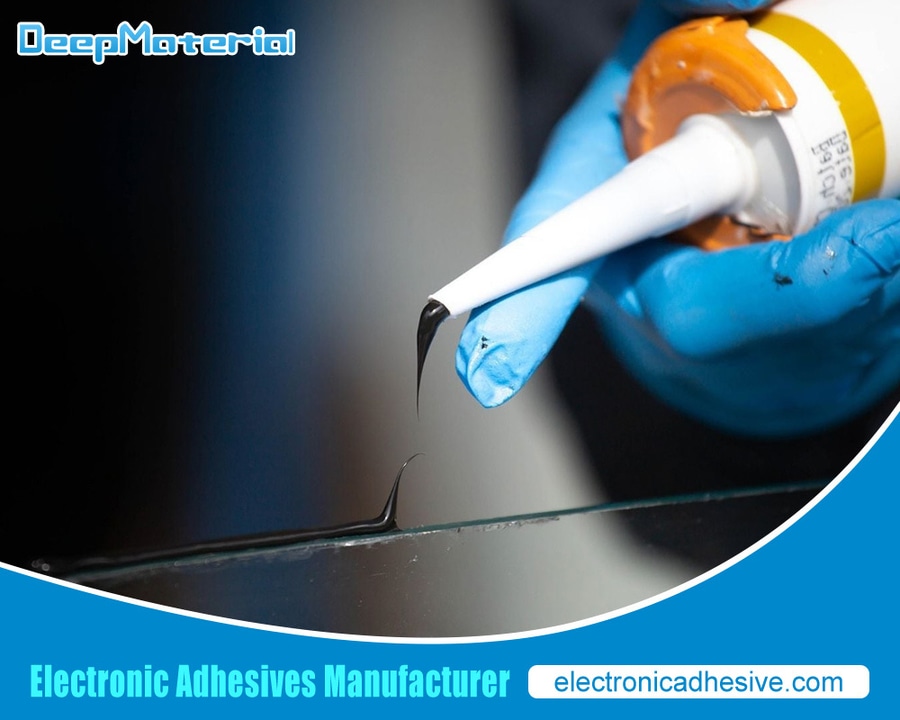
#Industry News
Exploring The Different Types of FPC Bonding Adhesive for Electronics Assembly
Best FPC Bonding Adhesive Glue for Electronics Assembly Manufacturer
FPC bonding adhesive plays a crucial role in the assembly of electronic devices. It is used to bond flexible printed circuits (FPCs) to various substrates, ensuring the electrical connections are secure and reliable. Choosing the right adhesive is essential for successful assembly, as it directly impacts the performance and durability of the final product.
In this article, we will explore the importance of FPC bonding adhesive in electronics assembly and discuss the different types of adhesive available, their properties, advantages, and disadvantages. We will also provide guidance on factors to consider when selecting FPC bonding adhesive, common applications, best practices for application, troubleshooting common issues, and future trends in this field.
Why FPC Bonding Adhesive in Electronics Assembly is Crucial?
FPC bonding adhesive is a specialized adhesive that is used to bond flexible printed circuits (FPCs) to various substrates in electronic devices. FPCs are thin, lightweight, and flexible circuits that are widely used in applications such as mobile devices, automotive electronics, and medical devices. The adhesive plays a critical role in ensuring that the FPC is securely bonded to the substrate, providing electrical connectivity and mechanical stability.
One of the key factors to consider when choosing FPC bonding adhesive is its strength and durability. The adhesive must be able to withstand the stresses and strains that the electronic device may be subjected to during its lifetime. This includes temperature variations, mechanical shocks, vibrations, and exposure to moisture or chemicals. The adhesive should have excellent adhesion properties to ensure that the FPC remains securely bonded to the substrate under these conditions.
Different Types of FPC Bonding Adhesive and Their Properties
There are several types of FPC bonding adhesive available in the market, each with its own unique properties and characteristics. The most common types include acrylic, epoxy, and silicone adhesives.
Acrylic adhesives are known for their excellent adhesion properties and high temperature resistance. They are suitable for applications that require a strong bond and can withstand elevated temperatures. Acrylic adhesives also offer good resistance to moisture and chemicals, making them suitable for outdoor or harsh environments. However, they may not be as flexible as other types of adhesives, which can limit their use in applications that require a high degree of flexibility.
