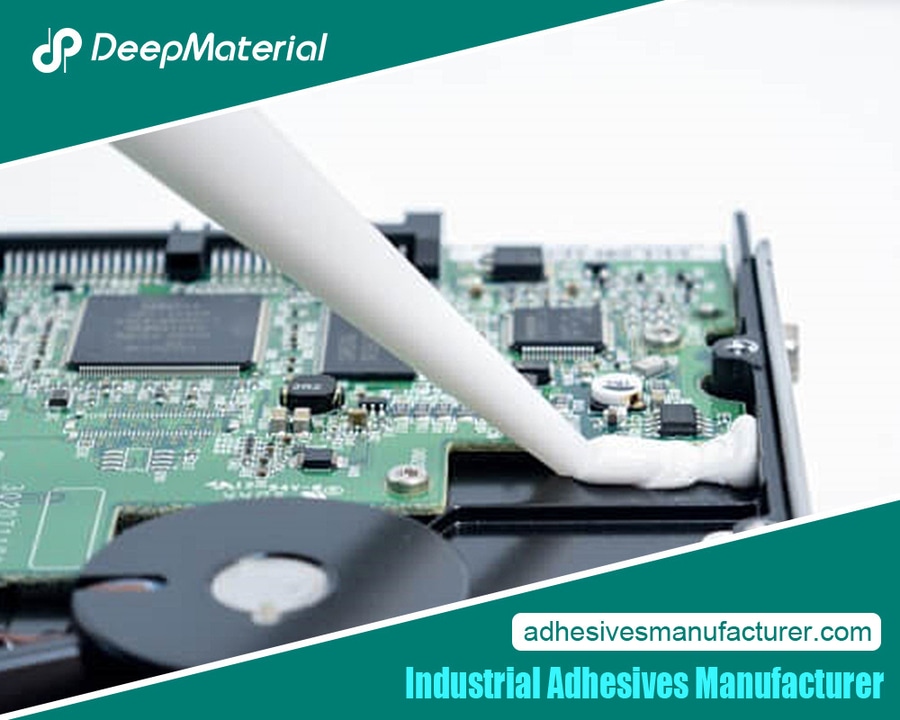
#Industry News
Exploring the Different Coating Techniques Used By a Pressure-Sensitive Adhesive Manufacturer
Best Pressure-Sensitive Adhesive Glue Manufacturer
The art and science of creating everyday products is a complex process, teeming with intricate components often unseen. Take pressure sensitive adhesive (PSA) manufacturing, a simple technique that hides a deep pooling of materials knowledge beneath the surface.
In this article, we’ll journey through the must-know details of coating techniques adopted by PSA manufacturers and discover all their many nuances; whether you’re highly experienced in industry protocol or just beginning your journey, it’s bound to be quite the ride!
Understanding the Different Types of Coating Techniques
With the vast array of pressure sensitive adhesive manufacturing processes out there, it can take time to pinpoint which one is best – each has its advantages and drawbacks depending on a variety of factors like need for adhesion properties, total volume needed, and cost.
The most popular ways to apply these coatings are roll coating, slot die coating, gravure coating, spray coating, extrusion coating, and hot melt coating. It’s remarkable how all these techniques combine to offer something unique for different situations; further complicating the decision-making process!
You’ve got your plate full when deciding which one holds up. It would be best to consider factors such as what thickness the material needs to be applied at or even given little things like possible substrate type requirements and even infrastructure available. Not only that, but costs come into play more than ever in this scenario, so if your heart is set on a specific method, don’t let sticker shock stand in your way!
Roll Coating: A Popular Coating Technique for Pressure Sensitive Adhesives
Roll coating is all the rage when it comes to pressure-sensitive adhesive manufacturing. This technique whips up reliable results with a skillful combination of speed and cost-effectiveness: a rotating roller applies the adhesive, transferring it evenly onto the substrate.
But what makes roll coating so magical is its ability for accurate control over thickness—so consistent performance can be expected in each batch. And that same precision comes at no extra expense, so roll coating has become an ideal choice for high-volume production projects.
However, there are some downsides too, mainly in thin layer difficulties (try achieving uniformity there!) or unavoidable waste due to leftovers sticking on little nooks of the cylinder. Moreover, depending on your substrate material, roll coating may not provide satisfactory adhesion in some cases – so think twice before jumping aboard this train!
