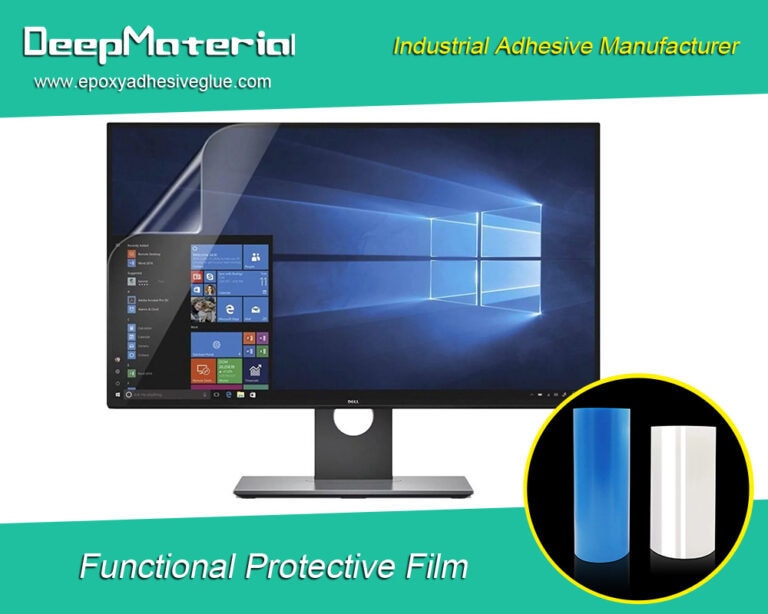
#Industry News
Advancements of the UV Adhesives Industry
Best UV Industry Adhesive Glue Manufacturer
UV adhesives play a crucial role in modern manufacturing processes. These adhesives are unique in that they cure rapidly when exposed to ultraviolet (UV) light, creating strong and durable bonds. They have become increasingly popular in various industries due to their numerous advantages over traditional adhesives. UV adhesives offer faster curing times, stronger bonds, increased durability, and reduced environmental impact.
In this article, we will explore the history of the UV adhesives industry, its advantages over traditional adhesives, its applications in various industries, the different types of UV adhesives and their properties, recent developments in UV adhesives technology, challenges faced by the industry, future prospects, and the environmental impact of UV adhesives.
History of UV Adhesives Industry
The development and use of UV adhesives can be traced back to the early 20th century. The first commercial UV adhesive was introduced in the 1930s and was primarily used in the dental industry. However, it wasn’t until the 1960s that UV adhesives started gaining popularity in other industries such as electronics and automotive.
Advancements in technology and manufacturing processes have played a significant role in the growth of the UV adhesives industry. The development of more efficient UV light sources and the introduction of new formulations and chemistries have greatly improved the performance and versatility of UV adhesives. Today, UV adhesives are widely used in various industries for their fast curing times, high bond strength, and excellent durability.
Advantages of UV Adhesives over Traditional Adhesives
One of the main advantages of UV adhesives is their faster curing times. Traditional adhesives often require hours or even days to fully cure, whereas UV adhesives can cure within seconds or minutes when exposed to UV light. This significantly reduces production time and increases efficiency in manufacturing processes.
UV adhesives also offer stronger bonds compared to traditional adhesives. The rapid curing process allows for better penetration and adhesion to the substrate, resulting in a stronger and more durable bond. This is particularly important in industries such as automotive and aerospace, where the strength of the bond is critical for safety and performance.
In addition to faster curing times and stronger bonds, UV adhesives also offer increased durability. These adhesives are resistant to temperature extremes, moisture, chemicals, and UV radiation, making them ideal for applications that require long-term reliability and performance.
Furthermore, UV adhesives have a reduced environmental impact compared to traditional adhesives. Traditional adhesives often contain volatile organic compounds (VOCs) that can be harmful to human health and the environment. UV adhesives, on the other hand, are solvent-free and emit minimal VOCs during the curing process, making them a more sustainable choice.
Types of UV Adhesives and Their Properties
There are several types of UV adhesives available in the market, each with its own unique properties and characteristics. The most common types of UV adhesives include acrylic, epoxy, silicone, and polyurethane.
