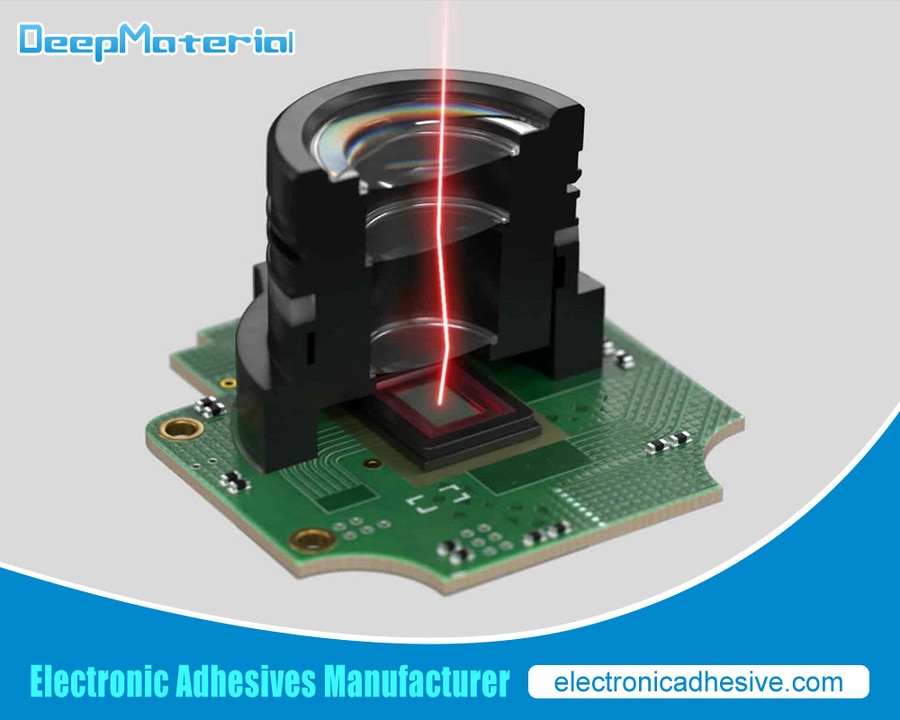
#Industry News
Exploring the Latest Innovations in Electronics Assembly Adhesives for High-Temperature Applications
Best Electronic Assembly Adhesive Glue Manufacturer
High-temperature electronics assembly adhesives play a crucial role in various industries, including automotive, aerospace, and electronics manufacturing. These adhesives are designed to withstand extreme temperatures and provide strong bonds between components. They are used in applications such as bonding circuit boards, attaching heat sinks, and sealing electronic enclosures. The importance of high-temperature electronics assembly adhesives cannot be overstated, as they ensure the reliability and performance of electronic devices in harsh environments.
Introduction to High-Temperature Electronics Assembly Adhesives
High-temperature electronics assembly adhesives are specially formulated adhesives that can withstand temperatures above 150°C (302°F). They are designed to provide strong bonds between components and substrates, even in extreme heat conditions. These adhesives are used in a wide range of applications, including bonding electronic components to circuit boards, attaching heat sinks to electronic devices, and sealing electronic enclosures.
The primary function of high-temperature electronics assembly adhesives is to provide a reliable and durable bond that can withstand the high temperatures encountered in various industries. These adhesives are formulated to resist thermal cycling, which is the repeated expansion and contraction of materials due to temperature changes. They also offer excellent chemical resistance, ensuring that the bond remains intact even in the presence of harsh chemicals or solvents.
Importance of Adhesives in High-Temperature Applications
High-temperature applications present unique challenges that require specialized adhesives. In these environments, traditional mechanical fasteners such as screws or bolts may not be suitable due to their limited ability to withstand extreme temperatures. Adhesives offer a more reliable and efficient solution for bonding components in high-temperature applications.
One of the main challenges in high-temperature applications is thermal cycling. Components and substrates expand and contract at different rates when exposed to temperature changes, leading to stress on the bond. High-temperature electronics assembly adhesives are designed to withstand these thermal stresses, ensuring that the bond remains intact even after repeated temperature cycles.
Adhesives also play a crucial role in sealing electronic enclosures in high-temperature applications. These enclosures protect sensitive electronic components from dust, moisture, and other contaminants. High-temperature adhesives provide a strong and durable seal that can withstand the harsh conditions encountered in these environments.