Nothing beats roll coating when dealing with applications such as label making, tape factories and graphic art stuff – and accuracy/uniformity obsession levels are off the charts!
Slot Die Coating: A Precise Coating Technique for Pressure Sensitive Adhesives
Slot die coating is regarded as a reliable and efficient way of creating pressure-sensitive adhesives. This technique applies the bond through a slot into the substrate, bringing all sorts of advantages to production lines. For instance, it gives tremendous fineness in controlling glue thickness for constant performance, plus even coverage across substrates, which spells bye-bye to costly mistakes. It’s super-fast, too: perfect for those high-volume jobs!
Don’t get it wrong though – there are some downsides to this type of coating such as specialized equipment necessities resulting in increased expenditure, and then rapid changes due to temperature indicators or viscosity may lead to substandard finishes. Moreover, certain materials won’t adhere whatsoever meaning slot die coating just won’t cut it!
Nevertheless. things like label manufacture, sticky tape output and medical device assembly tend to be entirely happy with slot die technology – where consistency and exactness matter more.
Gravure Coating: A High-Speed Coating Technique for Pressure Sensitive Adhesives
Gravure coating is a popular and effective technique for pressure sensitive adhesive manufacturing. It’s speedy, allowing manufacturers to keep up with large-scale production demands while delivering uniform coatings that provide the exact amount of adhesive needed; it can even achieve ultra-thin layers! But there are some drawbacks: gravure coating requires special tools and can lead to material waste – plus, not all substrates blend well with engraved cells.
Generally speaking, though, gravure coating is often applied in industries such as label making, tape producing, and flexible packaging – particularly when speediness and precise control of thickness matter most.
Spray Coating: An Efficient Coating Technique for Pressure Sensitive Adhesives
Spray coating is a great way to coat up in pressure-sensitive adhesive manufacturing. The technique works by atomizing the adhesive into tiny droplets, before they’re sprayed right onto the substrate. And that’s not all, as using spray coating for production can boast a few significant perks.
Not only does it provide lightning-fast and convenient production – perfect for those vast projects – but it also offers uniform coverage of adhesive across the surface, so you won’t ever have any problems with patchy sprayed layers again. Plus, due to its pleasing misting effect, you can create thin adhesives which will be helpful in jobs where thinner layers matter most!
Unfortunately, there are some drawbacks worth mentioning too – this type of equipment is pretty pricey, and although over spraying may generally be avoided, wastage is inevitable at times too. In addition, specific substrates might’ stand up well against the spray either – so keep an eye open on that side of things! All in all, from label-making to automotive assembly; spray coating proves helpful each time you require swiftness and excellent control over your adhesive thicknesses, just like clockwork.
Extrusion Coating: A Versatile Coating Technique for Pressure Sensitive Adhesives
Extrusion coating is an extraordinary tool for creating pressure sensitive adhesives; it involves forcing the bond through a die to coat a substrate. It offers several benefits, such as rapid high-volume output and even distribution of the adhesive throughout the material.
Plus, there’s potential for thicker layers when required – making it perfect for projects requiring relatively large amounts of glued substance. On the other hand, extrusion coating has its drawbacks – specialized hardware means higher production costs while excess materials become wasted on the die. Also, some substrates struggle to maintain their stickiness with this process.
Nonetheless, Label manufacturing, tape production and flexible packaging regularly go down this route due to its dependable speed and control in terms of characterization thickness.
Last Words on Choosing the Right Coating Technique for Your Pressure-Sensitive Adhesive Needs
Getting the proper coating process is critical for getting your desired PSAs. It would be best if you mulled over various aspects to decide the technique – adhesive thickness, speed, uniformity and substrate. To pick the perfect one for you, jot down what you require from it – characteristics asked of it, volume made every day and expenses included, if any. It’s a great idea to approach a top-notch PSA provider that can tip the scales towards selecting an appropriate coating procedure!
For more about the Different Coating Techniques Used By a Pressure-Sensitive Adhesive Manufacturer, you can pay a visit to Deepmaterial at https://www.adhesivesmanufacturer.com/ for more info.