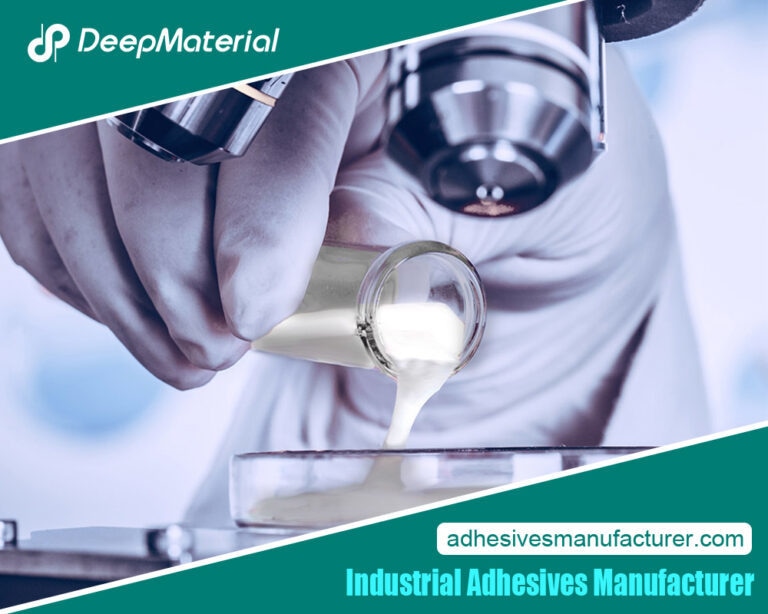
#Industry News
Why OLED Display Module Adhesive is Crucial in Electronics Manufacturing
Best OLED Display Module Adhesive Glue Manufacturer
Adhesive plays an integral part in electronic device production, especially when it comes to OLED displays. Without the strong bonding between components that adhesive provides, these screens would not be able to live up to their superior lifespan and performance standards. Let’s dive into the importance of bonds for manufacturing high-quality OLED displays – from what types are the best fit all the way through to how they could develop in the future.
We’ll look at how different adhesives can affect the productivity and life expectancy of an OLED display, take on board advice about which ones make wise decisions for manufacturers, and consider some of the benefits you get with top-notch adhesive products as well as issues like application techniques and procedures.
Understanding OLED Display Technology
OLED (Organic Light Emitting Diode) display technology is a stellar type of solution that utilizes organic compounds to shine brilliantly when a current runs through it. Unlike LCDs, which rely on an additional backlight, these kinds of displays light up independently – with each pixel literally glowing on its own. Such features make for deeper and inkiest blacks, and then some – contrast ratios are vastly superior while the viewing angle range also gets wider!
If that wasn’t enough already, OLED displays offer quicker response times, far better suited for games and virtual reality scenarios than traditional alternatives could ever dream of matching up to. Plus, let’s not forget their sleek size as well — they tend to be more compact than LCDs, being thin & lightweight enough for the likes of your everyday smartphone or tablet.
How Adhesive Affects OLED Display Performance
The adhesive was a key factor in OLED display production – hastily applied and the wrong kind, it could lead to interacting problems such as delamination, blotchiness, and reduced longevity. Delaminating indicates that different layers of the module haven’t completely bonded; this results in visible crinkles onscreen and could stop pixels from operating correctly.
If not spread evenly enough during the application, discoloration pops up when displaying dark colors or solids, totally messing with expected brightness levels. With warm temperatures inside each device rattling through 24/7, too, using an adhesive fit for purpose seems essential – if not picked aptly, then component quality takes a hit, leading to undesirable consequences down the line.
Factors to Consider When Choosing OLED Display Adhesive
When selecting an adhesive for OLED displays, a few aspects must be taken into account, foremost being compatibility with other components employed in production. The glue should stick well to all of the layers in the OLED display module and any additional materials used. Temperature resistance is just as important since these modules produce plenty of heat – naturally when displaying bright visuals or simply after some extended use.
Plus, it has to withstand bending and flexion that you often see with mobile devices like phones and tablets while keeping its adhesiveness as if nothing happened! Nothing beats a strong bond between every layer making up the display module either – one that holds up no matter what’swhat’s thrown at it like impacts or vibrations.
Types of Adhesive Used in OLED Display Manufacturing
OLED display manufacturing requires the use of special adhesives, each with its own set of pros and cons. For instance, epoxy adhesive offers great strength and temperature resistance but might not be practical for applications that need flexibility. Another option is acrylic adhesive, which does provide some flexibility yet lacks the heat resistance capability that epoxy has.
Finally, there are UV-curable adhesives that deliver prompt curing times with robust adhesion properties. Yet, these cannot hold up to extreme temperatures as well as their counterparts mentioned above. With so many factors taken into consideration, it’s clear why choosing a suitable adhesive can be challenging!
Benefits of Using High-Quality Adhesive in OLED Display Production
Quality adhesive is essential to the production of OLED displays, and with good reason! The durability it provides boosts stability by bonding the layers together firmly, shielding them from external pressures like shock or vibrations. It also guards against delamination – a definite plus for everything involved.
It’s crucial to use top-notch adhesive when it comes to OLED displays – it’ll give you the best chance of holding onto those life-like hues, amazing contrast, and radiant brightness. Plus, this strong stuff can handle extreme heat without weakening or losing its grip! Keeping high-quality adhesive in place means your display will stay flawlessly impressive for many years – guaranteed!
Reliable stickiness can definitely give your OLED display’s performance a longevity boost! This advanced adhesive has the power to stay strong against any beatings it takes from regular use, meaning that manufacturers and customers alike will reap the benefits of huge long-term savings. Let’s not forget how satisfied everyone will be with these results – an exciting win-win for all involved!
Challenges in OLED Display Adhesive Application
Gluing OLED displays can be tricky because of how fragile they are– getting an even gluing so there are no bright spots or visible defects is hard to master. Inconsistencies can end up making the display much less uniform and aesthetically pleasing.
No doubt, aligning the display’s diverse layers during adhesive application is a huge challenge. Every bit of misalignment has dire consequences – from non-functioning pixels that are pointless to catastrophically destroyed displays! You’ve got to position each one just right for it to perform and interface effectively electrically. It’s no wonder, then, why it takes so much effort – any slip-ups would be costly in more ways than one.
Ensuring the desired results, this job requires a precise workspace. Any little bit of dust contamination or any other foreign material can mess with the adhesive and drastically reduce its power to stick that display up securely – no room for sloppiness here!
Conclusion
To sum it up, the adhesive used for OLED display modules plays a significant role in the electronics manufacturing business linked to this technology. It works by holding different levels of displays together firmly and providing longevity to their stability. With that in mind, selecting an appropriate adhesive according to factors such as its capability being compatible with other elements present, temperature resistance capacity, and flexibility alongside strength for adhesion are key points.
By using only high-grade products and following adequate practices when applying the glue, all of us manufacturers can make sure every OLED display does its job properly and will last through time.
For more about a complete guide to industrial adhesive manufacturers and their products, you can pay a visit to Deepmaterial at https://www.adhesivesmanufacturer.com/ for more info.