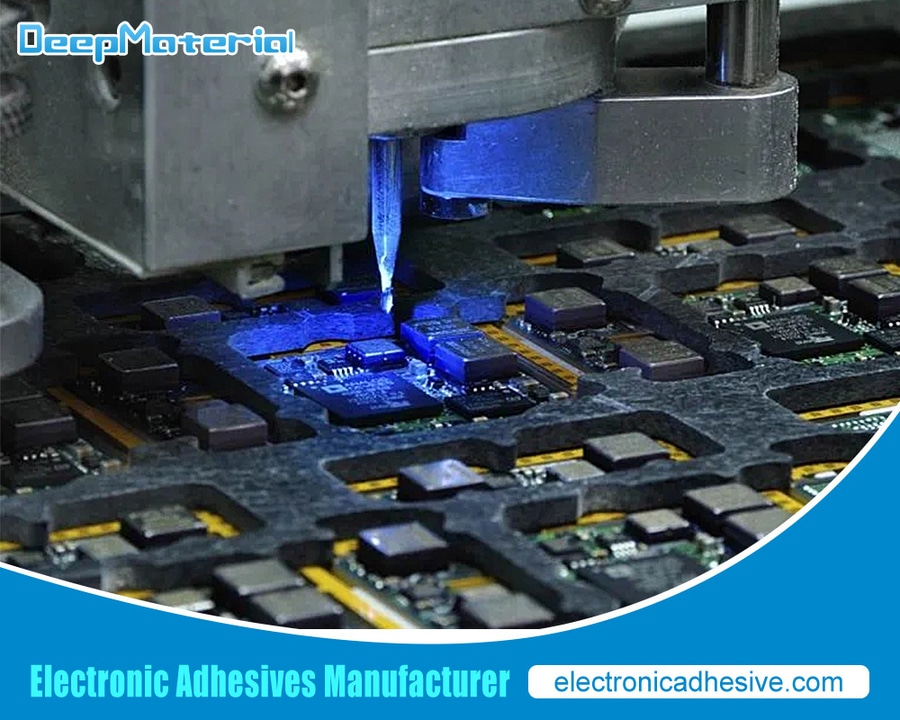
#Industry News
How to Troubleshoot and Fix Common Issues with Industrial Appliance Adhesive
Best Industrial Appliance Adhesive Glue Manufacturer
In the world of industrial appliances, strength and durability are not just desirable attributes – they are absolute necessities. These heavy-duty machines are the backbone of countless industries, from manufacturing to food processing, and their smooth operation is critical to maintaining productivity and efficiency. One key component that ensures this seamless functionality is the industrial appliance adhesive. This powerful bonding agent holds together various parts of these appliances, ensuring they withstand the rigors of daily use.
However, even the mightiest adhesive can sometimes falter under the relentless pressure of industrial operations. When this happens, it’s not just a minor inconvenience; it can lead to significant downtime, costly repairs, and even safety hazards. But fear not! Whether you’re a seasoned maintenance professional or a novice operator looking to expand your troubleshooting skills, this blog post is your ultimate guide.
We will delve deep into the world of industrial appliance adhesives, exploring common issues that can arise and providing practical solutions to get your machines back up and running in no time. From understanding why your adhesive isn’t sticking as it should, to figuring out why it’s curing too quickly or too slowly – we’ve got you covered.
Common Issues with Industrial Appliance Adhesive
Despite their importance, industrial appliance adhesives can sometimes experience issues that compromise their effectiveness. Some common problems include adhesive failure, weak bonding, premature aging, and poor adhesion to certain surfaces.
Adhesive failure occurs when the bond between the adhesive and the surfaces it is meant to join weakens or breaks completely. This is due to factors such as improper surface preparation, environmental conditions, or even incorrect adhesive selection.
Weak bonding refers to a situation where the adhesive does not provide a strong enough bond between the surfaces it is meant to join. This can result in components becoming loose or detached, leading to appliance malfunction.