Types of Adhesives Used in High-Temperature Electronics Assembly
There are several types of adhesives used in high-temperature electronics assembly, each with its own advantages and limitations. Some of the most commonly used types include epoxy adhesives, silicone adhesives, and polyimide adhesives.
Epoxy adhesives are widely used in high-temperature applications due to their excellent thermal stability and chemical resistance. They offer high bond strength and can withstand temperatures up to 200°C (392°F). However, epoxy adhesives can be brittle and may require careful handling to prevent cracking or delamination.
Silicone adhesives are another popular choice for high-temperature electronics assembly. They offer excellent flexibility and can withstand temperatures up to 300°C (572°F). Silicone adhesives also provide good resistance to moisture, chemicals, and UV radiation. However, they may not offer the same level of bond strength as epoxy adhesives.
Polyimide adhesives are known for their exceptional thermal stability and resistance to high temperatures. They can withstand temperatures up to 400°C (752°F) and offer excellent chemical resistance. Polyimide adhesives are commonly used in applications such as bonding flexible circuits and attaching heat sinks. However, they can be expensive and may require specialized equipment for application.
Advancements in Adhesive Technologies for High-Temperature Applications
In recent years, there have been significant advancements in adhesive technologies for high-temperature applications. These advancements have led to the development of adhesives with improved performance and reliability in extreme heat conditions.
Nanocomposite adhesives are a significant breakthrough in the field of adhesives and bonding technology. These adhesives are made up of a combination of polymers and nanoparticles, which work together to create a stronger and more durable bond. The nanoparticles used in these adhesives are typically made from materials such as silica, alumina, or carbon nanotubes, which have unique properties that enhance the adhesive’s performance.
One of the most significant benefits of nanocomposite adhesives is their improved thermal stability. Traditional adhesives can break down or lose their strength when exposed to high temperatures, but nanocomposite adhesives can withstand much higher temperatures without degrading. This makes them ideal for use in high-temperature applications such as aerospace and automotive manufacturing. In addition to their thermal stability, nanocomposite adhesives also offer improved mechanical properties.
Hybrid adhesives have become increasingly popular in recent years due to their ability to combine the best properties of different adhesive types. One such advancement is the use of hybrid epoxy-silicone adhesives, which offer the flexibility of silicone adhesives and the high bond strength of epoxy adhesives. This combination provides a versatile solution for high-temperature applications, where traditional adhesives may fail due to their inability to withstand extreme heat.
These hybrid adhesives can also be used in a variety of other applications, including automotive, aerospace, and electronics industries. They are particularly useful in situations where a strong bond is required, but flexibility is also necessary to accommodate movement or vibration.
Overall, the use of hybrid adhesives represents a significant advancement in adhesive technology and provides engineers and manufacturers with a valuable tool for solving complex bonding challenges.
Future Trends in Electronics Assembly Adhesives for High-Temperature Applications
The future of electronics assembly adhesives for high-temperature applications is promising, with several trends and advancements on the horizon. These trends include the development of adhesives with even higher temperature resistance, improved chemical compatibility, and enhanced bond strength.
One of the future trends is the development of adhesives that can withstand even higher temperatures. Researchers are exploring new materials and formulations that can withstand temperatures above 400°C (752°F), opening up new possibilities for high-temperature applications in industries such as aerospace and energy.
Another trend is the development of adhesives with improved chemical compatibility. Researchers are working on formulating adhesives that can resist a wider range of chemicals and solvents, ensuring the integrity of the bond in even the harshest environments.
Enhanced bond strength is also a focus of future developments in electronics assembly adhesives. Researchers are exploring new adhesive technologies and surface treatments that can improve the bond strength and durability of high-temperature adhesives, ensuring reliable performance in extreme conditions.
Final Recommendations
In conclusion, high-temperature electronics assembly adhesives play a crucial role in various industries by providing strong and reliable bonds between components in extreme heat conditions. These adhesives offer numerous benefits, including improved reliability, increased efficiency, and cost savings.
There are several types of adhesives used in high-temperature electronics assembly, each with its own advantages and limitations. Recent advancements in adhesive technologies have led to the development of adhesives with improved performance and reliability in extreme heat conditions.
For more about choosing the electronics assembly adhesives, you can pay a visit to DeepMaterial at https://www.electronicadhesive.com/about/ for more info.