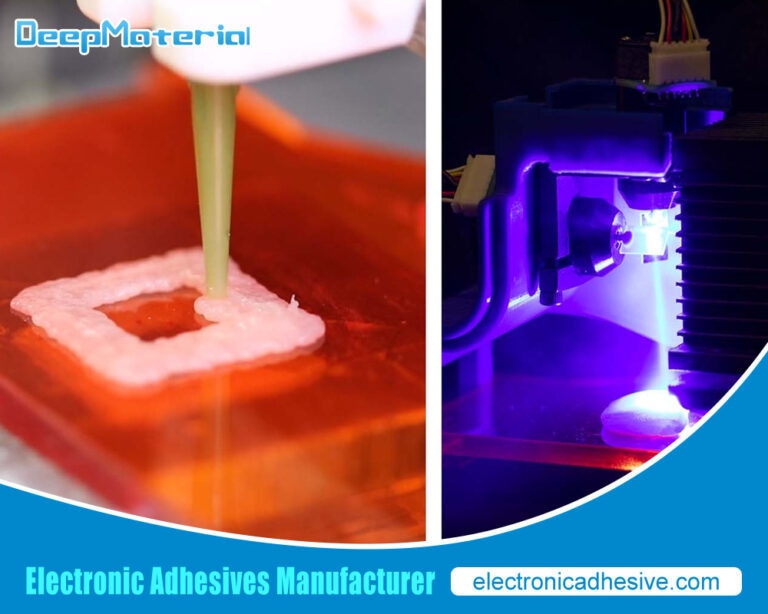
#Industry News
Overcoming Challenges in Electronics Assembly with Membrane Bonding Adhesive
Best Electronics Assembly with Membrane Bonding Adhesive Glue Manufacturer
As technology continues to evolve at a rapid pace, the demand for smaller, more efficient, and more reliable electronic devices is increasing. This demand presents a unique set of challenges for manufacturers who must constantly innovate to meet these evolving needs. One such challenge lies in the assembly process itself – specifically, in the bonding of electronic components. Traditional bonding methods often fall short when it comes to meeting the stringent requirements of modern electronic devices. This is where membrane bonding adhesive comes into play.
Membrane bonding adhesive has emerged as a game-changer in electronics assembly, offering a solution that not only meets but exceeds the demands of today’s high-tech devices. This innovative adhesive technology provides superior bond strength, excellent durability, and exceptional performance under extreme conditions. However, like any new technology, it also brings its own set of challenges that manufacturers must learn to navigate.
In this blog post, we will delve into the world of membrane bonding adhesive in electronics assembly. We will explore its benefits and potential applications, discuss the challenges associated with its use, and provide insights into how these challenges can be effectively overcome. Whether you are a seasoned professional in the electronics industry or a novice just starting out, this post will equip you with valuable knowledge and practical tips to help you succeed in your endeavors with membrane bonding adhesive.
Common Challenges in Electronics Assembly
One of the common challenges faced in electronics assembly is adhesion issues. Adhesion is crucial in ensuring that electronic components are securely bonded to the substrate or circuit board. However, traditional adhesives may not provide sufficient adhesion strength, especially when bonding dissimilar materials or when exposed to harsh environmental conditions. This can lead to component failure and reduced reliability.
Another challenge is thermal management. Electronic components generate heat during operation, and it is important to dissipate this heat to prevent overheating and damage. Traditional adhesives may not have good thermal conductivity, which can result in hot spots and reduced performance. Additionally, thermal expansion and contraction can cause stress on the bonded components, leading to failure over time.
Durability is also a concern in electronics assembly. Electronic components are often exposed to various environmental factors, such as moisture, chemicals, and temperature fluctuations. Traditional adhesives may not have good resistance to these factors, leading to degradation and failure of the bonded components.
