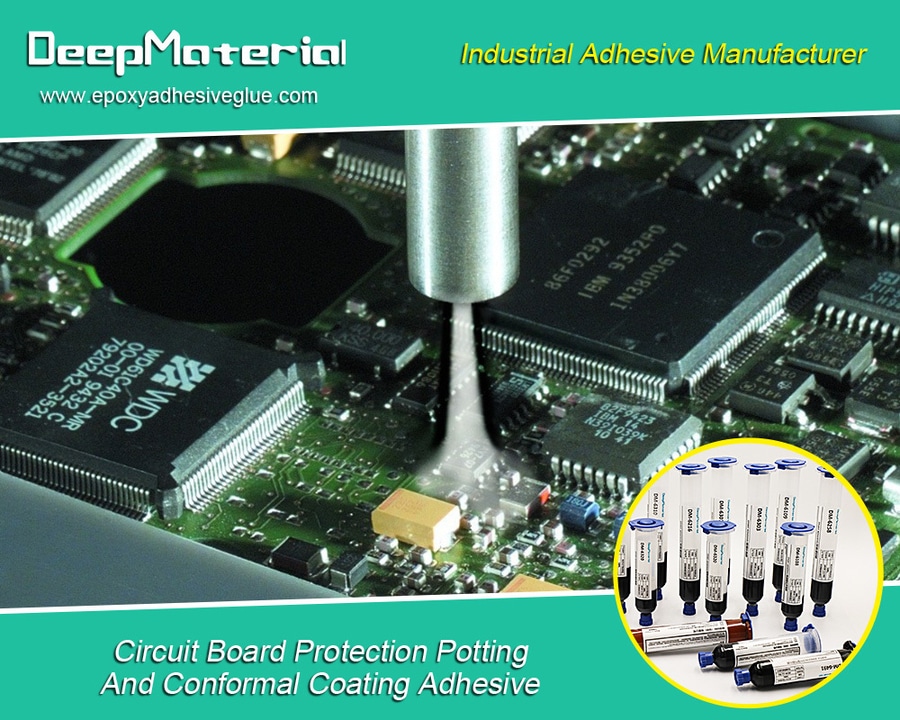
#Industry News
Discover the Benefits of Non Conductive Coating for Electronics
Best Non Conductive Coating Adhesive Glue Manufacturer for Electronics
Non-conductive coatings, also known as insulating coatings, are materials that inhibit the flow of electricity. They serve as a protective barrier between electronic components and potential sources of electrical discharge or interference. But what exactly makes these coatings so beneficial? How do they contribute to the longevity and reliability of electronic devices? And why should manufacturers and consumers alike pay attention to this seemingly minor yet crucial aspect of electronic design?
Join us as we unravel these questions, providing you with a comprehensive understanding of non-conductive coatings and their role in enhancing the functionality and lifespan of your electronic devices. Whether you’re an electronics manufacturer seeking to improve your products, a technician looking for better maintenance solutions, or a consumer aiming to get the most out of your devices, this exploration into non-conductive coatings will offer valuable insights for all.
Understanding the Importance of Non Conductive Coating for Electronics
Electronics can be damaged by conductive coatings due to the presence of electrical conductivity. When a conductive coating comes into contact with electronic components, it can create a short circuit, leading to malfunction or even complete failure of the device. This can result in costly repairs or replacements, as well as potential safety hazards.
Preventing damage to electronics is of utmost importance, as these devices are often expensive and contain valuable data. Non conductive coating provides a barrier between the electronic components and any conductive materials, preventing electrical conductivity and protecting the device from damage.
How Non Conductive Coating Protects Electronics from Damage
Non conductive coating works by creating a protective layer on the surface of electronic components. This layer acts as an insulator, preventing electrical conductivity and protecting the device from damage. The coating is typically made of materials such as silicone or acrylic, which have high dielectric strength and low electrical conductivity.
