitable for applications that experience movement.
Moisture Resistance:Highly resistant to moisture and various environmental factors.
Silicone
High-Temperature Resistance: Effective in high-temperature environments.
Electrical Insulation:Excellent electrical insulation properties.
Thermoplastics
Ease of Processing:Thermoplastics can be molded and shaped easily.
Reworkability:They can be removed and replaced without damaging the underlying component.
The Potting Process
The potting process involves several key steps to ensure effective encapsulation. Here’s a detailed look at the typical potting process:
Preparation
Component Cleaning:Clean the components to remove dust, grease, or contaminants that may affect adhesion.
Mold Design:Create or select a mold that fits the potted component.
Mixing
Material Preparation:Mix the selected potting compound according to the manufacturer’s instructions, ensuring proper ratios and consistency.
Pouring
Filling the Mold: Carefully pour the mixed compound into the mold, ensuring even coverage and avoiding air bubbles.
Curing
Setting Time:The potting compound can cure according to the manufacturer’s specifications. Curing times may vary depending on the material type and ambient conditions.
Finishing
Trimming and Cleaning:Once cured, remove any excess material and clean the component to achieve a finished appearance.
The Encapsulation Process
The encapsulation process is similar but focuses on coating or surrounding the component. Here’s a closer look at the encapsulation process:
Component Preparation
Cleaning:Like potting, cleaning the component is essential to ensure good adhesion.
Application
Coating Techniques:Apply the encapsulation material using spraying, dipping, or brushing to adequately cover the component.
Curing or Drying
Setting Time:The encapsulation material can cure or dry depending on the type used.
Quality Inspection
Inspection:Conduct a thorough inspection to ensure complete coverage and adhesion and identify defects.
Advantages of Potting and Encapsulation
Both potting and encapsulation processes offer several advantages, including:
Protection from Environmental Factors
Moisture:Both processes protect components from moisture, reducing the risk of corrosion and failure.
Dust and Debris:Potting and encapsulation prevent dust ingress and other contaminants.
Mechanical Protection
Impact Resistance: Encasing components enhances their resistance to impacts and vibrations.
Thermal Management: Proper materials help dissipate heat, preventing overheating.
Electrical Insulation
Safety:Potting and encapsulation provide excellent electrical insulation, reducing the risk of shorts and improving safety.
Extended Lifespan
Durability:Encapsulated and potted components often have a longer lifespan due to enhanced protection.
Cost-Effectiveness
Reduced Failures:By preventing damage, the need for repairs and replacements is minimized, ultimately saving costs.
Best Practices for Potting and Encapsulation
To achieve optimal results in potting and encapsulation, consider the following best practices:
Material Selection
Choose the Right Material:Select materials based on application requirements, such as temperature resistance, flexibility, and chemical exposure.
Proper Preparation
Thorough Cleaning:Ensure all components are clean and contaminant-free to promote adhesion.
Controlled Environment
Temperature and Humidity:Conduct potting and encapsulation in a controlled environment to ensure proper curing and minimize defects.
Accurate Mixing
Follow Instructions:Adhere to manufacturer guidelines for mixing compounds to achieve desired properties.
Quality Assurance
Conduct Inspections:Regularly inspect the finished products to ensure compliance with quality standards.
Conclusion
The potting and encapsulation processes are vital in protecting components across various industries. By understanding the nuances of each method, manufacturers and engineers can make informed decisions that enhance the performance and longevity of their products. With different materials available and multiple applications, the potting and encapsulation processes are essential for safeguarding components from environmental hazards, mechanical stress, and chemical exposure. By following best practices and choosing suitable materials, manufacturers can ensure that their products are reliable, durable, and effective in meeting industry standards. As technology advances, the importance of potting and encapsulation will continue to grow, solidifying their place in the manufacturing and electronics landscape.
For more about choosing the potting and encapsulation process: an in-depth guide, you can pay a visit to DeepMaterial at https://www.pottingcompound.com/ for more info.