How Membrane Bonding Adhesive Can Help Overcome These Challenges
Membrane bonding adhesive offers several benefits that can help overcome the challenges in electronics assembly. Firstly, it provides improved adhesion strength compared to traditional adhesives. Membrane bonding adhesive is specifically formulated to bond dissimilar materials and provide excellent adhesion even in harsh environmental conditions. This ensures that electronic components are securely bonded to the substrate or circuit board, reducing the risk of failure.
Secondly, membrane bonding adhesive has good thermal conductivity. This allows for efficient heat transfer from the electronic components to the substrate or circuit board, preventing overheating and ensuring optimal performance. Additionally, membrane bonding adhesive has good resistance to thermal expansion and contraction, reducing stress on the bonded components and increasing their durability.
Lastly, membrane bonding adhesive offers excellent durability. It has good resistance to moisture, chemicals, and temperature fluctuations, ensuring that the bonded components remain protected and functional even in challenging environments. This increases the reliability and lifespan of the electronic assembly.
Advantages of Using Membrane Bonding Adhesive in Electronics Assembly
The use of membrane bonding adhesive in electronics assembly offers several advantages. Firstly, it provides improved adhesion compared to traditional adhesives. This is especially important when bonding dissimilar materials or when exposed to harsh environmental conditions. The strong adhesion provided by membrane bonding adhesive ensures that electronic components are securely bonded to the substrate or circuit board, reducing the risk of failure.
Secondly, membrane bonding adhesive has good thermal conductivity. This allows for efficient heat transfer from the electronic components to the substrate or circuit board, preventing overheating and ensuring optimal performance. The ability to effectively manage heat is crucial in electronics assembly, as it can significantly impact the reliability and lifespan of the electronic components.
Lastly, membrane bonding adhesive offers excellent durability. It has good resistance to moisture, chemicals, and temperature fluctuations, ensuring that the bonded components remain protected and functional even in challenging environments. This increases the reliability and lifespan of the electronic assembly, reducing the need for frequent repairs or replacements.
Future Developments in Membrane Bonding Adhesive for Electronics Assembly
The field of membrane bonding adhesive is constantly evolving, with new developments and technologies being introduced. One emerging trend is the development of new formulations that offer improved performance characteristics. For example, there are ongoing efforts to develop adhesives with even higher adhesion strength, better thermal conductivity, and increased durability. These advancements will further enhance the capabilities of membrane bonding adhesive in electronics assembly.
Another area of development is the improvement of curing methods. Researchers are exploring new curing techniques that can reduce curing time and improve production efficiency. This includes the use of advanced curing technologies, such as UV LED curing and microwave curing. These developments will allow for faster and more efficient bonding processes.
Factors to Consider When Choosing Membrane Bonding Adhesive for Electronics Assembly
When selecting a membrane bonding adhesive for electronics assembly, there are several factors to consider. Firstly, substrate compatibility is important. The adhesive should be compatible with the materials being bonded to ensure proper adhesion and durability. It is important to consider the specific requirements of the application and choose an adhesive that is suitable for the materials involved.
Temperature resistance is another important factor to consider. The adhesive should be able to withstand the temperature extremes that the electronic components may be exposed to during operation. It is important to choose an adhesive that has good temperature resistance to prevent degradation and failure.
Curing time is also a consideration. The adhesive should have a curing time that is compatible with the production process. Some adhesives may require longer curing times, which can impact production efficiency. It is important to choose an adhesive that can cure within the desired timeframe.
Conclusion: The Importance of Membrane Bonding Adhesive in Overcoming Challenges in Electronics Assembly
Finally, membrane bonding adhesive plays a crucial role in overcoming the challenges faced in electronics assembly. It provides improved adhesion, thermal management, and durability compared to traditional adhesives. By selecting the right membrane bonding adhesive for each application and following best practices for its use, manufacturers can ensure reliable and durable electronic assemblies. With ongoing developments in the field, the capabilities of membrane bonding adhesive will continue to improve, further enhancing its importance in electronics assembly.
For more about choosing the Membrane Bonding Adhesive, you can pay a visit to DeepMaterial at https://www.electronicadhesive.com/about/ for more info.