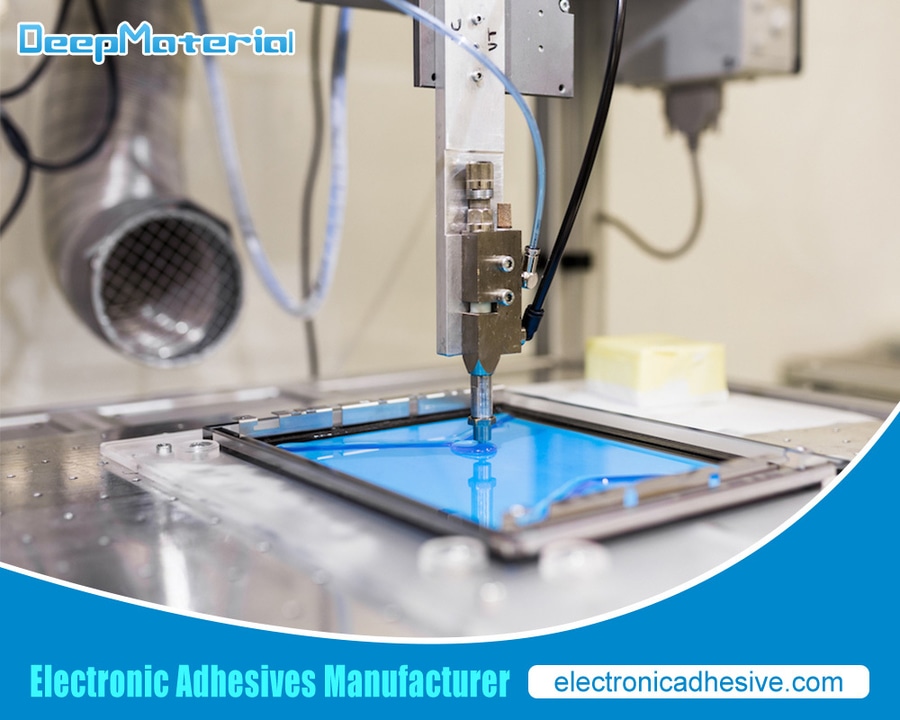
#Industry News
Evaluating the Impact of EV Battery Box Bonding Adhesive on Thermal Management
Best EV Battery Box Bonding Adhesive Glue Manufacturer
As we march into a greener future, EVs have been skyrocketing in fame due to their minuscule carbon footprints. A crucial piece of every EV car is the battery pack, which needs exceptional thermal management to stay up and running for an extended time – enter bonding adhesives.
Recently, folks have been embracing this nifty adhesive for assembling EV battery boxes, and it’s becoming more significant than ever! So today, let’s closely examine how bond adhesive impacts thermal management: what good does it bring and any bottlenecks it may cause?
What is EV Battery Box Bonding Adhesive?
Electric vehicle battery box bonding adhesive is integral to electric car production – it holds a uniquely essential purpose. It’s the bond between the pack’s battery modules and cooling plates, ensuring maximum structural integrity and safety. It also guarantees optimal heat transfer between components for improved performance on the road. But perhaps more importantly, it helps distribute and manage any mechanical stresses or vibrations so drivers can get top-notch reliability and protection out of their cars. It’s worth all that buzz!
Reduced weight and size
In electric vehicle (EV) battery pack assembly, bonding adhesives are a real game-changer. Making traditional mechanical fastening methods look antiquated, their ability to shave off both size and weight makes them essential for crafting peak efficiency and range in vehicles. From an engineering standpoint, this lightweight quality is crucial in optimizing the power-to-weight ratio, ultimately affecting how far you can go on a single charge – every mile counts!
On top of that, thanks to its compact design capabilities, adhesives bestow a significant leg up on saving space within the battery box. You don’t need extra clearance like other mounting options; with adhesive applications made easy and hassle-free, there’s so much more room available for packing those batteries inside, upping energy storage capacity, which translates into increased power over extended periods. Clever solutions like these have truly revolutionized EV technology as we know it today!