Acrylic UV adhesives are known for their excellent bond strength, high clarity, and resistance to yellowing. They are widely used in industries such as automotive, electronics, and medical devices. Acrylic UV adhesives offer good adhesion to a wide range of substrates including metals, plastics, and glass.
Epoxy UV adhesives are known for their high bond strength, chemical resistance, and excellent electrical insulation properties. They are commonly used in the electronics industry for bonding and encapsulating electronic components. Epoxy UV adhesives offer excellent adhesion to metals, ceramics, and most plastics.
Silicone UV adhesives are known for their flexibility, high temperature resistance, and excellent electrical insulation properties. They are commonly used in industries such as automotive, electronics, and medical devices. Silicone UV adhesives offer good adhesion to a wide range of substrates including metals, plastics, and glass.
Polyurethane UV adhesives are known for their flexibility, impact resistance, and excellent adhesion properties. They are commonly used in industries such as automotive, construction, and packaging. Polyurethane UV adhesives offer good adhesion to a wide range of substrates including metals, plastics, and wood.
Recent Developments in UV Adhesives Technology
The UV adhesives industry has witnessed several recent developments in technology and formulations, leading to improved performance and versatility. New formulations and chemistries have been developed to meet the specific requirements of different industries and applications.
One of the recent developments in UV adhesives technology is the introduction of new formulations that offer improved adhesion to difficult-to-bond substrates such as low surface energy plastics and metals. These new formulations provide better wetting and adhesion properties, resulting in stronger and more durable bonds.
Another recent development in UV adhesives technology is the improvement in curing methods. Traditional UV curing methods involve using mercury lamps, which can be hazardous and require special handling. However, new LED-based UV curing systems have been developed, which offer several advantages such as longer lamp life, lower energy consumption, and reduced heat generation.
Furthermore, UV adhesives are increasingly being used in 3D printing processes. UV-curable resins are used as the printing material, and UV light is used to cure the resin layer by layer, resulting in the formation of a solid object. This technology has revolutionized the manufacturing industry by enabling the production of complex and customized parts with high precision and accuracy.
Challenges Faced by UV Adhesives Industry
Despite the numerous advantages of UV adhesives, there are still some challenges that the industry faces. One of the main challenges is the cost of UV adhesives. UV adhesives can be more expensive than traditional adhesives due to the higher cost of raw materials and the specialized equipment required for curing.
Another challenge is the limited compatibility of UV adhesives with certain materials. Some substrates, such as polyethylene and polypropylene, have low surface energy and are difficult to bond with UV adhesives. However, new formulations and surface treatment methods are being developed to improve the adhesion of UV adhesives to these materials.
Safety concerns are also a challenge in the UV adhesives industry. UV light can be harmful to human health and can cause skin and eye damage if proper safety precautions are not taken. It is important for manufacturers and users of UV adhesives to follow safety guidelines and use appropriate protective equipment.
Future Prospects of UV Adhesives Industry
The UV adhesives industry has a promising future with significant growth potential in emerging markets. As industries such as automotive, electronics, and medical devices continue to grow, the demand for UV adhesives is expected to increase. The increasing use of advanced manufacturing processes such as 3D printing is also expected to drive the demand for UV adhesives.
Furthermore, advancements in technology and formulations will continue to improve the performance and versatility of UV adhesives. New formulations that offer improved adhesion to difficult-to-bond substrates and new curing methods that are more efficient and environmentally friendly will further enhance the capabilities of UV adhesives.
Finalizing on The Growing Importance of UV Adhesives in Modern Manufacturing
In conclusion, UV adhesives have become an integral part of modern manufacturing processes due to their numerous advantages over traditional adhesives. The fast curing times, strong bonds, increased durability, and reduced environmental impact offered by UV adhesives make them a preferred choice in various industries such as automotive, electronics, medical devices, packaging, and construction.
For more about Advancements of the UV Adhesives Industry, you can pay a visit to DeepMaterial at https://www.epoxyadhesiveglue.com/category/epoxy-adhesives-glue/ for more info.