Epoxy adhesives are widely used in electronics assembly due to their excellent bonding strength and durability. They offer high mechanical strength, temperature resistance, and chemical resistance. Epoxy adhesives also have good electrical insulation properties, making them suitable for applications that require electrical connectivity. However, epoxy adhesives can be brittle and may not be suitable for applications that require a high degree of flexibility.
Silicone adhesives are known for their flexibility and excellent temperature resistance. They can withstand extreme temperatures without losing their adhesive properties, making them suitable for applications that require a wide operating temperature range. Silicone adhesives also offer good resistance to moisture and chemicals, making them suitable for outdoor or harsh environments. However, silicone adhesives may not have the same level of bonding strength as acrylic or epoxy adhesives, which can limit their use in applications that require a strong bond.
Advantages and Disadvantages of FPC Bonding Adhesive
Using FPC bonding adhesive in electronics assembly offers several advantages. Firstly, it provides a reliable and secure bond between the FPC and the substrate, ensuring electrical connectivity and mechanical stability. This is especially important in applications where the device may be subjected to temperature variations, mechanical shocks, vibrations, or exposure to moisture or chemicals.
FPC bonding adhesive also offers flexibility in design and assembly. It allows for the use of thin and lightweight FPCs, which can be bent or folded to fit into tight spaces or complex shapes. This flexibility in design enables the development of smaller and more compact electronic devices.
However, there are also some disadvantages to using FPC bonding adhesive. One of the main challenges is the difficulty in rework or repair. Once the FPC is bonded to the substrate, it can be challenging to remove or replace without damaging the components or the substrate. This can increase the cost and time required for repairs or modifications.
Another disadvantage is the potential for delamination or poor adhesion. If the adhesive is not properly selected or applied, it may not provide a strong bond between the FPC and the substrate. This can lead to electrical connectivity issues or mechanical instability, compromising the performance and reliability of the electronic device.
When comparing FPC bonding adhesive to other bonding methods such as soldering or mechanical fastening, each method has its own advantages and disadvantages. Soldering offers a strong and reliable bond, but it requires high temperatures and can be challenging to rework. Mechanical fastening provides flexibility in assembly and rework, but it may not offer the same level of electrical connectivity or mechanical stability as adhesive bonding.
Factors to Consider When Choosing FPC Bonding Adhesive
When selecting FPC bonding adhesive, there are several factors to consider to ensure the adhesive meets the specific requirements of the application. These factors include the substrate material, operating environment, application method, and testing and validation.
The substrate material plays a crucial role in determining the compatibility and adhesion properties of the adhesive. Different adhesives may have different bonding strengths on different substrates. It is important to select an adhesive that is compatible with the substrate material to ensure a strong and reliable bond.
The operating environment is another important consideration. The adhesive should be able to withstand the temperature variations, mechanical shocks, vibrations, and exposure to moisture or chemicals that the electronic device may be subjected to. It is important to select an adhesive that offers the required temperature resistance, flexibility, and chemical resistance for the specific operating environment.
The application method also needs to be considered when selecting FPC bonding adhesive. Different adhesives may require different application methods, such as dispensing, screen printing, or laminating. It is important to select an adhesive that can be easily applied using the chosen method and provides the desired bond strength and durability.
Testing and validation are crucial steps in the selection process. It is important to test the adhesive under the specific conditions and requirements of the application to ensure it meets the desired performance and reliability. This may include testing for adhesion strength, temperature resistance, flexibility, and chemical resistance. It is also important to validate the adhesive with the chosen substrate material and components to ensure compatibility and reliability.
Conclusion: Choosing the Right FPC Bonding Adhesive for Your Electronics Assembly Needs
Selecting the right FPC bonding adhesive is crucial for successful electronics assembly. The adhesive plays a critical role in ensuring the electrical connections are secure and reliable, as well as providing mechanical stability. It is important to consider factors such as adhesive strength, durability, substrate material, operating environment, application method, and testing and validation when choosing FPC bonding adhesive.
For more about choosing the Different Types of FPC Bonding Adhesive for Electronics Assembly, you can pay a visit to DeepMaterial at https://www.electronicadhesive.com/about/ for more info.