Enhanced Structural Integrity
Bonding adhesives are essential in boosting the power of the battery pack structure in electric cars (EVs). Such a solid bond provided by these glues is a must for sustaining the firmness and dependability of the battery, given all conditions EVs endure while running – such as tremors and impacts.
Electric vehicles face various variable environments, covering rocky roads, out-of-the-blue speeding up or slowing down, and maybe even lucky escapes from accidents. The bonding adhesive smooths out any shock or pressure those car parts feel, drastically decreasing their chances of destruction or breakdown.
Improved Resistance to Environmental Factors
Electric vehicle battery boxes need ultra-strong adhesives to perform under the harshest conditions – from extreme hot and cold temperatures to altitude changes, high humidity levels or chemicals in the background. After all, these batteries have a long journey ahead of them.
That’s why EV companies rely on specially formulated adhesives that can stand up against wild temperature swings. It might sound like no small feat – and it isn’t – but this extra layer of protection safeguards an electric car’s structural integrity for years down the road.
Challenges in Thermal Management
In heating and cooling within EV battery systems, bonding adhesives offer tantalizing advantages but pose some problematic issues that must be scrutinized. Of utmost difficulty is the possibility of supposing an increase in thermal impedance at the adhesive connection, which could meddle with heat change-over and bluff the overall temperature performance of this battery package.
Applying bonding adhesives creates an extra layer between battery components, which hampers heat transfer efficiency. That’s like putting the brakes on how well it can debunk this heat, impacting its performance and even safety. Plus, it heightens operating temps that could shorten its lifespan. It’s all connected—an unexpected domino effect we don’t want to miss out on!
Manufacturers have to pick out bonding glues with low thermal resistance attributes tactfully. Opting for adhesives with minimal opposition against heat exchange enables them to contain the likelihood of the thermal impedance increasing at the adhesive connection. That way, they can be sure that warmness flows effortlessly via this bond, sustaining excellent temperature control and protecting conglomerates from going up in excessive smoke – if you get the drift!
Compatibility With Battery Materials
Regarding regulating temperatures in electric vehicle battery systems, bonding adhesives have numerous perks. However, there’s a catch – they may elevate thermal resistance at the adhesive interface, which could slow down heat transfer and hamper the overall cooling of the battery pack. You’ve got to weigh all your options before making this important decision!
Applying bonding adhesives adds an extra barrier between the battery components, like throwing a blanket over them. This layer affects how easily heat can run through it and can impact how the battery pack dissipates heat – reducing its ability to let it go. In hindsight, this could lead to higher temps in operation, which isn’t good news for the performance, lifecycle or safety of your battery system.
Future Development And Advancement
The EV technology arena constantly shifts, and the expectation for adhesive improvements runs high. For instance, researchers are looking at creating adhesives with better thermal conductivity to provide better heat dissipation inside battery packs. And that’s not all! Self-healing or reflow capabilities may be incorporated into this innovation to ensure long-term reliability even when there is minor wear and tear.
Moreover, environmental protection has been paramount in developing these adhesives – they must be free from toxic chemicals. Last but never least, intelligent functionalities embedded within them might also appear on the scene, like sensors which assist in real-time monitoring of battery efficiency…words worth bearing in mind! These advancements illustrate continued progress towards perfecting EV tech and optimizing eco practices in the automotive field we know so well.
Wrapping Up
The role of EV battery box bonding adhesive in temperature management is enormous! It can help significantly with better heat conduction, less bulk and size, a more solid construction, plus resilience to external elements. But risks, too- like extra thermal resistance or not agreeing with the battery materials – need consideration. If you pick an adhesive carefully and follow the best application and steadfast trial testing practices, those EVs will reach peak performance without compromising their durability. A sustainable future awaits, after all!
For more about choosing the Impact of EV Battery Box Bonding Adhesive on Thermal Management, you can pay a visit to DeepMaterial at https://www.electronicadhesive.com/about/ for more info.