Examples of how non conductive coating can protect electronics include preventing moisture ingress, preventing corrosion, and providing insulation against electrical conductivity. Moisture ingress can lead to short circuits and corrosion, which can cause irreversible damage to electronic components. Non conductive coating acts as a barrier against moisture, preventing these issues from occurring.
Advantages of Using Non Conductive Coating for Electronics
There are several advantages to using non conductive coating for electronics. Firstly, it increases the durability and longevity of electronic devices. By providing a protective layer, the coating helps to prevent damage from electrical conductivity, moisture, and corrosion. This extends the lifespan of the device and reduces the need for repairs or replacements.
Secondly, non conductive coating improves the performance and reliability of electronic devices. By preventing short circuits and other electrical issues, the coating ensures that the device functions properly and consistently. This is especially important in industries where reliability is crucial, such as aerospace or medical.
Lastly, using non conductive coating can result in cost savings in the long run. By protecting electronic devices from damage, the need for repairs or replacements is reduced. This can result in significant cost savings for both manufacturers and end users.
Non Conductive Coating vs. Traditional Coating for Electronics
Non conductive coating differs from traditional coating in several ways. Traditional coatings are often conductive, meaning they can create a path for electrical conductivity and potentially cause damage to electronic components. Non conductive coating, on the other hand, provides insulation against electrical conductivity, preventing damage.
One advantage of traditional coatings is that they can provide additional benefits such as thermal conductivity or EMI shielding. However, these benefits may not be necessary or desirable for all applications. Non conductive coating focuses solely on protecting electronic components from damage caused by electrical conductivity.
Applications of Non Conductive Coating in Electronics Industry
Non conductive coating is used in a wide range of industries within the electronics industry. Some examples include consumer electronics, automotive electronics, aerospace electronics, and medical electronics. In these industries, electronic devices are often exposed to harsh environments or high levels of moisture, making non conductive coating essential for protection.
Specific applications of non conductive coating in the electronics industry include PCBs (printed circuit boards), connectors, sensors, and displays. These components are often exposed to moisture or other conductive materials, making them susceptible to damage. Non conductive coating provides a protective barrier, ensuring the reliability and longevity of these components.
How to Apply Non Conductive Coating on Electronics
Applying non conductive coating on electronics requires careful attention to detail and proper technique. Here is a step-by-step guide to applying non conductive coating:
Clean the surface: Before applying the coating, ensure that the surface is clean and free of any contaminants. This can be done using a cleaning solution and a lint-free cloth.
Prepare the coating: Mix the non conductive coating according to the manufacturer’s instructions. This may involve diluting the coating with a solvent or adding a catalyst.
Apply the coating: Use a brush, spray gun, or dip method to apply the coating evenly onto the surface of the electronic component. Ensure that the coating covers all areas that need protection.
Cure the coating: Allow the coating to cure according to the manufacturer’s instructions. This may involve air drying or using a curing oven.
Tips for ensuring proper application of non conductive coating include wearing gloves and protective eyewear, working in a well-ventilated area, and following the manufacturer’s instructions carefully.
Future of Non Conductive Coating in Electronics Industry
The future of non conductive coating in the electronics industry looks promising, with potential for growth and development. As electronic devices become more advanced and complex, the need for reliable protection against electrical conductivity will continue to increase.
New technologies and advancements in non conductive coating are also being developed. For example, researchers are exploring the use of nanomaterials in non conductive coatings, which could provide even better protection and performance.
Conclusion
In conclusion, non conductive coating is an essential part of protecting electronics from damage caused by electrical conductivity. It provides a barrier between electronic components and conductive materials, preventing short circuits and other electrical issues. By using non conductive coating, electronic devices can benefit from increased durability and longevity, improved performance and reliability, and cost savings in the long run. It is important for industries within the electronics industry to consider using non conductive coating to ensure the protection and reliability of their electronic devices.
For more about choosing the Benefits of Non Conductive Coating for Electronics, you can pay a visit to DeepMaterial at https://www.epoxyadhesiveglue.com/category/epoxy-adhesives-glue/ for more info.