Premature aging occurs when the adhesive deteriorates or loses its effectiveness before its expected lifespan. This can be caused by exposure to harsh environmental conditions, such as extreme temperatures or chemicals.
Poor adhesion to certain surfaces can be a result of using an adhesive that is not compatible with the material it is meant to bond. This can lead to weak bonding or complete failure of the adhesive.
Understanding the Causes of Adhesive Failure
In order to troubleshoot and fix adhesive issues, it is important to understand the causes of adhesive failure. Some common causes include environmental factors, improper surface preparation, incorrect adhesive selection, and inadequate curing time.
Environmental factors such as temperature, humidity, and exposure to chemicals can have a significant impact on the performance of industrial appliance adhesives. Extreme temperatures can cause the adhesive to become brittle or lose its bonding strength, while high humidity can interfere with the curing process. Exposure to chemicals can also degrade the adhesive over time.
Improper surface preparation is another common cause of adhesive failure. If the surfaces to be bonded are not properly cleaned, sanded, or degreased, the adhesive may not adhere properly and the bond may be weak or fail completely.
Incorrect adhesive selection is a common mistake that can lead to adhesive failure. Different adhesives are designed for use with specific materials and surfaces. Using the wrong adhesive can result in poor adhesion or weak bonding.
Inadequate curing time is another factor that can contribute to adhesive failure. Adhesives require a certain amount of time to fully cure and develop their maximum bonding strength. If the adhesive is not given enough time to cure, the bond may be weak or fail completely.
Tools and Materials Needed for Troubleshooting and Fixing Adhesive Issues
When troubleshooting and fixing adhesive issues in industrial appliances, there are several tools and materials that may be needed. These include adhesive remover, sandpaper, solvent, new adhesive, and an applicator.
Adhesive remover is used to remove old or failed adhesive from surfaces. It helps to dissolve the adhesive, making it easier to remove.
Sandpaper is used to roughen the surfaces to be bonded, ensuring better adhesion. It helps to create a rough surface that the adhesive can grip onto.
Solvent is used to clean surfaces before applying new adhesive. It helps to remove any dirt, grease, or other contaminants that may interfere with adhesion.
New adhesive is needed to replace the old or failed adhesive. It is important to select an adhesive that is compatible with the materials and surfaces to be bonded.
An applicator, such as a brush or a syringe, is used to apply the adhesive to the surfaces. It helps to ensure even coverage and proper application of the adhesive.
Steps to Remove and Replace Failed Adhesive
Once the type of adhesive has been identified, the next step is to remove the failed adhesive and replace it with a new one. This process involves several steps, including surface preparation, adhesive removal, new adhesive application, and curing time.
Surface preparation is an important step in ensuring proper adhesion. It involves cleaning the surfaces to be bonded, sanding them to create a rough surface, and degreasing them to remove any contaminants.
Adhesive removal is done using an adhesive remover or solvent. The old or failed adhesive is dissolved and removed from the surfaces using a brush or a cloth.
New adhesive is then applied to the prepared surfaces using an applicator. It is important to follow the manufacturer’s instructions for proper application and coverage.
After applying the new adhesive, it needs to be allowed to cure for a certain amount of time. This ensures that the adhesive develops its maximum bonding strength. The curing time can vary depending on the type of adhesive used.
Conclusion
Industrial appliance adhesive plays a crucial role in ensuring the proper functioning of industrial appliances. Understanding the common issues and their causes can help troubleshoot and fix adhesive problems. Proper surface preparation, adhesive application, and testing can ensure strong bonding. Preventive measures, such as proper storage, correct application, regular maintenance, and quality control, can help avoid future adhesive failure. By following these guidelines, industrial appliance manufacturers and users can ensure that their appliances remain in optimal condition and perform reliably.
For more about choosing the Troubleshoot and Fix Common Issues with Industrial Appliance Adhesive, you can pay a visit to DeepMaterial at https://www.electronicadhesive.com/about/ for more info.